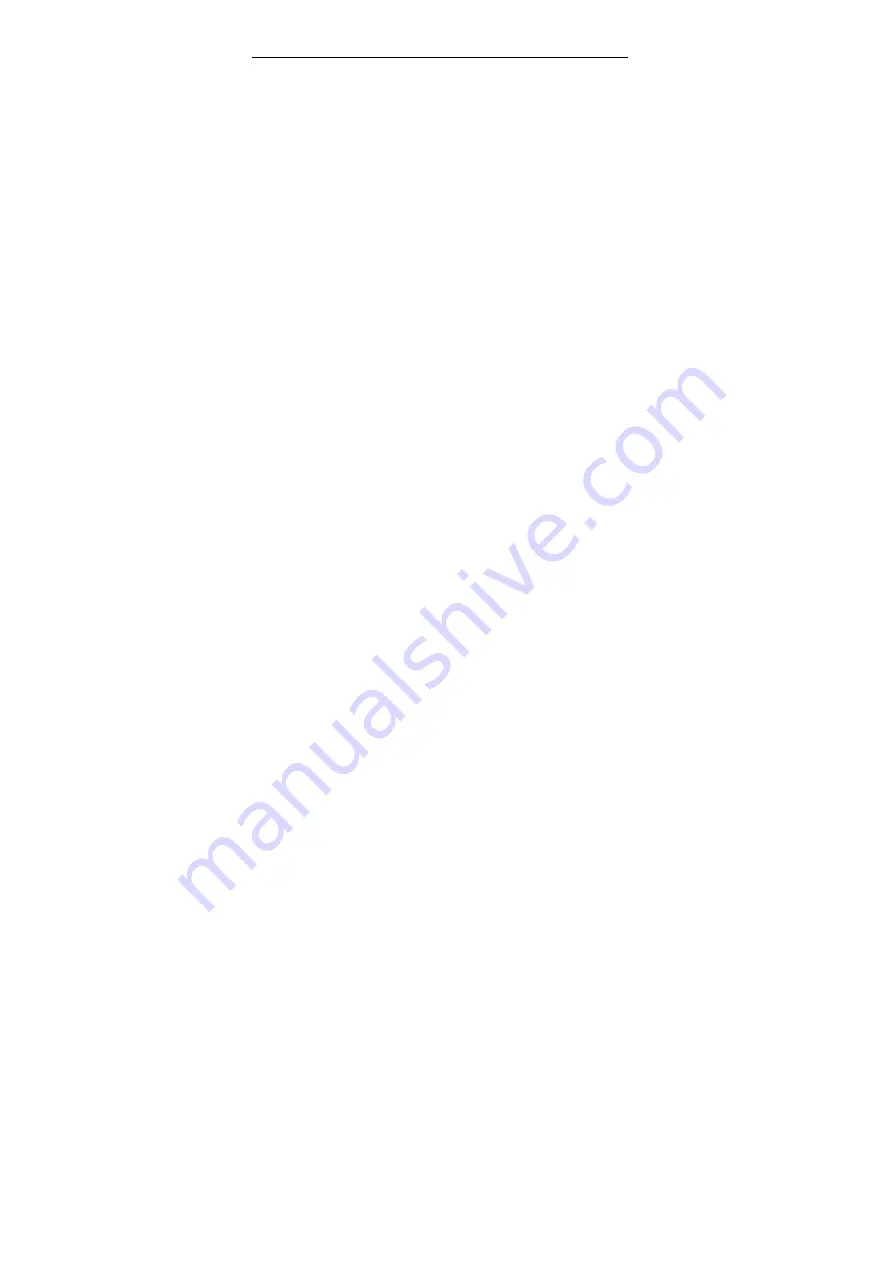
Trinox Floor Standing Shell and Tube Boiler
20 L344
©
Elco UK 04/07/2012
-
check the hermetic seal of the smoke circuit (inspection doors, burner plate, smoke box,
boiler/flue connection);
-
check that the rubber holder on the flame warning light is connected to the burner air inlet or
clogged.
FAULT: the boiler does not reach set pressure.
REMEDY:
-
check that the smoke side and water side of the boiler are clean;
-
check the combination, regulation and performance of the burner;
-
check the regulation of the pressure switches and that they work correctly;
-
check the position of the thermostat gauges;
-
ensure that the boiler capacity is appropriate for the plant
FAULT: the boiler reaches the appropriate temperature but the heating system
is cold.
REMEDY:
-
check that no air is in the system;
-
check that circulation pumps are working well;
FAULT: the safety pressure switch intervenes.
REMEDY:
-
check electric wires
-
check the position of the thermostat probes;
-
check the thermostat setting and ensure they work well
FAULT: the safety valve of the boiler intervenes often.
REMEDY:
-
check the system loading pressure;
-
check the efficiency of the expansion vessel;
-
check the calibration of the safety valves.
FAULT: membranes overheating due to lack of water in the boiler.
Содержание Trinox 1000
Страница 7: ...Trinox Floor Standing Shell and Tube Boiler 7 L344 Elco UK 04 07 2012 TECHNICAL SPECIFICATION ...
Страница 11: ...Trinox Floor Standing Shell and Tube Boiler 11 L344 Elco UK 04 07 2012 Wiring Diagram for BMS relays ...
Страница 12: ...Trinox Floor Standing Shell and Tube Boiler 12 L344 Elco UK 04 07 2012 ...