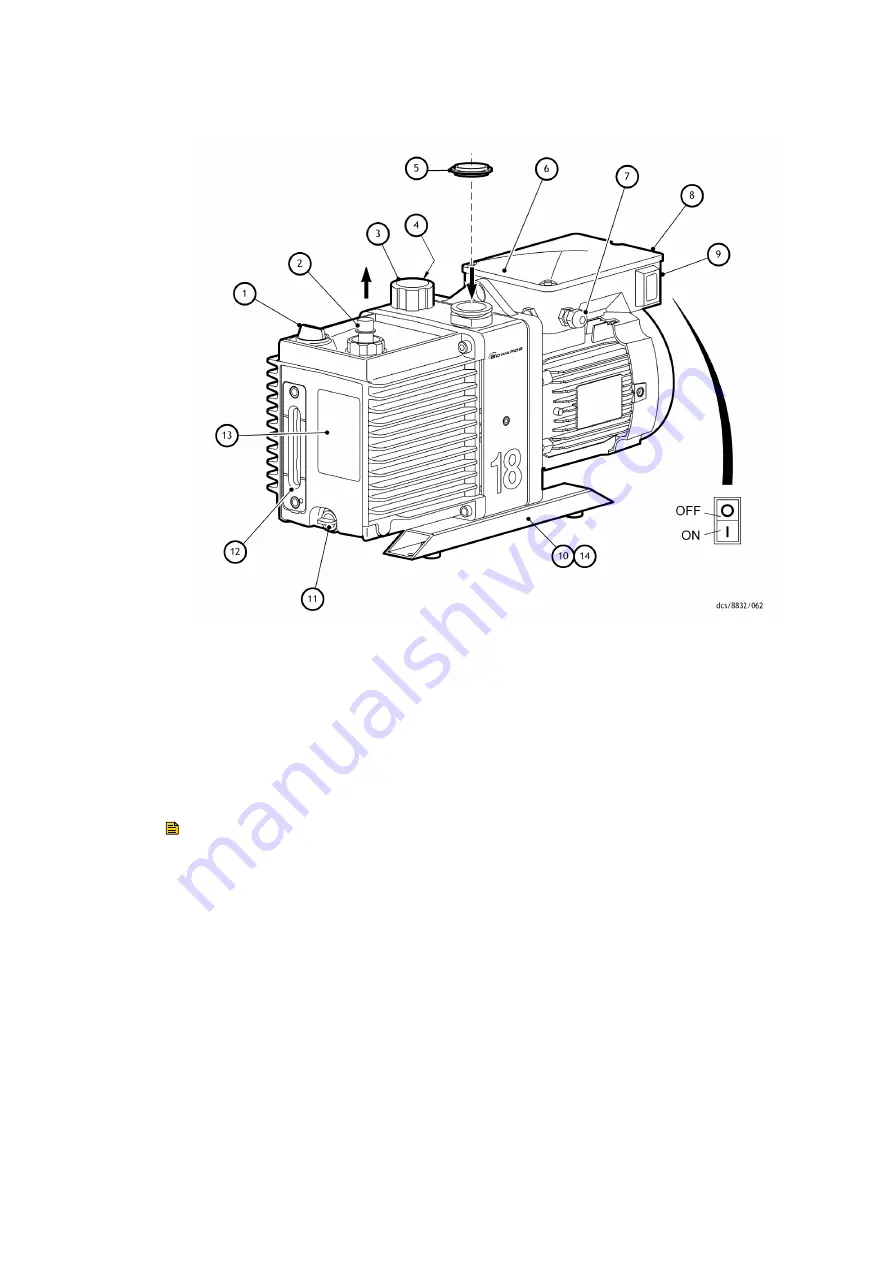
Figure 1 General view of the pump
1. Oil filler
2. Outlet nozzle
3. Gas-ballast control
4. Gas-ballast inlet
5. Centring-ring and O-ring (supplied)
6. Inlet-port (adaptor flange)
7. Cable-gland/Amphenol connector
position
8. Motor terminal box
9. On/Off switch
10. Box section skids
11. Oil drain-plug (gravity drain)
12. Oil sight-glass
13. Pump identification label
14. Oil drip tray
1. Oil filler
2. Outlet nozzle
3. Gas-ballast control
4. Gas-ballast inlet
5. Centring-ring and O-ring (supplied)
6. Inlet-port (adaptor flange)
7. Cable-gland/Amphenol connector
position
8. Motor terminal box
9. On/Off switch
10. Box section skids
11. Oil drain-plug (gravity drain)
12. Oil sight-glass
13. Pump identification label
14. Oil drip tray
Note:
A pump with a single-phase motor is shown in this figure. The motor shown in this figure
is not representative of the motor used on the E1/E2M18 pumps with Item Numbers
A34317984 and A36317984. On these pumps, Cable-gland/Amphenol connector position
and On/Off switch are transposed, with Cable-gland/Amphenol connector position being
an IEC60320 16-20 Amp socket.
2.4 Gas-ballast
When using the pump with high vapour throughputs, the gas-ballast facility should be
used to prevent condensation of the vapours inside the pump. The condensates will
contaminate the oil, will cause performance to deteriorate and may cause corrosion of
the pump mechanism.
Air (or an inert gas) can be introduced into the pump mechanism through the gas-ballast
control (
Figure: General view of the pump on page 11
Page 11
A34310880_T - Introduction
Содержание A34310940
Страница 6: ...This page has been intentionally left blank...
Страница 56: ...edwardsvacuum com...