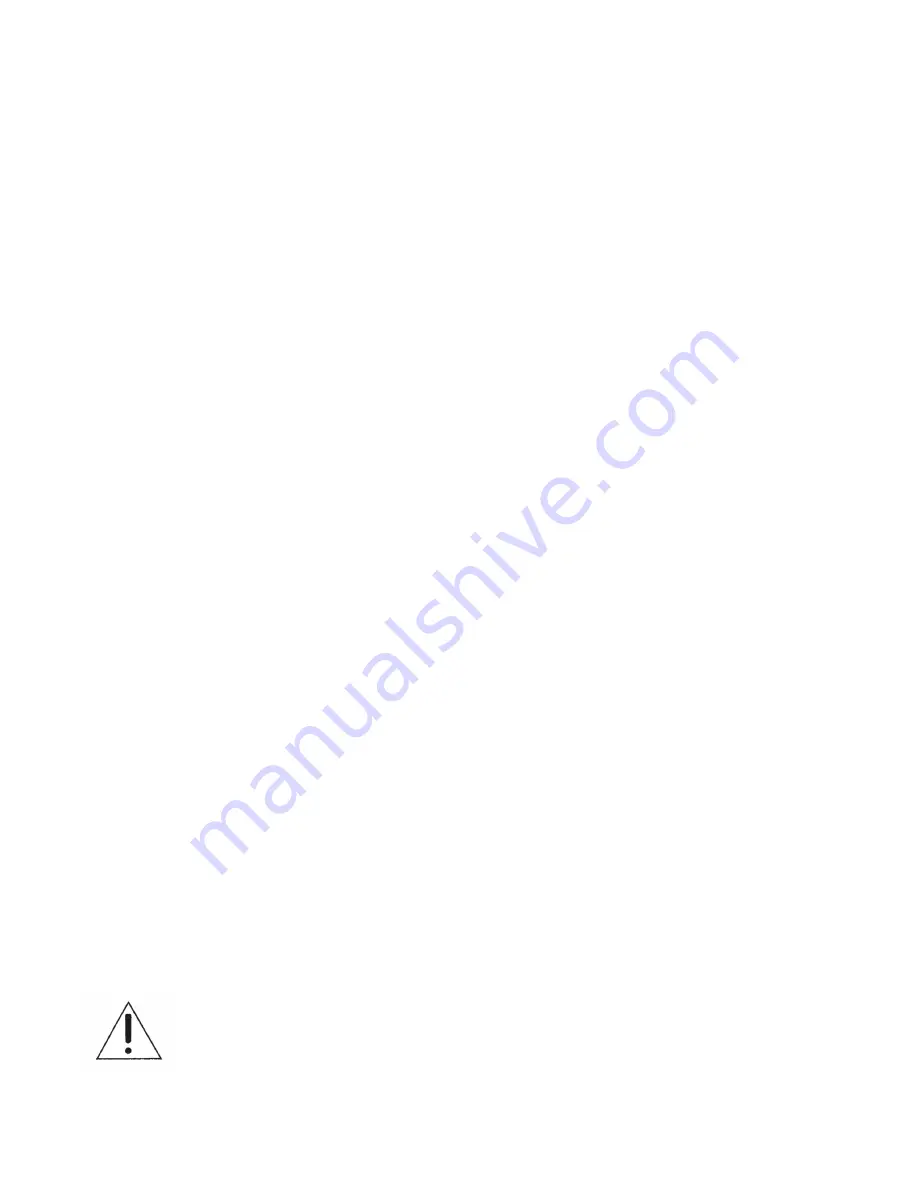
ELECTRO-VOICE
®
Xi-A Rigging Manual
12
strength. This requires the user to calculate the safety factor directly for a given load. The actual
safety factor for a given load is defined as the ratio of the ultimate-break-strength rating of a
mechanical component to the actual load applied to that component. Electro-Voice suggests that
the user maintain an overall safety factor of at least 8:1 when implementing an Xi-A flying system.
In other words, the ultimate break-strength of each of the mechanical components in the system
should be at least eight times greater than the actual force applied to those components. This
includes the Xi-A enclosures, the rigging-strap assemblies, the grid the hoist and all other me-
chanical components and hardware. The working-load limits discussed throughout this manual for
the strength of the Electro-Voice Xi-A enclosures rigging hardware, and the GS-1B, LS-1B, LS-2B,
LS-3B, RS-1B and RS-2B rigging accessories are based on an 8:1 minimum safety factor. Where
local regulations require safety factors greater than 8:1, Electro-Voice insists that the user must
meet the required safety factor. Where local regulations permit safety factors less than 8:1,
Electro-Voice still insists that the working-load limit of the Xi-A enclosures/rigging hardware, and
the GS-1B, LS-1B, LS-2B, LS-3B, RS-1B and RS-2B rigging accessories never be exceeded.
4.2 Special Safety Considerations for Xi-A Loudspeaker Arrays
The techniques discussed in Chapter II for constructing arrays may be expanded upon to create
different arrays utilizing different combinations of Xi-A loudspeaker systems, as long as a sufficient
safety factor is maintained. The user is reminded that the top cabinet in an array supports the
weight of all the cabinets hung beneath it, and that the weight distribution between the rigging
points will depend on the exact configuration. For example, the center of gravity of the Xi-1152A
loudspeaker system is not perfectly centered but rather shifted slightly towards the high-frequency
side of the box. As a result, when an Xi-1152A is hung sideways (i.e., with the cabinet oriented so
the rigging track is on the sides), the load on the rigging strap on the high-frequency side of the Xi-
1152A system would be slightly higher than the load on the horn/compression-driver side. On the
other hand, the load would be distributed equally between the two rigging straps at the top of a
column of Xi-1152A systems hung with the enclosures oriented with the rigging track on the top
and bottom. The weight distribution of any Xi-A array can be calculated with the information
presented in Figure 2.2. Readers unfamiliar with the process of calculating load distributions
should consult the list of references in Appendix B.2 that cover the topics of rigging and
engineering mechanics. When arrays are constructed with columns of Xi-A systems oriented with
the rigging tracks on the top and bottom of the enclosures the rigging straps between the
enclosures will not hang straight down with a 0° vertical angle if the center-to-center spacing of the
rigging attachment positions are different from the bottom of one cabinet to the top of the cabinet
immediately beneath it. The rigging straps will deviate from a 0° vertical angle when trapezoidal
cabinets are employed, or cabinets of differing size are mixed in the same column. These vertical-
angle differences will result in forces (i.e., tension loads) of the top cabinets (including the top
rigging straps). However, if the rigging straps throughout the array are at unusual and or extreme
angles, the worst-case forces in an array may occur somewhere other than the top rigging-
attachment point of the top cabinets.
Attention: Array details and rigging configurations will affect the load on the
loudspeaker systems, the rigging straps and all associated rigging hardware. The
user is responsible for determining the loads on all of the mechanical components
throughout the loudspeaker array, and for ensuring that the working-load limits and
resulting safety factors are not exceeded. A qualified structural engineer should be
consulted to evaluate the design.