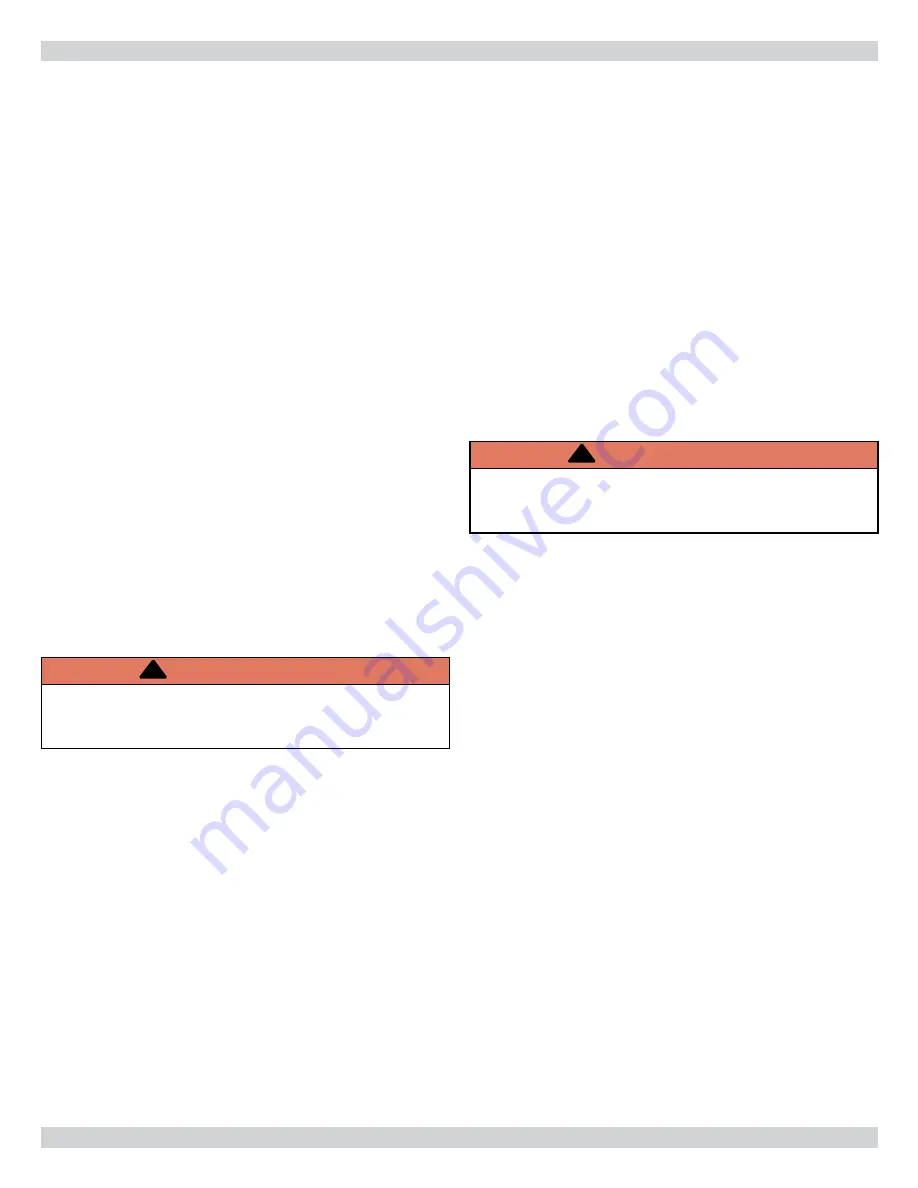
• High limit control is mounted in ½” NPT control well
and ¾” X ½” bushing on top of front boiler section at
hot water outlet.
• High limit control is tied in with boiler control and is
factory set at 200°F (94°C) water temperature.
• High limit setpoint is fi eld adjustable and may be set
anywhere between 100°F (38°C) and 200°F (94°C),
with maximum high limit setpoint not exceeding 200°F
(94°C). Field high limit setpoint adjustment for each
installation depends on heating system requirements.
