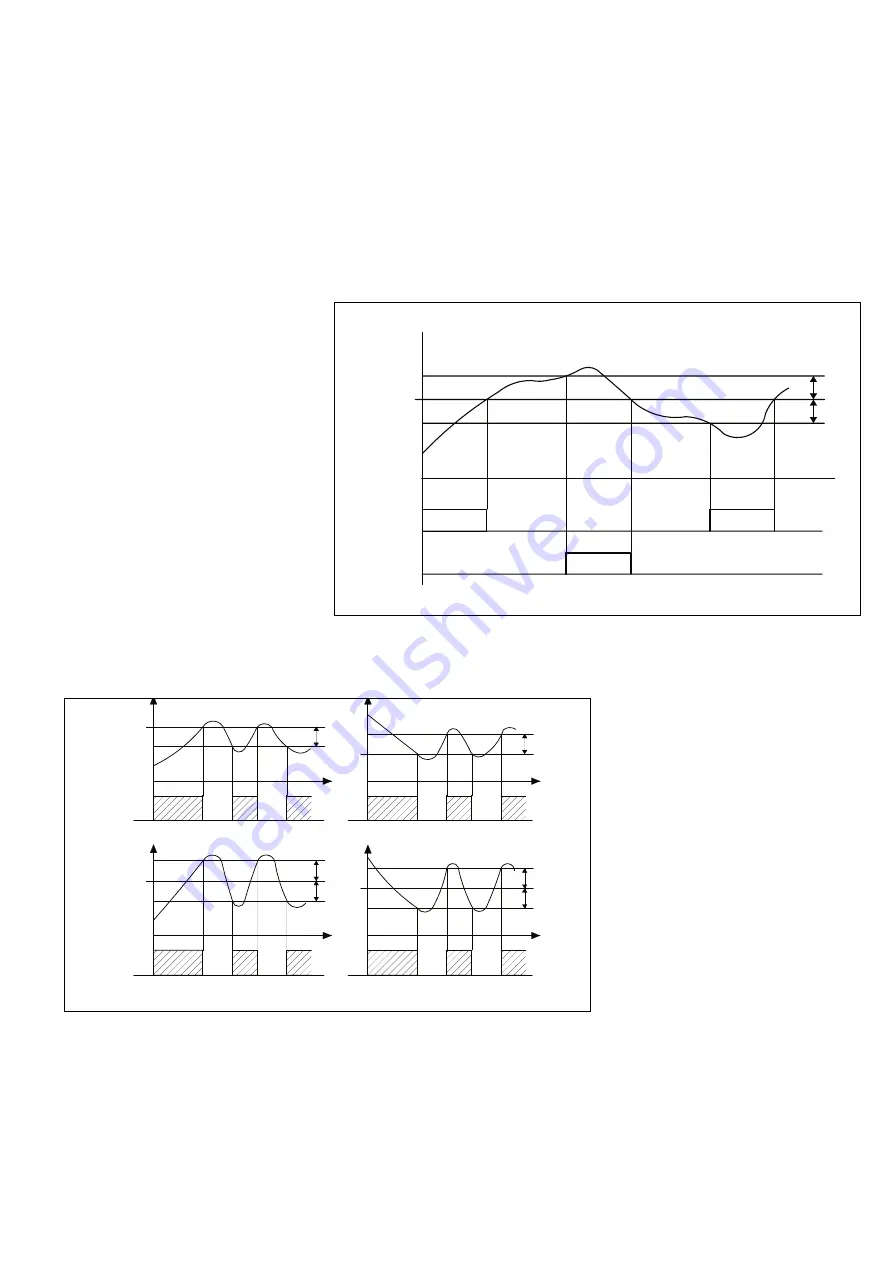
OUTPUTS CONFIGURATION
The instrument’s outputs can be programmed
by entering the group of parameters “]Out,
where the relative parameters “O1F” and “O2F”
(depending on the number of outputs available
on the instrument) are located.
The outputs can be set for the following func-
tions :
• Main control output (1.rEG)
• Secondary control output (2.rEG)
• Alarm output normally open (ALno)
• Alarm output normally closed (ALnc)
• Alarm output normally closed with led reverse
indication (ALni)
• Output deactivated (OFF)
The coupling outputs number outputs – number
alarms can be made in the group referring to
the alarm to the alarm (“]AL1”).
ON/OFF CONTROL (1REG)
All the parameters referring to the ON/OFF
control are contained in the group “]rEG”.
