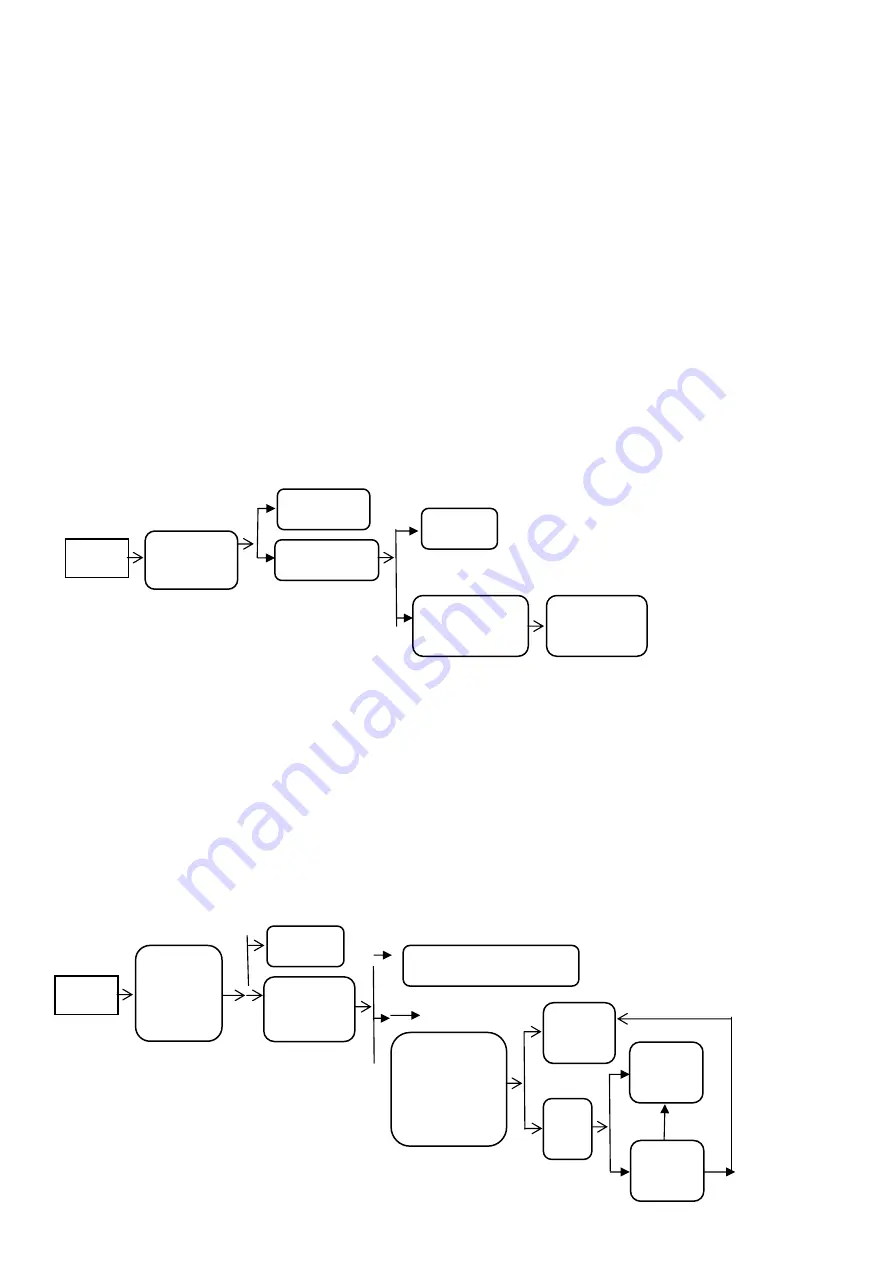
32
Two: sensor and its related faults
1. Overview of faults
Short-circuit and open circuit of the temperature sensing bag, all of which have fault code display.
