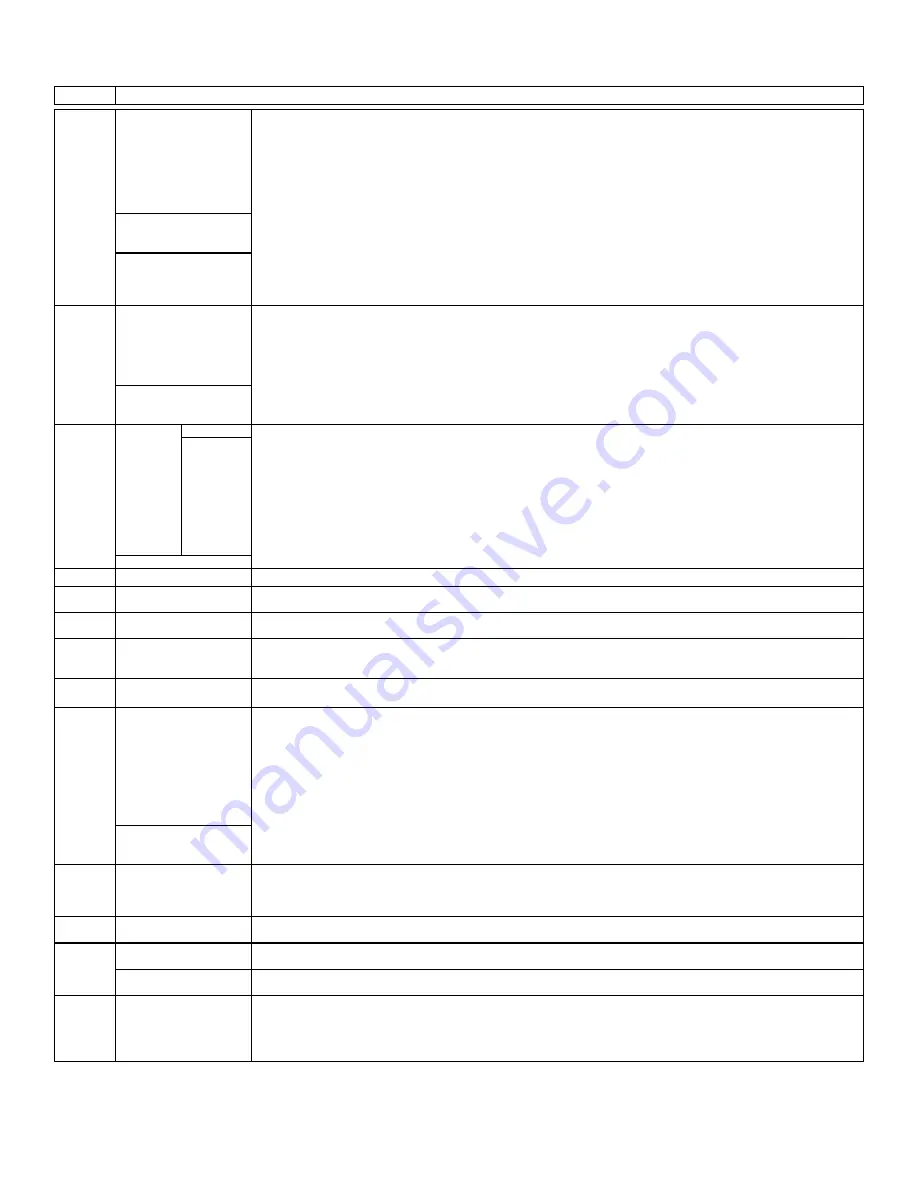
List of Possible Error Causes
Code
Possible error causes
Water tap is closed or faulty
No water pressure, pressure too low or changing
Screen in front of inlet valve clogged
Flow governor at inlet valve faulty
Inlet valve faulty
Inlet valve deenergized (faulty wiring or no activation by electronics)
Inlet hose bent
Softener system clogged (by filling detergent into salt compartment, for instance)
Upright installation without upright assembly kit
Connection height of the discharge hose is lower than 30cm above appliance base
Connection w/o siphon or air chamber
Pressure controller faulty
Pressure controller hose obstructed, bent or leaking
Pressure controller wiring is faulty
Screens in the appliance clogged (also check spray arm nozzles for clogging)
Fault with discharge pump
Discharge pump deenergized (faulty wiring or no activation by electronics)
Obstruction/blocking (filters in the appliance, discharge opening in discharge trough, discharge pump, discharge hose, siphon, cover plug at
siphon connection not removed during first commissioning)
Discharge hose bent or connection height above 100cm
Ball valve in discharge trough glued / blocked (discharge pump does not aerate)
Pressure controller faulty
Pressure controller hose obstructed or bent
Insulation fault with heating element
Leakage
Leakage at recipient, discharge trough, hose system (e.g., Y-type hose), regeneration dosage etc.
