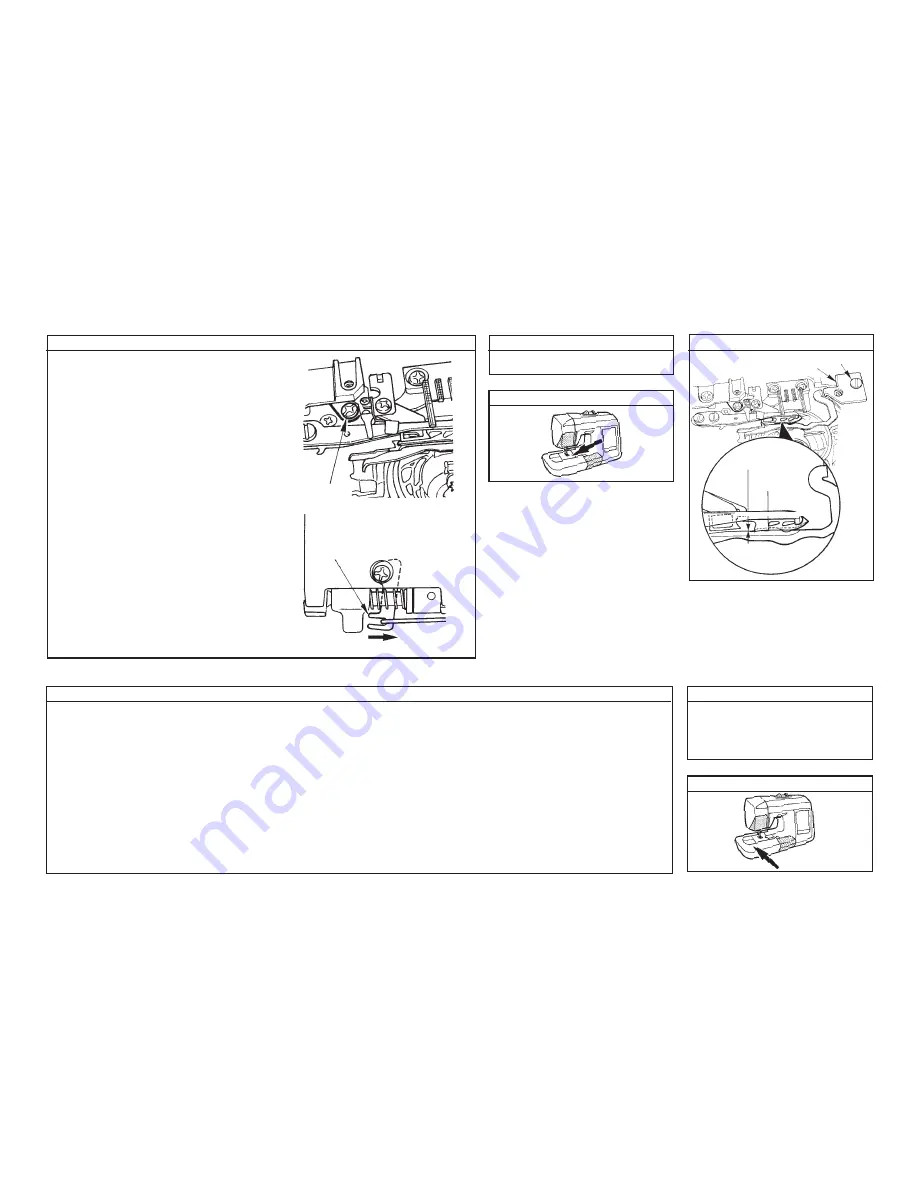
23
(11) Position of the looper
Set the sewing machine to its highest dead point. In this state, loosen screw
3
and adjust so that the play provided between
1
and
2
should
be 0.5 to 1 mm. (Required value is 0.5.)
(12) Adjusting the knife disengagement
Disassembly
Location of components to be adjusted
Throat plate
How to adjust
Disassembly
Location of components to be adjusted
Throat plate and free arm bottom cover
How to adjust
Pressing
4
in the direction of arrow, turn the hook
driving shaft pulley by hand to actuate the moving
knife. Loosen
1
and adjust
2
so that the clearance
provided between the looper and the moving knife
base should be 0
±
0.2 mm when the moving knife
returns, and the end of the left slot of moving knife
base aligns with the corner section of looper as shown
in the illustration below.
<Confirm the looper operation.>
When the looper operation is wrong, loosen screw
3
and adjust so that the looper is located to the
smooth operating position.
* When
3
is loosened, re-confirm the clearance
provided between the moving knife and the looper.
3
4
Adjustment drawing
0
±
0.2 mm
1
2
To align