Indoor: environmental sensor failure, pipe temperature sensor failure.
Outdoor: the environmental sensor, outdoor pipe temperature sensor and exhaust temperature sensor are faulty.
Sensor resistance is abnormal
If the sensor resistance is abnormal or the sensor with wrong specification is replaced during maintenance, the fault code of the
sensor is generally not displayed, but it may cause abnormal protection frequency limiting, abnormal protection shutdown and other
related codes to be displayed. Faults caused by abnormal sensor resistance are invisible and complicated to deal with. Whether the
sensor resistance is normal or not can be rechecked in case of abnormal phenomena.
2. Cause
of
failure
When the sensor is open or short-circuited, the detection circuit voltage is close to the power supply voltage or 0V. The power
supply voltage of outdoor unit is 3.3V or 5V, and that of indoor unit is 5V.
3. Possible failure point
Poor contact and looseness of sensor terminal
Sensor circuit components loose, open circuit, virtual welding
Sensor resistance offset
Sensor circuit resistance offset, capacitor leakage
The sensor specification is wrong, for example, 10K is used as 50K
Abnormal controller chip
The sensor bulb is short-circuited with the shell or copper pipe
4. Fault handling flow
Three: indoor fan failure
1. Overview of faults
"F0" is displayed indoors, and F0 fault is mainly to prevent abnormal rotating speed from turning into fault of electronic control and
refrigerant circulation system.
2. Cause
of
failure
When the fan is turned on, the indoor main chip detects that the motor speed is lower than 300 rpm for 1 minute continuously
(through the fan feedback circuit), and the controller reports the fault of the internal fan.
3. Possible
failure
point
Whether the motor is installed correctly, whether the terminals are plugged firmly, whether the blades are stuck, whether the
eccentric tuyere of the sliding bearing in the rubber ring is blocked and the wind speed is too slow.
Fan starting capacitor is damaged
The internal controller is abnormal
The motor body is stuck and damaged (peculiar smell, open or short circuit of windings are abnormal. When measuring the winding
resistance, pay attention to distinguish whether the thermal protector acts due to the high temperature of the motor casing). Note: If
there is an "FO" fault in case of uncertainty, please check the fan blades and motor equipment and add proper lubricating oil.
4. Fault
handling
flow
NO
YES
Sensor
failure
Is the terminal plug
loose or poor
contact
Reconnect and plug
in the terminals
Is the sensor resistance
normal
Replace sensor
Is the sensor lead broken
or short-circuited by other
devices or copper pipes
Replace the sensor
and readjust the
sensor routing
NO
NO
YE
S
YE
S
NO
YE
S
Internal fan
failure
Whether the
contact between
motor control
output and
feedback end is
firm
Reinsert the
terminals
Turn the blades by
hand to see if they
rotate smoothly
Re-assemble blades, motors and sliding
bearings correctly
Measure whether the
output voltage at the
control end of PG motor
is greater than 50V
within one minute after
being powered on again
and the air deflector is
turned on.
Replace the
main
controller of
the same
model
Motor
startin
g
Test whether
there is
feedback
signal
Replace the
internal
board
NO
NO
NO
YE
S
YE
S
YE
S
NO
Содержание CM2-H16/4DR2
Страница 1: ...Service manual FREE MATCH 50Hz R32 Models СM2 H16 4DR2 СM3 H22 4DR2 2022 06 ...
Страница 3: ...1 1 Summary and Features Outdoor Unit CM2H 1644A23 CM3H 2228A23 ...
Страница 11: ...9 4 Construction Views 4 1 Outdoor Unit CM2H 1644A23 Unit mm ...
Страница 12: ...10 CM3H 2228A23 Unit mm ...
Страница 27: ...25 8 Exploded Views and Parts List 8 1 Outdoor Unit Model CM2H 1644A23 ...
Страница 29: ...27 Model CM3H 2228A23 ...
Страница 47: ...41 ...