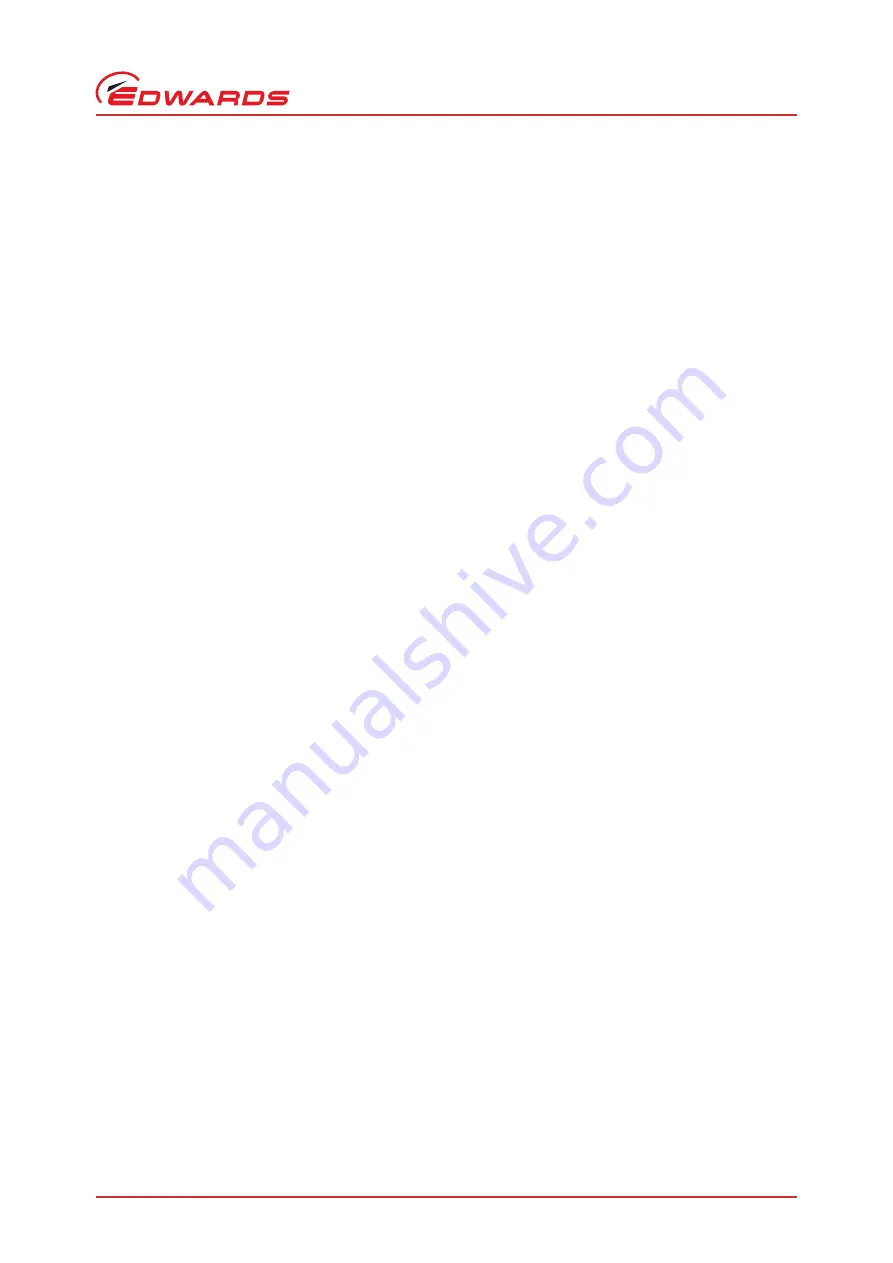
© Edwards Limited 2012. All rights reserved.
Page 21
Edwards and the Edwards logo are trademarks of Edwards Limited.
INSTALLATION
A750-04-880 Issue F
3.5.2
Total recirculation sealing liquid and seals flush supply system
A total recirculation system minimizes waste sealing liquid from the pump. Such a system may be particularly
effective when used in a solvent removal or drying process, where process vapours are condensed inside the pump;
the sealing liquid used can be the same as the condensed process vapours. In this configuration a loss of cooling liquid
to the heat exchanger could cause the service liquid temperature and hence any contact surfaces to exceed the
maximum allowable surface temperature. A temperature probe is therefore always fitted and should be set to trip
the pump at 70°C.
Refer to
, detail A. The sealing liquid discharged at the pump outlet is separated from the pumped gases and
vapours in the sealing liquid reservoir (14), connected to the pump process outlet pipeline (19).
The sealing liquid is then recirculated to the pump through a cooler (13). This removes the heat of compression and
any latent heat of condensation from the recirculated sealing liquid.
On ATEX Category 1 and 2 pumps configured for external seals flush supplies, the sealing liquid reservoir (14) can be
used to provide the seals flush supplies, or an external seals flush supply (1) can be used.
3.5.3
Partial recirculation sealing liquid and seals flush supply system
, detail B. In a partial recirculation system, part of the sealing liquid discharged at the outlet is
recirculated through the pump (8).
The sealing liquid discharged at the pump outlet enters the sealing liquid reservoir (14), connected to the pump
process outlet pipeline (19).
Fresh sealing liquid is supplied to the reservoir (14), through the float operated fill/top-up valve (15).
A mixture of fresh and recovered sealing liquid from the reservoir is then supplied to the sealing ring in the pump
(through the supply pipeline: 12, 11, 10, 9).
On ATEX Category 1 and 2 pumps configured for external seals flush supplies, the sealing liquid reservoir (14) can be
used to provide the seals flush supplies, or an external seals flush supply (1) can be used.
3.5.4
Once-through sealing liquid and seals flush supply system
Note:
Because of the potential environmental impacts, we do not recommend the use of once-through systems.
, detail C. In once-through systems, the sealing liquid is supplied directly to the liquid ring in the
pump (8), through a suitable supply pipeline (17, 16, 12, 26, 11, 10, 9).
The used sealing liquid is discharged with the pumped gases and vapours through the outlet pipeline (21) into your
exhaust-extraction system.
On ATEX Category 1 and 2 pumps configured for external seals flush supplies, the sealing liquid supply (17) can be
used to provide the seals flush supplies, or a separate external seals flush supply (1) can be used.
3.6
Unpack and inspect
1. Remove all packing materials and protective covers and check the pump. If the pump is damaged, notify your
supplier and the carrier in writing within three days; state the Item Number of the pump together with your
order number and your supplier's invoice number. Retain all packing materials for inspection. Do not use the
pump if it is damaged.
2. Look at the pump identification plate (refer to the System Manual) and check that the pump is suitable for use in
your system. If the pump is not suitable for use in your system, do not continue to install the pump: contact your
Supplier or Edwards.
If the pump is not to be used immediately, replace the protective covers. Store the pump in suitable conditions, as
described in