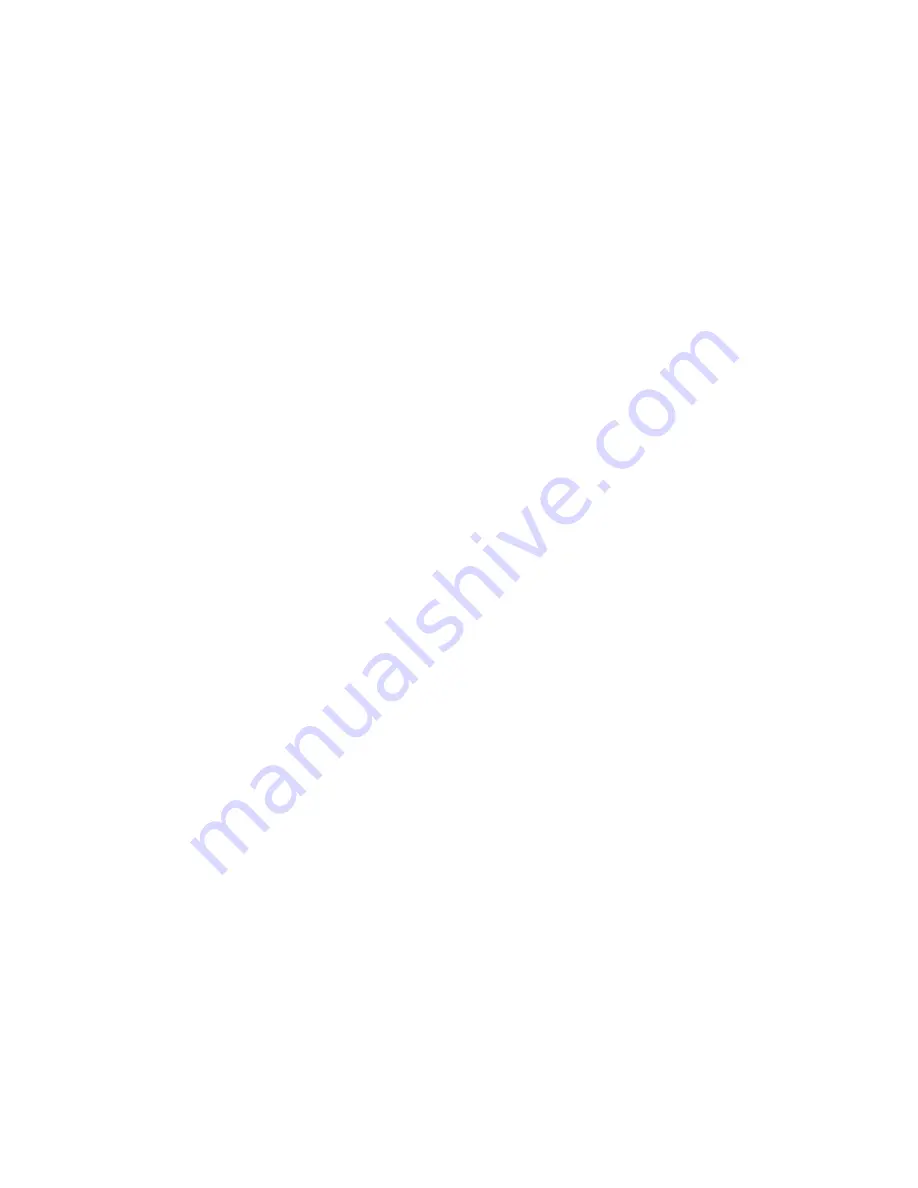
23
1300 and 1500 welding machine models belong to a new generation of welding inverters. This generation has been
developed as integrated and portable units using the newest techniques in power electronics, based on an inverter process
with IGBT, which enables the following:
- A considerable reduction of weight and volume,
- The dynamic control of the welding current,
- The specific protection of power components,
- A high power in a small space at very low power consumption.
4. INSTALATION
4.1 CONNECTION TO THE MAIN SUPPLY
This unit must be connected to a single phase 230V - 50 Hz/60 Hz + ground with a tolerance of +/-10%.
Main supply must be protected by fuses or circuit-breaker according to the value I1eff written on the specifications
of the power source.
It is strongly suggested to use a differential protection for the operator’s safety.
4.2 CONNECTION TO EARTH
For the operator's protection, the power source must be correctly grounded (according to the International
Protections Norms).
It is absolutely necessary to set a good earth connection with the green/yellow wire of the power cable. This will
avoid discharges caused by accidental contacts with grounded pieces. If no earth connection has been set, a high risk of
electric shock through the chassis of the unit remains possible.
4.3 WELDING
Connect the power source to the main supply and the ground.
Connect the ground cable and the electrode holder to the appropriate power conne (5) and - (4) according
to the electrode polarity being used (refer to the electrodes manufacturer’s datasheets).
Start up the power source with the switch ON/OFF (7).
The red indicator (2) illuminates and indicates that the machine is undervoltage.
Adjust welding current with potentiometer (1).
Place the electrode on the piece you have to weld in order to strike the arc.