This type of control can be obtained by pro-
gramming par."Cont" = On.FS or = On.FA and
works on the output programmed as 1.rEG,
depending on the measure, on the active Set
Point “SP”, on the functioning mode "Func” and
on the hysteresis "HSEt".
The instrument carries out an ON/OFF control
with symmetric hysteresis if “Cont" = On.FS or
with asymmetrical hysteresis if “Cont” = On.Fa.
The control works in the following way : in the
case of reverse action, or heating
(“FunC”=HEAt), it deactivates the output, when
the process value reaches [SP + HSEt] in case of
symmetrical hysteresis, or [SP] in case of asym-
metrical hysteresis and is then activated again
when the process value goes below value [SP -
HSEt].
Vice versa, in case of direct action or cooling
("Func”=CooL), it deactivates the output, when
the process value reaches [SP - HSEt] in case of
symmetrical hysteresis, or [SP] in case of asym-
metrical hysteresis and is activated again when
the process value goes above value [SP + HSEt].
NEUTRAL ZONE ON/OFF CONTROL (1REG -
2REG)
All the parameters referring to Neutral Zone
ON/OFF control are contained in the group
“]rEG”.
This type of control can be obtained when 2
outputs are programmed respectively as 1rEG
and 2rEG and the par. “Cont” = nr .
The Neutral Zone control is used to control
plants in which there is an element which caus-
es a positive increase (ex. Heater, humidifier,
etc.) and an element which causes a negative
increase (ex. Cooler, de-humidifier, etc).
The control functions works on the pro-
grammed outputs depending on the measure-
ment, on the active Set Point “SP” and on the
hysteresis "HSEt".
The control works in the following way : it deac-
tivates the outputs when the process value
reaches the Set Point and it activates the output
1rEG when the process value goes below value
[SP - HSEt], or it activates the output 2rEG when
the process value goes above [SP + HSEt].
Consequently, the element causing a positive
increase has to be connected to the output pro-
grammed as 1rEG while the element causing a
negative increase has to be connected to the
output programmed as 2rEG.
If 2rEG output is used to control compressor is
possible to use the “Compressor Protection”
function that has the meaning to avoid com-
pressor “short cycles”.
This function allows a control by time on the
output 2rEG activation, independently by the
temperature control request.
The protection is a “delayed after deactivation”
type.
This protection permits to avoid the output
activation for a time programmable on par.
“CPdt” (expressed in sec.); the output activation
will occurs only after the elapsing of time
“CPdt”.
The time programmed on parameter “CPdt” is
counted starting from the last output deactiva-
tion.
Obviously, whether during the time delay
caused by the compressor protection function,
the regulator request should stop, the output
activation foreseen after time “CPdt” would be
erased.
The function is not active programming “CPdt”
=OFF.
The led relative to 2rEG output blinks during
the phases of output activation delay, caused by
“Compressor Protection” function.
SINGLE ACTION PID CONTROL (1REG)
All the parameters referring to PID control are
contained in the group “]rEG”.
The Single Action PID control can be obtained
by programming par."Cont" = Pid and works on
the output 1rEG depending on the active Set
Point “SP”, on the functioning mode "Func” and
on the instrument’s PID algorithm with two
degree of freedom.
In order to obtain good stability of the process
variable, in the event of fast processes, the cycle
time “tcr1” has to have a low value with a very
frequent intervention of the control output.
In this case use of a solid state relay (SSR) is
recommended for driving the actuator.
EWTQ 905
3/8
OUT
SP1
PV
off
ON
HEAt - On.FA
OUT
time
HSEt
SP1
PV
HSEt
time
CooL - On.FA
ON
ON
ON
ON
ON
off
off
off
CooL - On.FS
HEAt - On.FS
ON
ON
OUT
SP1
off
PV
off
ON
HSEt
time
OUT
ON
SP1
PV
ON
off
off
ON
time
HSEt
HSEt
HSEt
1.rEG
1.rEG
1.rEG
1.rEG
0N
OUT 2.rEG
(cooling)
OUT 1.rEG
(heating)
SP1
PV
off
0N
off
off
off
0N
time
HSEt
HSEt
,,
,,,,
,,,,,
,,,,,
,,,,
,,,
,
,,,
,,
,
,
,,
,
,,
,,
,
,,
,,,,
,,
,,
,,,,
,,
,
,,
,,
,
,,
,,
,
,,
,,,,
,,