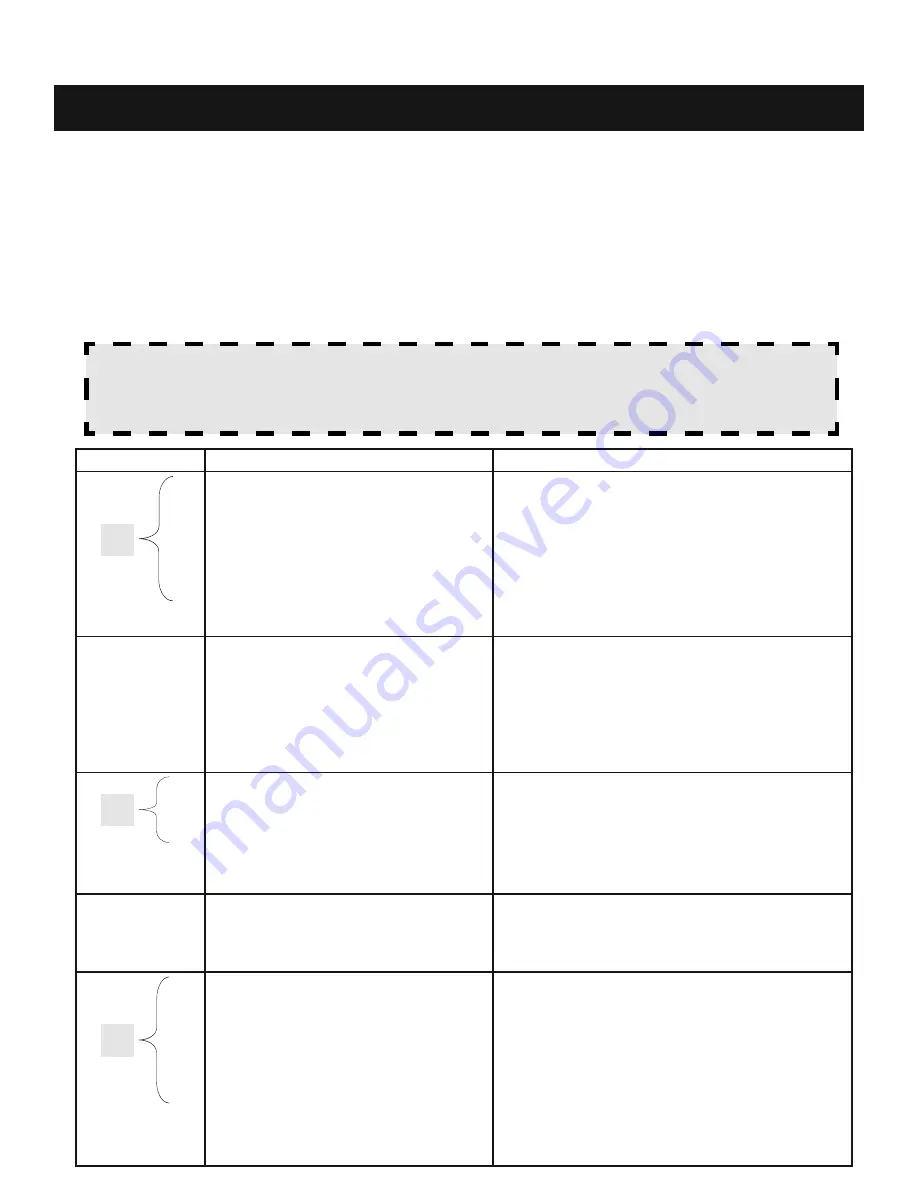
Page 9
P/N 316439221
RANGE TECHNICAL DATA
EOC Failure / Fault Codes
For each Fault code there is a listing of the likely failure condition or cause, as well as suggested
corrective actions to be taken. Not all fault codes will appear in every model but the fault codes are
universal and have the same meaning regardless of the model that is being serviced
Note: Fault codes are not a foolproof system. Never assume that a part has failed based on a displayed
fault code. An example would be if the EOC is displaying F30 (open sensor), the failure could be caused
by a loose connection or faulty wire harness between the EOC and sensor or the sensor could simply
be unplugged.
