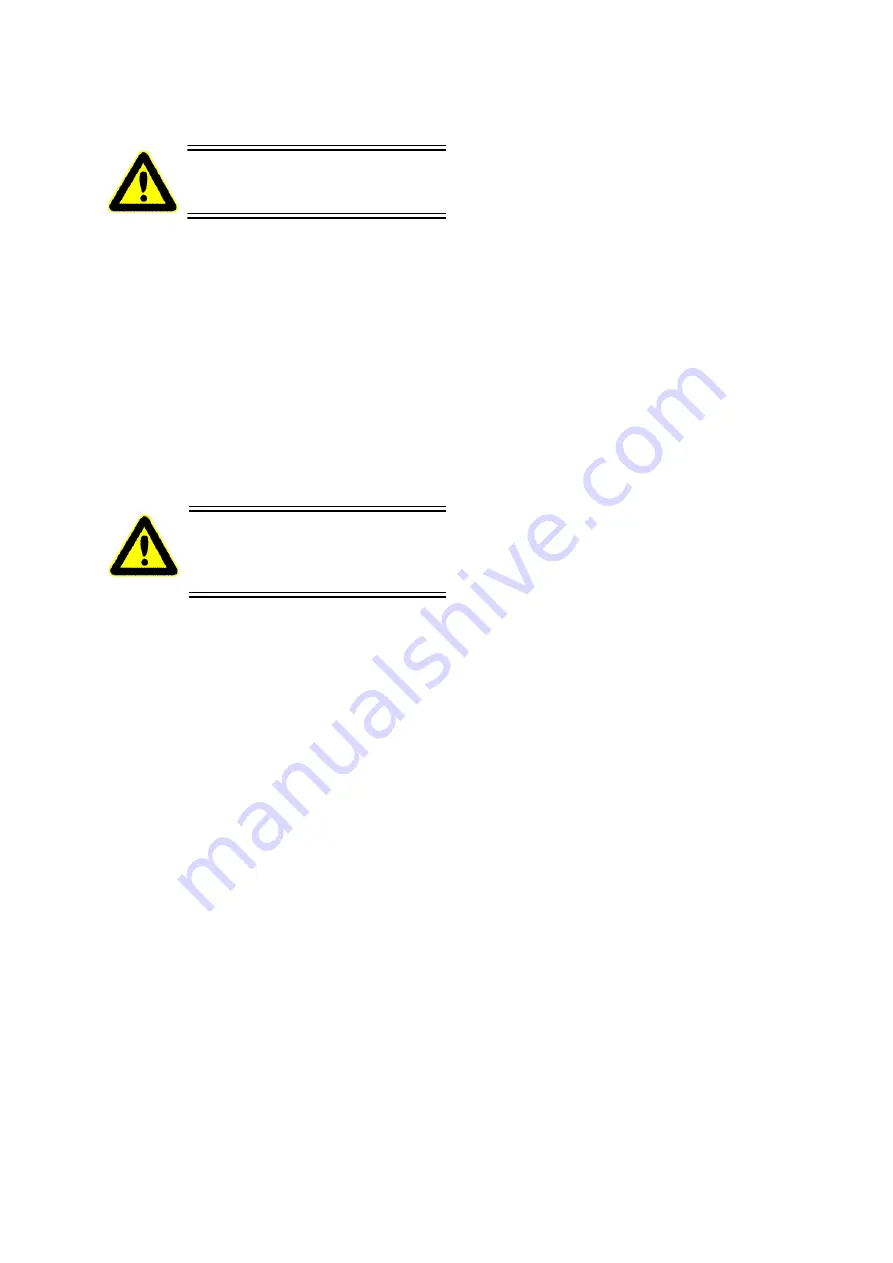
Schmid & Wezel
D-75433 Maulbronn
Seite / Page
Ausführung / Execution
05.2004
6. Cleaning and Maintenance
Disconnect the machine from the
works mains before all cleaning
and maintenance work!
6.1 Daily Cleaning After Completing
Work
Trouble-free, continuous operation can be ensured
only if the hook cutter is permanently kept in a
clean, hygienic condition. The machine should nor-
mally be disinfected before each cleaning.
Observe the applicable safety and hygiene regula-
tions (EN 1672)!
Disinfectants must not be allowed to come into di-
rect or indirect contact with foodstuffs. Rinse the
machine with clear water after disinfection.
Do not use aggressive solvents! Do
not use steam or high-pressure
cleaners! Do not immerse the unit
in water!
6.1.1 Disinfection
Disinfect the machine during operation after every
cut with hot water (82° C).
6.1.2 Cleaning the cutter
Clean the machine after use with a cloth, brush and
warm water (40 - 55° C). Stubborn or encrusted dirt
and residue must be soaked beforehand. Clean us-
ing a cleaning agent, preferably as a foam, that is
applied to the surface to be cleaned and allowed to
work in for 15 - 20 minutes. Subsequently wash off
the dissolved soiling manually with warm water.
Recommended cleaning agents
Diversey Lever Tego 2000: Surface-active disin-
fectant.
Diversey Lever GmbH
Mallaufstr. 50-56, 68219 Mannheim
P3-topax 91: Surface-active disinfectant
Henkel-Ecolab Deutschland GmbH
Postfach 13 04 06, 40554 Düsseldorf
A cleaning plan and further details can be obtained
from the above addresses.
The above cleaning agents are only a recommenda-
tion; if other cleaning agents are used, the customer
should examine the material compatibility and com-
pliance with the hygiene regulations.
6.1.3 Lubricants and hydraulic oil
The lubricant and the hydraulic oil have to meet the
regulations for the foodstuffs sector (DIN 1672).
Recommended lubricating grease
Klübersynth UH1 14-22 (1 kg special grease in can)
Quality: H1 approval
Order No.001 365 621
Recommended hydraulic oil
Shell Risella D15 (ISO VG 10 - ISO VG 68 to DIN
51519)
Quality: H1 approval
Order No.001 365 614
6.2 Daily Maintenance of Cutter
6.2.1 Lubrication
After every cleaning, grease the pivot and sliding
points and the blades lightly with EFA Special
Grease.
6.2.2 Blade clearance
Check the blade clearance at regular intervals. In or-
der to avoid breakage, the blades must always be
adjusted without clearance but with free movement.
If the self-locking effect of the hex. nut is no longer
assured, it must be replaced without delay. See also
Chapter 4.1 "Changing Blades" (pg. 4).
6.3 Extended Maintenance (after
approx. 100 operating hours)
6.3.1 Hydraulic power unit
Check the oil level at regular intervals and top up, if
necessary. See also Chapter 3.1.2 "Hydraulic power
unit" (pg. 3) and the separate operating manual for
the hydraulic power pack.
CAUTION! Food grade: H1 approval. Pay attention
to cleanliness! Use a filler funnel with a fine-mesh
screen (mesh width approx. 0.4 mm).
At least once a year, drain the oil filling, inspect for
soiling and replace if necessary.
The hydraulic oil is classified as a hazardous sub-
stance and must be used and disposed of according-
ly. On no account may hydraulic oil drain into the
sewage system or escape into the atmosphere.