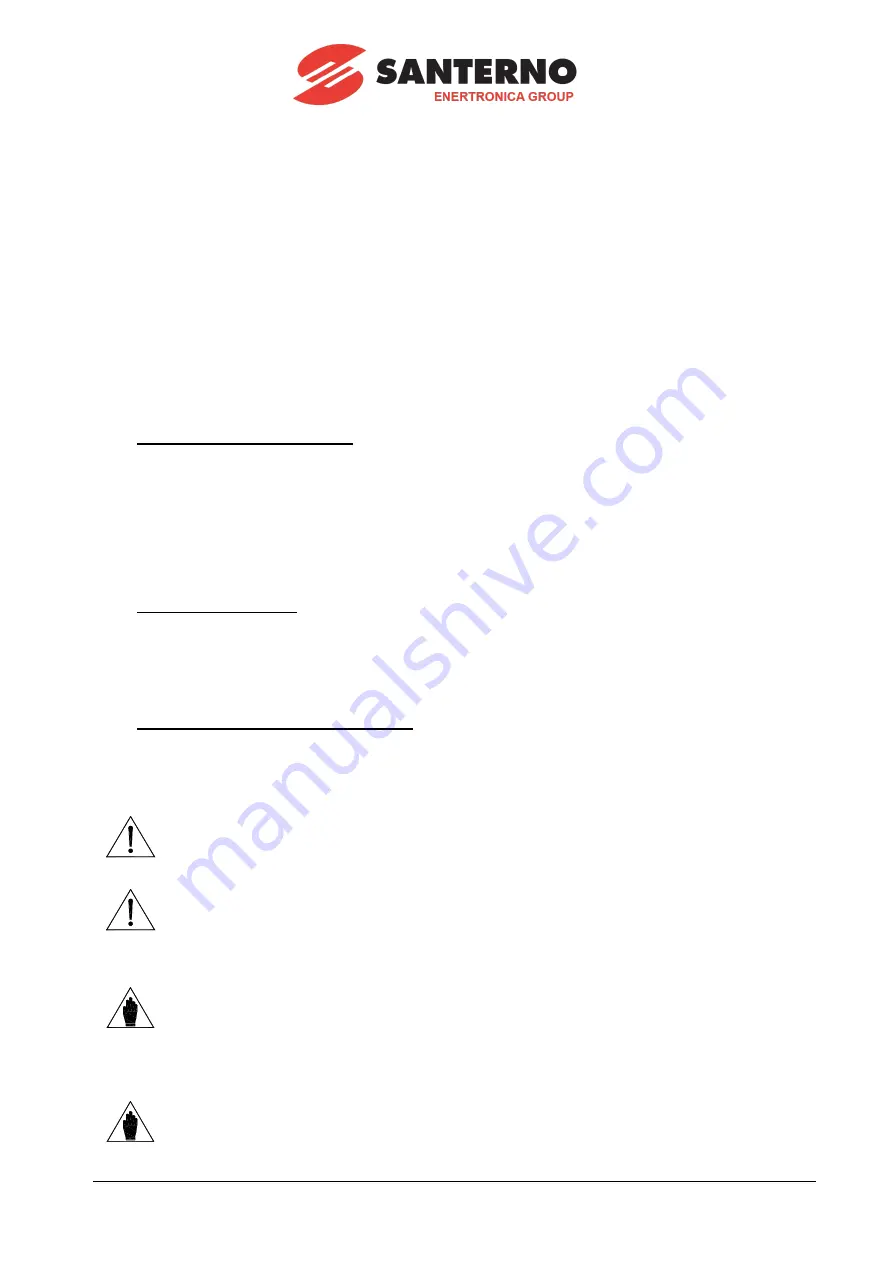
SINUS PENTA
PENTA MARINE
IRIS BLUE
STO FUNCTION
APPLICATION MANUAL
20/
27
5. VALIDATING THE OPERATION OF A SAFETY FUNCTION
Safety Standards EN IEC 62061 and EN ISO 13849 require that the final assembler of the machine
validates the operation of the safety function with an acceptance test.
The acceptance tests must be performed:
At initial start-up (commissioning) of the safety function or installation of a new drive unit in place of an
existing one,
At each periodic annual test of the safety function,
After any changes (wiring, components, settings, etc.) related to the safety function,
After any changes related to the CPU CONTROL BOARD ES927 of the drive,
After any maintenance activity related to the safety function,
After any Test Result FAIL during the STO acceptance test procedure and subsequent decommissioning
of ES927 damaged board and replacement with a new one.
5.1. Acceptance Test Reports
Signed acceptance test reports must be stored into the Instruction’s Manual of the machine. The report
shall include documentation of start-up activities and test results, references to failure reports and
resolution of failures. Any new acceptance tests performed due to periodic annual test (once a year),
changes, maintenance and decommissioning
shall be logged into the Instruction’s Manual of the machine.
Section 5.3 Performing the Acceptance Test includes the template of the Check List for
‘STO Acceptance
Test
’, as a guide for a test report.
5.2. Authorized Person
The acceptance test of the safety function must be carried out by an authorized person having adequate
expertise and knowledge of the safety function. The test must be documented and signed by the
authorized person.
5.3. Performing the Acceptance Test
The drive is working with motor torque applied to motor during the acceptance test.
The following template shall be included in the
Instruction’s Manual of the machine incorporating the motor
drive.
WARNING
Speed and torque applied during the acceptance test need to be compliant
with acceptable working conditions of the application where the drive is
installed.
WARNING
The Safe Torque Off function does not cut off the mains voltage and auxiliary
circuits from the drive. Therefore, maintenance work on electrical parts of the
drive or the motor can only be carried out after isolating the drive system from
the mains supply.
NOTE
The Safe Torque Off function can be used for stopping the drive in emergency
stop situations. In the normal operating mode, it is not recommended to stop
the drive by using the Safe Torque Off function. If a running drive is stopped
by using the Safe Torque Off function, the drive will trip and stop by coasting.
If this is not acceptable, e.g. causes danger, the drive and machinery must be
stopped using the appropriate stopping mode before using this function.
NOTE
Note concerning permanent magnet motor drives in case of multiple
IGBT power semiconductor failure:
Due to the possible DC output voltage present for certain multiple IGBT
failures, in spite of the activation of the Safe Torque Off function, the drive
system can produce an alignment torque which maximally rotates the motor
shaft by 180/p degrees (p is the pole pair number).