• High limit control automatically resets when boiler water
temperature decreases below high limit setpoint value
by differential setpoint value. (Adjustable differential
from 5°F (2.8°C) to 30°F (16.7°C).
• Boiler operating temperature (temperature curve) is
calculated and set in boiler control parameters.
11.13 Casting Temperature Safety Switch
• Casting temperature safety switch, 230°F (110°C)
setpoint, shuts off power to boiler control in event of
boiler lack of or loss of water.
• Casting temperature safety switch is installed on top of
aluminum boiler section behind supply piping.
• Failure code is displayed on digital readout. Fault
requires manual reset of casting temperature safety
switch to restart boiler. Press reset on user interface
panel also.
• Verify boiler is properly fi lled with water and no air is
trapped in top of casting (check cap on Cam Vent at
heat exchanger) before resetting.
WARNING
Burn and scald hazard. Never run cold water into a
hot, empty boiler. Failure to follow these instructions
could result in death or serious injury
!
11.14
Circulator Pump
• Circulating pump moves water through closed loop
supply and return piping systems, terminal heating
equipment (fi nned tube radiators, etc.) and back
through boiler for reheating.
• Properly size circulator pump to overcome frictional
losses (usually measured in feet of water, also referred
to as “pump head loss”) of supply and return piping
systems and boiler to provide required hot water fl ow
rates.
• Circulator pump is furnished in carton within boiler
cabinet.
• Locate circulator(s) on downstream (“pumping away”)
side of expansion tank.
11.15 Blocked Vent Safety Assembly
Blocked vent safety assembly incorporates two pressure
switches designed to discontinue operation of boiler if there
is a problem with blower or venting system.
The normally open switch closes upon initiation of blower
and functions as air proving switch.
The normally closed switch opens if there is a blockage in
combustion air intake or exhaust vent pipes.
11.16 Drain Valve
Manual drain valve drains water in heating system,
including boiler, hot water supply and return piping systems
installed above drain valve.
Drain valve is installed in return piping at bottom front of
boiler section. Any piping installed below elevation of drain
valve requires additional drain valves to be installed at low
points in piping system in order to drain entire system.
WARNING
Burn and scald hazard. Safety relief valve could
discharge steam or hot water during operation.
Install discharge piping per these instructions.
!
11.17 Safety Relief Valve
• Each boiler must have a properly sized and installed
American Society of Mechanical Engineers (ASME) rated
safety relief valve.
• Furnished safety relief valve automatically opens at 30
psig pressure to relieve strain on boiler and heating
system from increasing pressure.
• Pipe Safety relief valve discharge with same size pipe
as valve discharge opening to open drain, tub or sink,
or other suitable drainage point not subject to freezing.
11.18 External Condensate Pump (optional)
For installations where there is no fl oor drain or other
appropriate drainage receptacle available to receive
condensate from boiler, external fl oat activated condensate
pump with integral sump is required. Condensate pump can
be piped to remote tie in point to sanitary sewer system.
For this application, boiler must be installed so that proper
pitch of piping to external condensate reservoir (sump) can
be accomplished. Use wood frame or concrete blocks to
raise boiler as required for proper installation.
11.19 Concentric Vent/Air Intake Termination
(Optional)
Optional concentric vent/air intake termination utilizes
single opening per each appliance through wall or roof of
structure.
11 - CONTROLS AND ACCESSORIES
22
Содержание Olsen OQ95M-200
Страница 2: ...1 DIMENSIONS OPENING FOR SAFETY RELIEF VALVE DISCHARGE PIPE 30 785mm 39 1 1m 18 458mm 2 ...
Страница 27: ...APPENDIX A BOILER PIPING AND WIRING Electrical Wiring Diagram 27 ...
Страница 49: ...49 NOTES ...
Страница 50: ...50 NOTES ...
Страница 51: ...51 Company Address Phone Company Name Tech Initials Service Performed Date SERVICE RECORD ...
Страница 52: ...ECR International 2201 Dwyer Avenue Utica NY 13501 web site www ecrinternational com ...