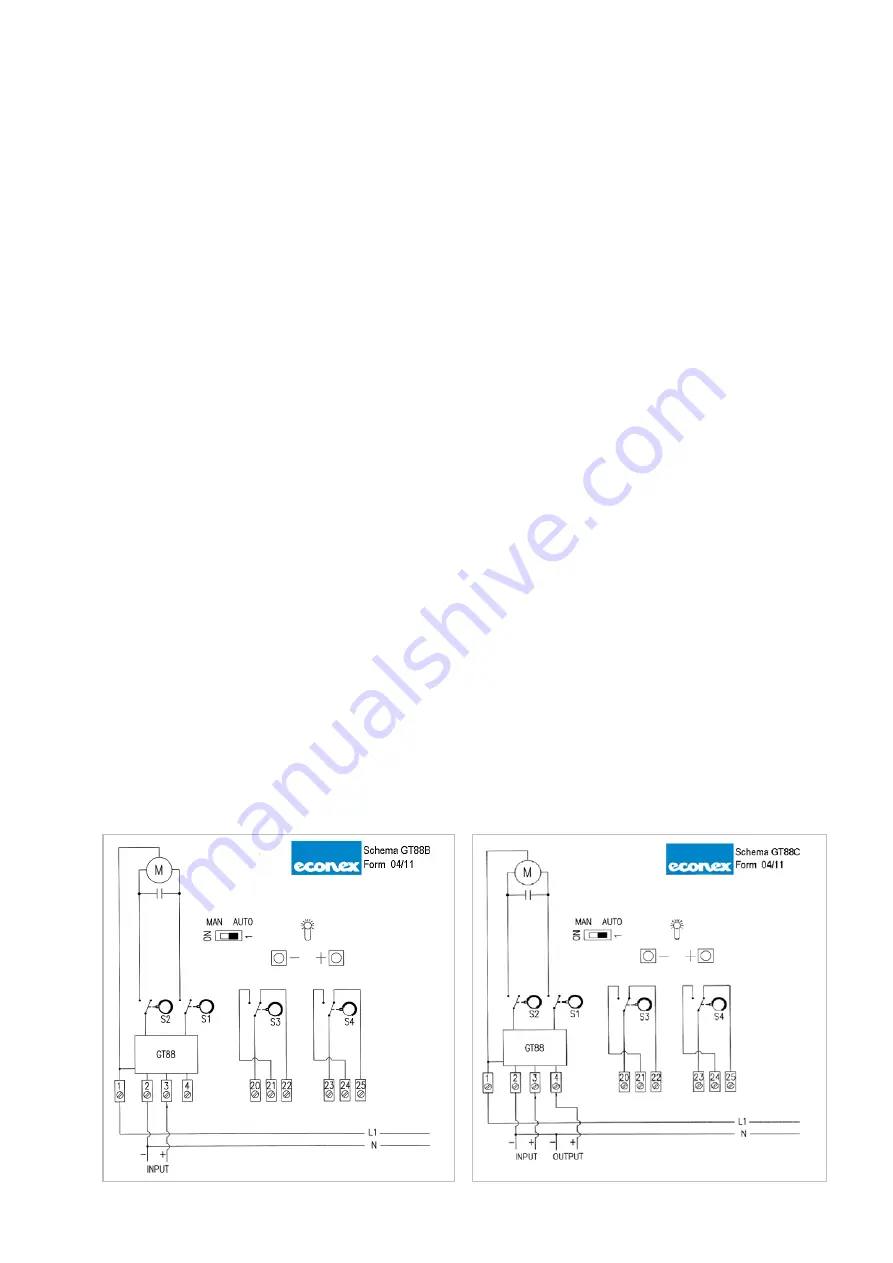
AR2…SE.. Instructions
4
Form 120127
4 ELECTRIC
CONNECTIONS
4.1
After having installed the AR gear motor and before fastening it mechanically to
the device to be controlled, proceed with wiring and earthling.
4.2
The wiring diagrams are reported both in the attached technical bulletin and on the
plate inside the cover.
4.3
Warning: before servicing make sure that power supply is disconnected by means
of the two-pole-switch [phase and neutral]. In case of non-observance, damages
to people and to the equipment may occur.
4.4
External supply voltage transformer with load
>
15 VA protected against overloading.
4.5
To accede to the internal wiring terminal board remove the cover by loosening the
4 fastening screws.
4.6
On the frame of the AR gear motor are located 2 threaded holes for the fitting of
the conduit plug PG 13.5 and 2 extra ¼” holes [on request] if pressurizing of the
motor is requested.
4.7
All wires must comply with local prescriptions and, in any case, their section must
be ranging between 1 and 1.5 mm².
4.8
Connection piping recommended HO7V-U…G 1.5 mm².
4.9
The wiring diagrams show the AR2...E gear motor at end position closed [0°].
W
ARNING
An immediate accident may occur onto circuit board due to wrong wiring.
Check
it
carefully
before servicing.
4.10
The auxiliary microswitches are single-pole double through and are voltage-free.
4.11
The auxiliary microswitches rating is 0,5 A / 48 Vdc e Vac.
4.12
Make sure that power supply and system frequency match to the values indicated
on the AR gear motor’s plate.
W
ARNING
Transformer power supply must be separated from that of the gear motor.
4.13
The low-tension signalling cables [tension lower than 48V] must be laid separately
from the higher-tension-conduits [tension higher than 48V]. In case they are laid in
a single channel, screened cables must be used.
Valid only for AR2…SE1, SE2, SE7 e SE8