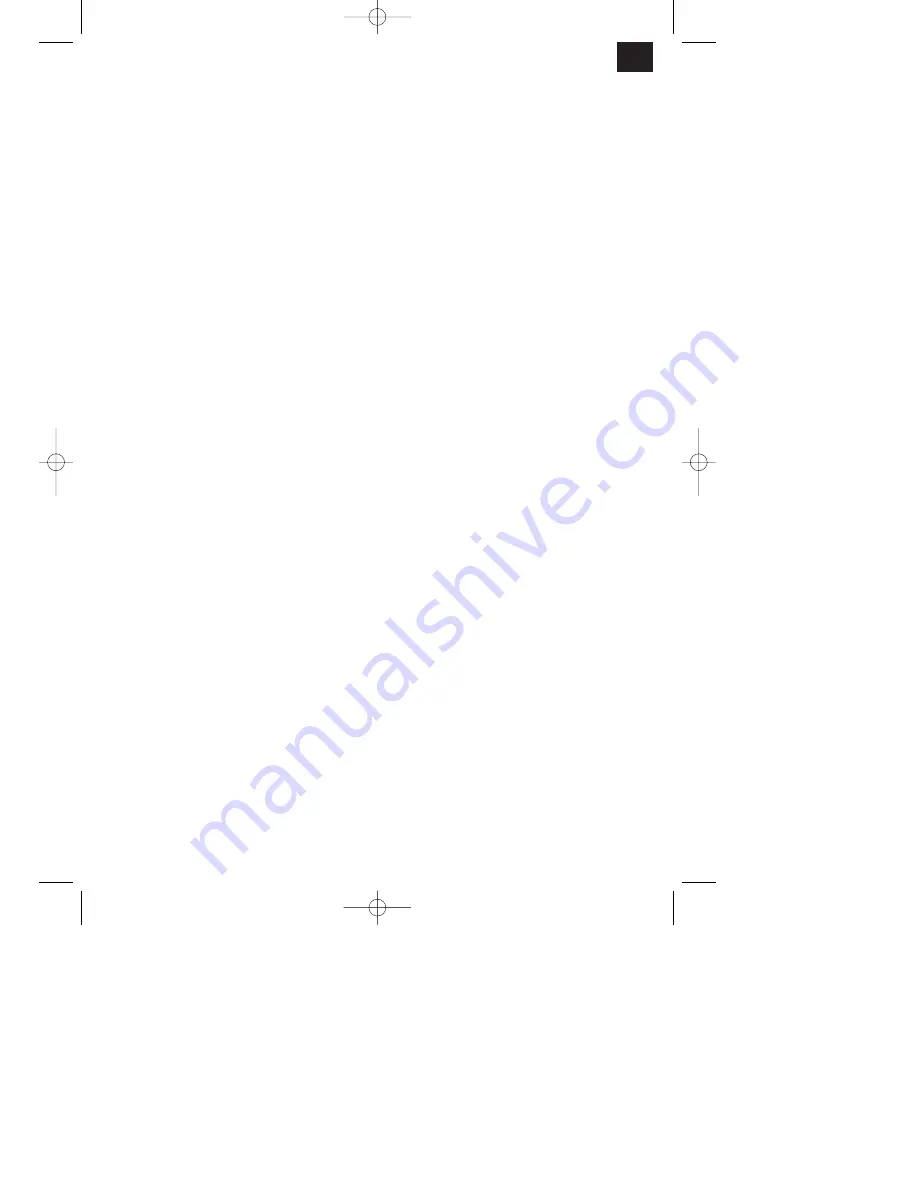
6.2 Intake process
앬
During the priming process, the shut-off devices
present in the pressure pipe (spray nozzles,
valves etc.) must be completely open so that the
air in the suction pipe can escape freely.
앬
Depending on the suction height and the air
quantity in the suction pipe, the initial priming
process can last for approx. 0.5 min. – 5 min. In
the case of longer priming periods, top up again
with water.
앬
If the pump is removed after use, it is essential
that it is filled with water again the next time it is
connected and started.
6.3 Stopping the engine
앬
Set the On/Off switch to “OFF”.
앬
Close the petrol cock.
Running-in period:
For the first 20 hours of operation, the motor
must not be operated at full throttle for too long.
Misfires, start-up difficulties:
Check whether
앬
fuel is flowing into the carburetor;
앬
the fuel filter is clean;
앬
the carburetor air valve is open;
앬
the air filter is clean;
앬
the spark plug is clean and the electrode gap is
between 0.6 and 0.7mm.
7. Cleaning, maintenance, storage and
ordering of spare parts
Disconnect the spark plug boot before doing any
cleaning and maintenance work!
7.1 Cleaning
Keep all safety devices, air vents and the motor
housing free of dirt and dust as far as possible.
Wipe the equipment with a clean cloth or blow it
with compressed air at low pressure.
We recommend that you clean the device
immediately each time you have finished using it.
Clean the equipment regularly with a moist cloth
and some soft soap. Do not use cleaning agents
or solvents; these could attack the plastic parts
of the equipment. Ensure that no water can seep
into the device.
7.2 Maintenance
In this connection, please also read the attached
service information
7.2.1 Changing the oil
The engine oil is best changed when the engine is at
working temperature
앬
Use only engine oil (10W40).
앬
Place the machine on a slightly inclined surface
so that the oil drain plug is at the lower end
(Figure 5a / Item A).
앬
Remove the oil filler screw (Figure 5a / Item B).
앬
Remove the oil drain plug and drain the warm
engine oil into a suitable container.
앬
After all the oil has drained, screw in the oil drain
plug and place the machine on a flat surface.
앬
Insert fresh engine oil up to the top mark on the
oil dipstick (Figure 5b / Item H).
Important.
Only inset the oil dipstick to check
the oil level. Do not screw it in.
While the machine is working, the oil level must be
between the two marks “L” and “H” (Figure 5b).
Dispose of the waste oil properly.
7.2.2
Air filter
Clean the air filter at regular intervals, and replace it if
necessary.
앬
Remove the screw from the air filter cover (Figure
6a)
앬
Remove the air filter cover.
앬
Remove the screw from the air filter element
(Figure 6b)
앬
Remove the air filter element (Figure 6c).
앬
Clean the air filter by tapping it, blowing it out
with compressed air or by washing it with soap
suds.
Important.
Leave the air filter to dry before
you refit it.
앬
Assemble in reverse order.
7.2.3 Spark plug
Clean the spark plug at regular intervals, and replace
it if necessary. Set the electrode gap to 0.6 mm.
앬
Remove the spark plug boot by twisting it (Figure
7)
앬
Remove the spark plug using a spark plug
wrench
앬
Clean the spark plug with a copper wire brush or
fit a new one.
앬
Assemble in reverse order.
9
GB
Anleitung_BG_PW_48_SPK1:_ 25.06.2008 9:34 Uhr Seite 15