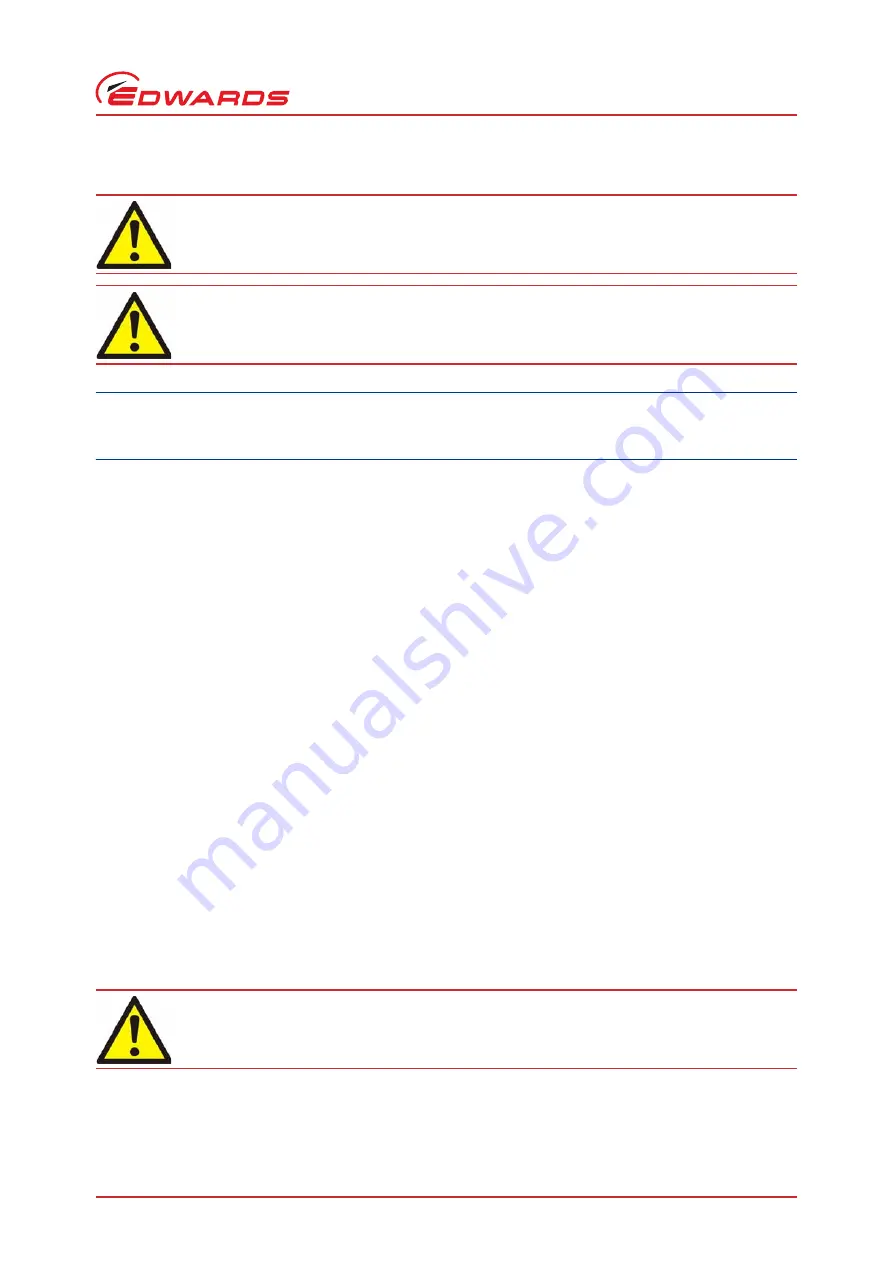
© Edwards Limited 2009. All rights reserved.
Page 27
Edwards and the Edwards logo are trademarks of Edwards Limited.
INSTALLATION
A705-74-880 Issue K
3.11.2
Connect the pump-outlet
CAUTION
Install an outlet catchpot to prevent the drainage of condensate back into the pump. If not, condensate that
drains back into the pump may damage it or cause it to seize.
The exhaust pipeline system must be designed so that the pressure in the pipeline during pump operation is less than
1.15 bar absolute (1.15 x 105 Pa). If the pressure in the pipeline is higher than this pressure, the pump will operate
at a high temperature and may trip because of excessive electrical current consumption.
Flexible bellows must be incorporated in the exhaust pipeline to reduce the transmission of vibration and to prevent
loading of coupling-joints. The bellows must have a maximum pressure rating which is greater than the highest
pressure that can be generated in your system, and which can withstand the maximum temperatures that can be
generated by your process conditions.
Use the following procedure to connect the pump-outlet to your exhaust pipeline:
1. Refer to
. Undo and remove the four M8 x 50 hex-head bolts, nuts and washers that secure the blanking-
plate to the pump-outlet (13) and remove the blanking-plate. Retain the bolts, nuts and washers.
2. Use the trapped O-ring supplied to connect the pump-outlet (13) to your exhaust pipeline; secure with the bolts,
nuts and washers retained in Step 1.
Note:
If required, you can adapt the blanking-plate removed in Step 1 above to fit your exhaust pipeline: drill a
suitable size hole in the centre of the blanking-plate, then weld the blanking-plate to your pipeline.
The exhaust manifold and the Pressure relief valve are fitted with purge ports (
, items 11 and 30) that may
be used to dilute the exhaust gas if required. The ports can also be used for instrumentation if necessary.
3.11.3
External Evacuation of High Vacuum Bearing Oil Box
If desired, the high vacuum oil box can be externally evacuated. This is achieved by utilising connections located
underneath the high vacuum head plate evacuation port cover plate (
, item 29). For advice on this facility
and associated applications please contact Edwards.
3.12
Leak test the installation
When supplied, the leak rate of the pump is tested to be less than 1x10
-3
mbar Is
-1
(1x10
-1
Pa Is
-1
, 2.1x10
-6
). The
required leak rate for your system will depend on your safety and process requirements.
WARNING
Exhaust should be piped to a suitable treatment plant to prevent the discharge of dangerous gases
or vapours to the surrounding atmosphere.
WARNING
Safety devices should be incorporated to prevent operation of the pump when the exhaust pipeline
is restricted or blocked. If not, the exhaust pipeline may become over-pressurised and may burst.
WARNING
Leak-test the system after installation and maintenance and seal any leaks found to prevent the
leakage of dangerous substances out of the system and leakage of air into the system.
Содержание DRYSTAR GV Series
Страница 2: ......