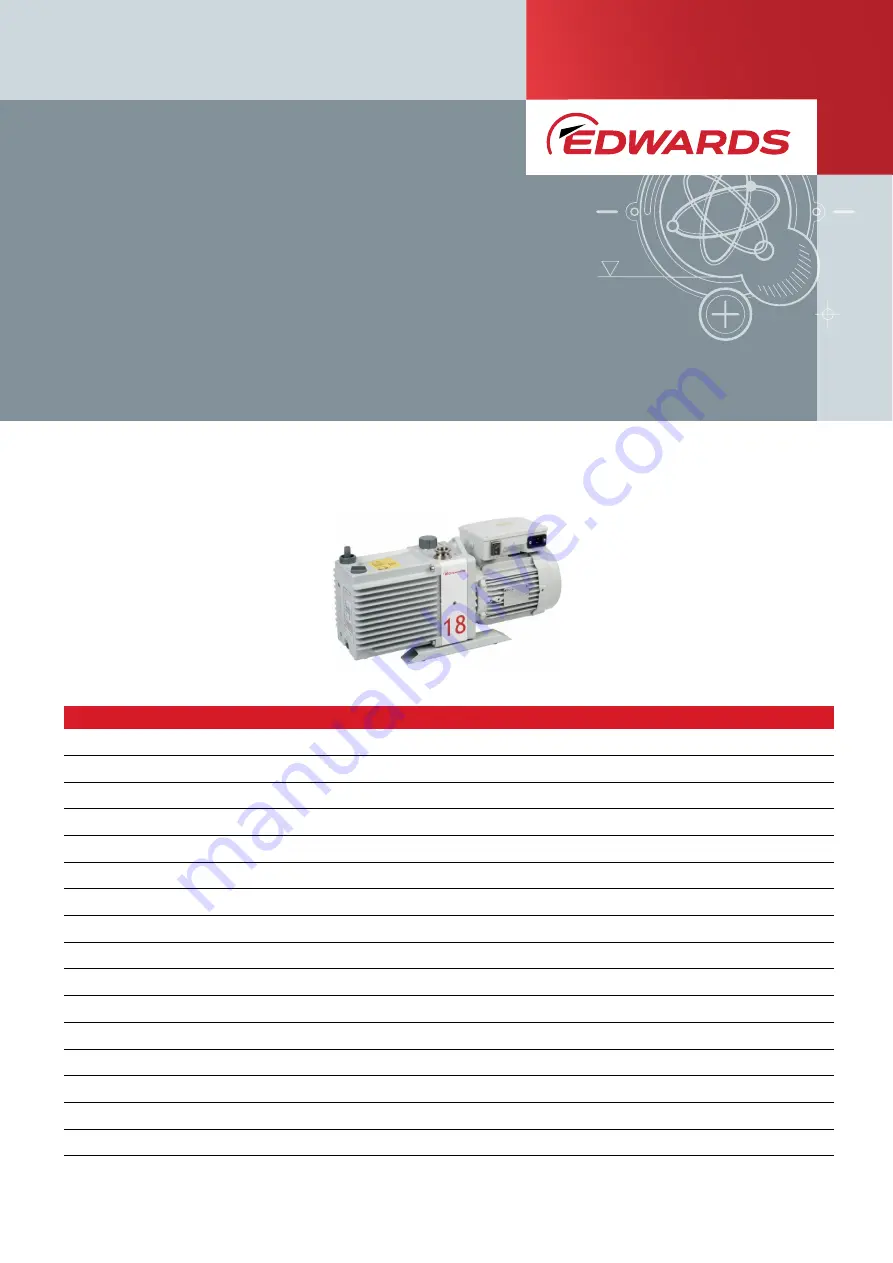
E1M18 and E2M18 Rotary
Vacuum Pumps
INSTRUCTION MANUAL
A34310880_T
Original instructions
edwardsvacuum.com
DESCRIPTION
ITEM NUMBER
E1M18, 100/200 V, 50 Hz or 100-105/200-210 V, 60 Hz, single-phase
A34315904
E1M18, 115/230 V, 60 Hz, single-phase
A34315981
E1M18, 220-240 V, 50 Hz, or 230-240 V, 60 Hz, single-phase
A34315903
E1M18, 200-230/380-460 V, 50/60 Hz, three-phase
A34310940
E1M18, 220-240 V, 50 Hz, or 230-240 V, 60 Hz, single-phase (Amphenol)
A34316903
E1M18, 110/200-240 V, 50 Hz, or 115-120/200-230 V, 60 Hz, single-phase
A34317984
E1M18, 110/200-240 V, 50 Hz, or 115-120/200-230 V, 60 Hz, single-phase, fomblin filled
A34325984
E2M18, 100/200 V, 50 Hz or 100-105/200-210 V, 60 Hz, single-phase
A36315904
E2M18, 115/230 V, 60 Hz, single-phase
A36315981
E2M18, 220-240 V, 50 Hz, or 230-240 V, 60 Hz, single-phase
A36315903
E2M18, 200-230/380-460 V, 50/60 Hz, three-phase
A36310940
E2M18, 110/200-240 V, 50 Hz, or 115-120/200-230 V, 60 Hz, single-phase
A36317984
E2M18-FF, 200-230/380-460 V, 50/60 Hz, three-phase
A36321940
E2M18-FF, 100/200 V, 50/60 Hz, single-phase
A36325904
E2M18, 220-240 V, 50 Hz, single-phase
A36325912
E2M18, 110/200-240 V, 50 Hz, or 115-120/200-230 V, 60 Hz, single-phase, fomblin filled
A36325984
Содержание A34310940
Страница 6: ...This page has been intentionally left blank...
Страница 56: ...edwardsvacuum com...