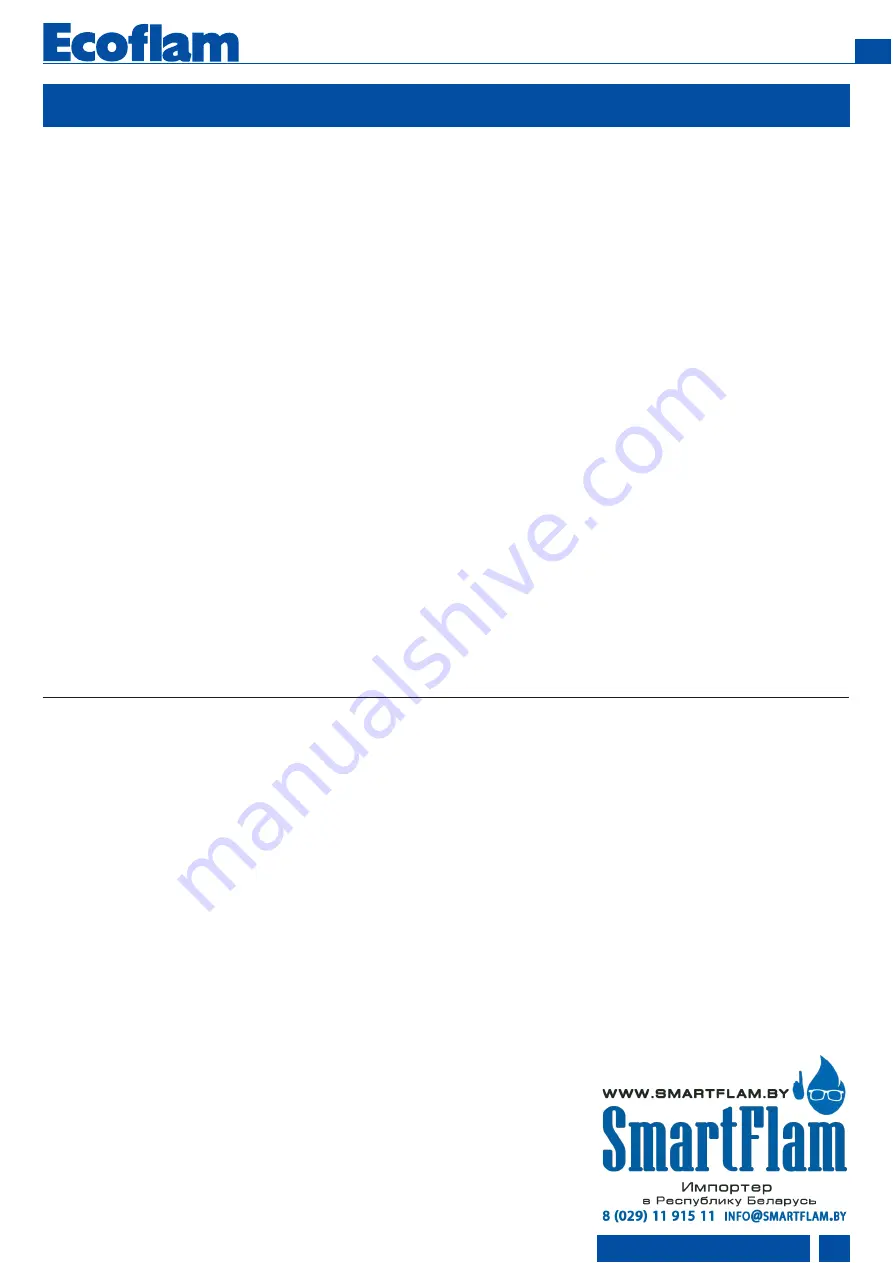
9
www.ecoflam-burners.com
EN
420010813300
OIL OPERATING MODE - GENERAL SAFETY FUNCTIONS
GENERAL SAFETY FUNCTIONS
In case a flame does not develop when
starting the burner (fuel release) the
burner will shut off at the end of the safety
period (safety lock-out).
A safety lock-out will also occur in the case
of flame failure during operation, air flow
failure during the pre-ventilation phase and
pressure failure during the whole period of
burner operation.
Any failure of the flame signal at the end of
the safety period and a flame signal during
the pre-ventilation phase (external light
control) will result in a safety lock-out with
the control box being locked.
The trouble is indicated by the trouble
signal lamp lighting up.
The control box can be unlocked
immediately after a safety lock-out by
pressing the unlocking key. The program
unit will return to its starting position and
proceed with the restart of the burner.
A voltage failure will result in a regular
shut-off of the burner. Upon voltage
recovery there may be an automatic
restart unless another interlock is
provided, e.g. by the safety system. In any
case of trouble the fuel oil supply will be
shut off right away. The program unit will
stop at the same time causing also the
trouble location indicator to stop.
The symbols will indicate the kind of
trouble.
START-UP MODE
As soon as the furnace system is required
to supply heat the burner control circuit will
close and the program be started. After the
program has run down the burner will start.
The air damper is closed when the burner
iis out of operation.
The automatic furnace controller controls
and monitors the starting function.
The electric actuator opens the closed air
damper to its full-load position so that the
burner will sweep the furnace
compartment and exhaust ports at the
required air flow rates. At the end of the
specified pre-ventilation time the air
damper will be moved into its partial load
position. This operation will be followed by
the pre-ignition procedure and the oil feed
start.
The solenoid valves will open and thus
allow the pressurized oil to flow to the
nozzle and to the return line.
The oil will be atomized, mixed with the
combustion air and ignited.
A safety period is provided to allow the
flame to develop a proper and steady
pattern.
On the termination of the safety period, a
flame signal must have been received by
the automatic furnace controller via the
flame monitor and remain on until the
regular shut-off.
The startup program of the burner has now
been completed.
OIL OPERATING MODE
After the flame has developed the load
regulator will be enabled which brings the
burner into its operating position.
The load regulator will now control the
burner automatically between its partial-
load and full-load stages.
Depending on the heat demand, the
electric actuator of the mechanical
compound control system will be fed with
the OPEN or CLOSE signal via the
regulator and thus increase or decrease
the oil and air flow rates.
This compound control system will vary
the positions of the oil control valve and air
damper and thus regulate the oil flow rate
in conjunction with the air flow rate. The
burner can either be controlled in two-
stage sliding mode or, if a respective
controller is provided, in stepless control
mode.
The stepless control will allow the burner
to be operated at any desired stage
between its partial-load and full-load
positions. The burner will be turned off
from its partial-load position. The air
damper will be closed when the burner is
out of operation and will thus prevent cold
air flowing through the burner chamber,
heat exchanger and chimney.
The interior cooling losses will be greatly
minimized.
Содержание MAIOR P 500-1 PRE
Страница 31: ...31 www ecoflam burners com EN 420010813300...