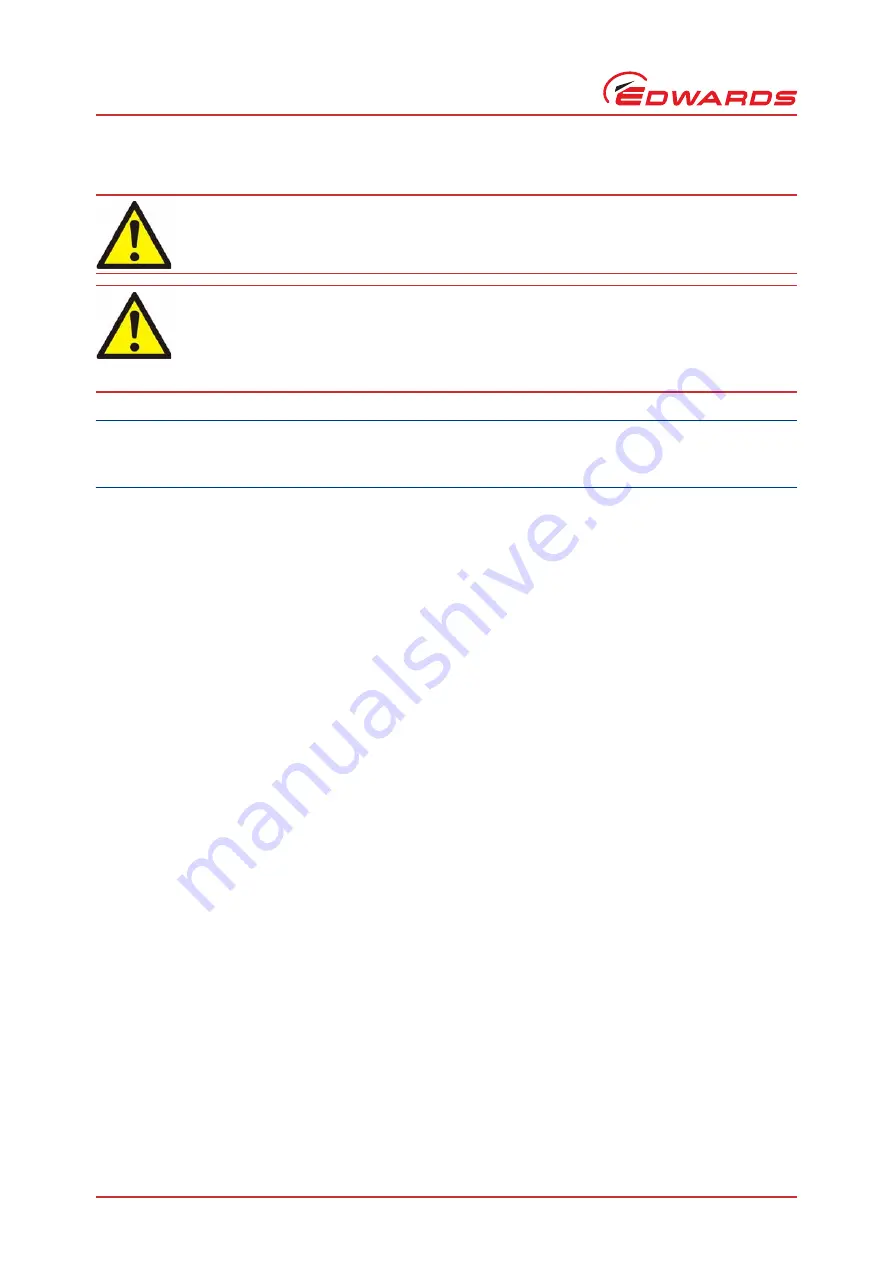
A705-74-880 Issue K
Page 20
© Edwards Limited 2009. All rights reserved.
Edwards and the Edwards logo are trademarks of Edwards Limited.
INSTALLATION
3.6.4
Connect to the thermal snap-switches
CAUTION
Ensure that you route the snap-switch away from hot surfaces of the pump or other equipment. If not, the cable
may be damaged.
Connect the output of the warning thermal snap-switch to your control equipment to provide an indication that the
pump is too hot.
Connect the output of the shutdown thermal snap-switch to the electrical-overload control-loop of your contactor,
so that the contactor will automatically switch off the pump if it is too hot: refer to
.
The thermal snap-switches will reset (that is, close again) when the pump cools down to a preset temperature (see
). We therefore recommend that your control equipment incorporates a manual reset device so that the
pump does not automatically switch on again when it cools down.
Use the following procedure to connect the thermal snap-switches. The output from the thermal snap-switches will
be normally closed and will open when the pump is too hot.
1. Refer to
. Undo and remove the four screws (1) that secure the cover (2) to the thermal snap-switch box
(3), and then remove the cover.
2. Remove the plastic bag from inside the box, this bag contains the crimp connectors and Insulators required to
connect the snap-switches.
3. Pass a suitably rated (see
) four-core cable through the cable gland (5).
4. Fit the crimp connectors to the ends of the four wires in the cable (4), and then fit the insulators around the
connections.
5. Fit the crimp connectors on one pair of wires (11) to the spade terminals (10) of the shutdown thermal snap-
switch (9).
6. Connect the other ends of the same pair of wires to the electrical-overload loop of your contactor.
7. Fit the crimp connectors on the remaining pair of wires (6) to the spade terminals (7) on the warning thermal
snap-switch (8)
8. Connect the other end of the same pairs of wires to the warning circuit of your control equipment.
9. Tighten the cable-gland (5) to secure the cable in position.
10. Refit the cover (2) and secure with the four screws (1).
WARNING
You must connect the shutdown thermal snap-switch so that the pump stops when the thermal
snap-switch opens. If not there may be a risk of fire.
WARNING
Incorporate a manual reset device in your control equipment. If not,and a fault which causes the
shutdown thermal snap-switch to open is not corrected the pump will automatically switch on
again when it cools down. If maintenance or fault finding on the pump has started, there will then
be a risk of injury.
Содержание DRYSTAR GV Series
Страница 2: ......