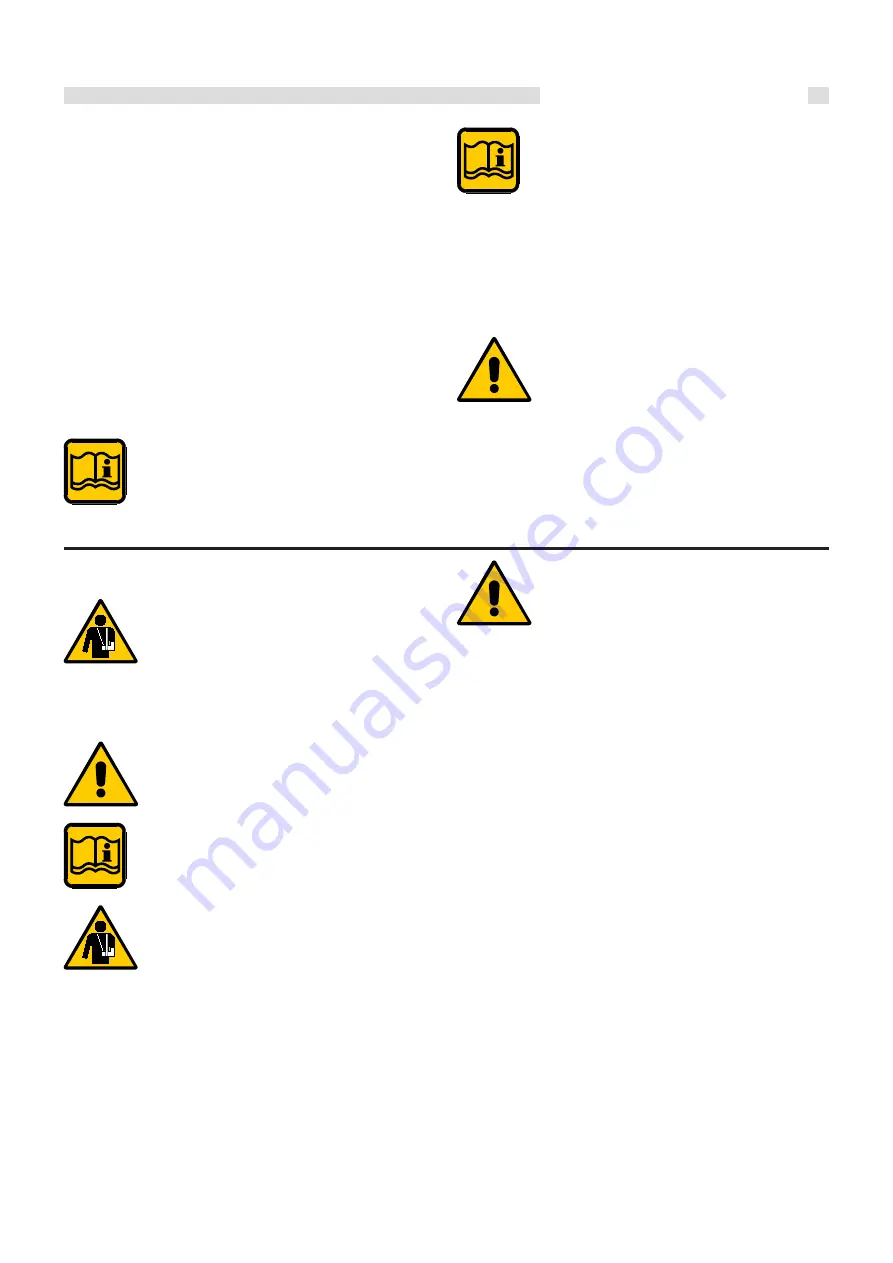
Installation instructions
23
If the boiler was without electric power, after a
certain idle period, the pump could be blocked.
Before turning on the main switch, the pump must
be unblocked by operating as follows:
Introduce a screwdriver in the hole below the
protective screw in the centre of the pump intended
for this purpose and turn the pump shaft clockwise.
After having unblocked the pump, tighten the
protective screw and make sure there is no water
leakage.
ATTENTION!
After removing the protective screw, a small amount
of water could leak out. Dry off all wet surfaces
before powering the boiler.
3.12 - CONNECTING GAS
Danger!
The gas connection must be carried out only
by a qualified installer who must respect and
apply that foreseen by relevant laws in force in
the local prescriptions of the supply company.
Incorrect installation can cause damage to
persons, animals and objects for which the
manufacturer cannot be held responsible.
Before installation, we recommend a thorou-
gh inner cleaning of all fuel adduction piping
to remove any residue which could jeopardise
proper operation of the boiler.
Attention!
Make sure that there are no mechanical tension
points while connecting gas to avoid the risk
of leakage!
Perceiving the smell of gas:
a) Do not turn electric switches on or off, use
a telephone or any other object which can
create sparks.
b) Immediately open doors and windows to
create an air current to air out the room;
c) Shut the gas cocks.
d) Request the intervention of professionally
qualified personnel.
As a precaution against gas leaks, we
recommend installing a monitoring and
protection system consisting in a gas leak
detector coupled with a shut-off solenoid
valve on the gas feed line.
The supply pipes must have a cross-section
sufficient for the flow rate of the burner.
You should nonetheless comply with the “General installation
regulations”.
Before commissioning an internal gas distribution system and
therefore before connecting it to the gas meter, check its sealing
carefully.
If any part of the system is out of sight, the sealing test must be
done before the pipes are covered.
Before connecting the appliances, the system must be tested
with air or inert gas at a pressure of at least 100 mbar.
The following operations and checks must also be performed
while commissioning the system:
- Open the meter and air release valve to bleed the air from
the piping of the appliances, proceeding one appliance after
another.
- With the appliances closed, check that there are no gas leaks.
The pressure gauge must show no pressure drop during the
second quarter of an hour from the start of the test.
Gas leaks must be found with a soapy solution or similar
product and eliminated. Never look for gas leaks with an
open flame.
following phases:
- Open the radiator air release valves.
- Open the filling tap gradually, making sure that the automatic
air release valves installed on the system work properly.
- Close the radiator air release valves as soon as water comes
out.
- Check the pressure gauge until pressure reaches
approximately 1 bar.
- Close the filling tap and bleed air once again through the
radiator air release valves.
- Make sure that all the connections are watertight.
- After commissioning the boiler and bringing the system to
the operating temperature, stop the pumps and repeat the
air bleed operations.
- Let the system cool off and, if necessary, return the water
pressure to 1 bar.
NOTE
The water pressure in the heating system must not be drop
below 1 bar; open the filling tap on the boiler when
pressure is too low.
This operation must be performed with the system
cool.
NOTE
Содержание TRIMAX 3SC 840-N
Страница 45: ......