Inlet valve faulty (does not close)
Water inlet too high (faulty flow governor at inlet valve)
Connecting hose regenerating dosing to discharge trough blocked
Water inlet channels in regeneration dosing unit blocked
Screens in the appliance clogged (also check spray arm nozzles for clogging)
Pressure controller faulty
Pressure controller hose obstructed, bent or leaking
Pressure controller wiring is faulty
Foam production in the appliance (splashed rinsing liquid / leaking dosing unit or con-compatible detergent / rinsing agent used)
Base trough is dry
Inlet valve or wiring electrically interrupted
i50
Motor triac short-circuit
Faulty electronics
Heating element faulty
Heating element deenergized (faulty wiring or no activation by electronics)
Thermal sensor defect
Wiring faulty (e.g. short-circuit or interruption)
Mains filter defect
Faulty electronics
EMC problem
i90
Check sum error model
programmation
Faulty electronics
Blocking by dishes or cutlery basket
Nozzles clogged (drive nozzles at spray arm extremities)
Spray arm leaking (welding seam)
Spray arm bearing blocked (dirt, foreign bodies)
Screens in the appliance clogged
Bellows at connecting pipe not sealed at recipient rear wall (bellows not contacting/glued together)
Circulating pump does not reach full power (nominal speed is not reached due to winding influence)
Too little water in appliance - for possible causes see Error codes i10 and iF0
Foam production in the appliance (splashed rinsing liquid / leaking dosing unit or con-compatible detergent / rinsing agent used)
No magnet in spray arm
Spray arm detection sensor faulty
Wiring faulty
turbidity sensor defect
Wiring faulty
turbidity sensor dirty
Foam production in the appliance (splashed rinsing liquid / leaking dosing unit or con-compatible detergent / rinsing agent used)
Faulty electronics
Wiring faulty
Circulating pump / capacitor defect
Circulating pump deenergized (faulty wiring or no activation by electronics)
Tachometer generator defect
Wiring faulty
Problem with water inlet in general - see Error code i10, pipette effect in particular (also look for an error memory entry i10)
Problem by incomplete pumping in previous program cycle (remaining water) - see Error code i20 (also look for an error memory entry i20)
Improper loading, e.g. big item (pot, bowl is reversed and fills with water)
Foam production in the appliance (splashed rinsing liquid / leaking dosing unit or con-compatible detergent / rinsing agent used)
ic0
id0
iF0
communication faulty
Circulation pump no function
No tacho signal
recognized
Time limit during filling
exceeded
iA0
Upper spray arm does not
rotate
No spray arm detection
turbidity signal faulty
ib0
i60
i70
i80
No rise in temperature
NTC signal faulty
Check sum error EEPROM
Water is not pumped off
Water level inside appliance is
not detected
i20
Overflow
Water remains
in base trough
i30
i10
No or not enough water let in
Machine runs dry (Siphon
effect)
Water level inside appliance is
not detected