On freestanding gas and electric ranges manufactured beginning with the serial number date code
VF426
many of the EOC’s will have expanded three digit fault codes. These codes may also appear
in new replacement EOC’s for ranges built prior to this date. Below is a list of possible fault codes
that might appear in the EOC display window. The original two digit fault codes appear in the shaded
boxes followed by the replacement three digit codes.
FAULT CODE
LIKELY FAILURE CONDITION/CAUSE
SUGGESTED CORRECTIVE ACTION
F10
F11
F12
F13
F14
Runaway Temperature.
Shorted Keypad.
Bad Micro Identi
fi
cation.
Bad EEPROM Identi
fi
cation/Checksum error.
Display tail missing/not connected
1. (F10 only) Check RTD Sensor Probe & replace if necessary.
If oven is overheating, disconnect power. If oven continues to
overheat when the power is reapplied, replace EOC. Severe
overheating may require the entire oven to be replaced should
damage be extensive.
2. (F11, 12 & 13) Disconnect power, wait 30 seconds and reapply
power. If fault returns upon power-up, replace EOC.
3. (F14 only) Re-seat the P12 ribbon connector tail. If fault re-
turns replace EOC (
fi
rst action); Touch Panel (second action)
F20
F26
Communication failure between EOC and ESEC
system.
Communication failure with mini oven control.
1. Test harness/connections P4 (EOC) & P11 (Surface element
control board).
2. If harness checks O.K. failure can be caused by faulty UIB,
surface element control board, or EOC.
Check harness and connectors from the EOC to mini oven
control board. Check for 15vdc to mini oven control (red & gray
wires). If harness and voltage are good replace mini oven con-
trol. If fault returns replace EOC.
F30
F31
Open probe connection.
Shorted Probe connection
1. (F30 or F31) Check resistance at room temperature & com-
pare to RTD Sensor resistance chart. If resistance does not
match the RTD chart replace RTD Sensor Probe. Check Sensor
wiring harness between EOC & Sensor Probe connector.
2. (F30 or F31) Check resistance at room temperature, if less
than 500 ohms, replace RTD Sensor Probe. Check for shorted
Sensor Probe harness between EOC & Probe connector.
F40
F41
Cooktop Lockout error.
1. (F40 or F41) Check the wiring.
2. (F40 or F41) Replace the Cooktop Lockout Control Board.
3. (F40 or F41) Replace EOC.
F90
F91
F92
F93
F94
Maximum oven door unlock time exceeded.
Maximum oven door unlock attempts exceeded.
Maximum oven door open time exceeded.
Maximum oven door lock time exceeded.
Maximum oven door lock attempts exceeded.
1. (F90, 91, 92, 93 & 94) Check the wiring between EOC & Lock
Motor Micro Switch.
2. (F90, 91, 92, 93 & 94) Replace the Motor Door Latch assem-
bly if necessary.
3. (F90, 91, 92, 93 & 94) Check for binding of the Latch Cam,
Lock Motor Rod & Lock Motor Cam.
4. (F90, 91, 92, 93 & 94) Check to see if Lock Motor Coil is open.
If open, replace Lock Motor Assembly.
5. (F90, 91, 92, 93 & 94) Lock Motor continuously runs - if Micro
Switch is open, replace Lock Motor Assembly.
6. (F92, 93 & 94) Check oven door Light Switch - if open, replace
Switch.
7. If all situations above do not solve problem, replace EOC.
F1
F9
F3
Содержание 30" GAS FREESTANDING RANGES
Страница 19: ...Page 19 P N 316439221 GAS RANGE COOKTOP STYLES ...
Страница 20: ...Page 20 P N 316439221 GAS RANGE COOKTOP STYLES ...
Страница 43: ...Page 43 P N 316439221 NOTES ...