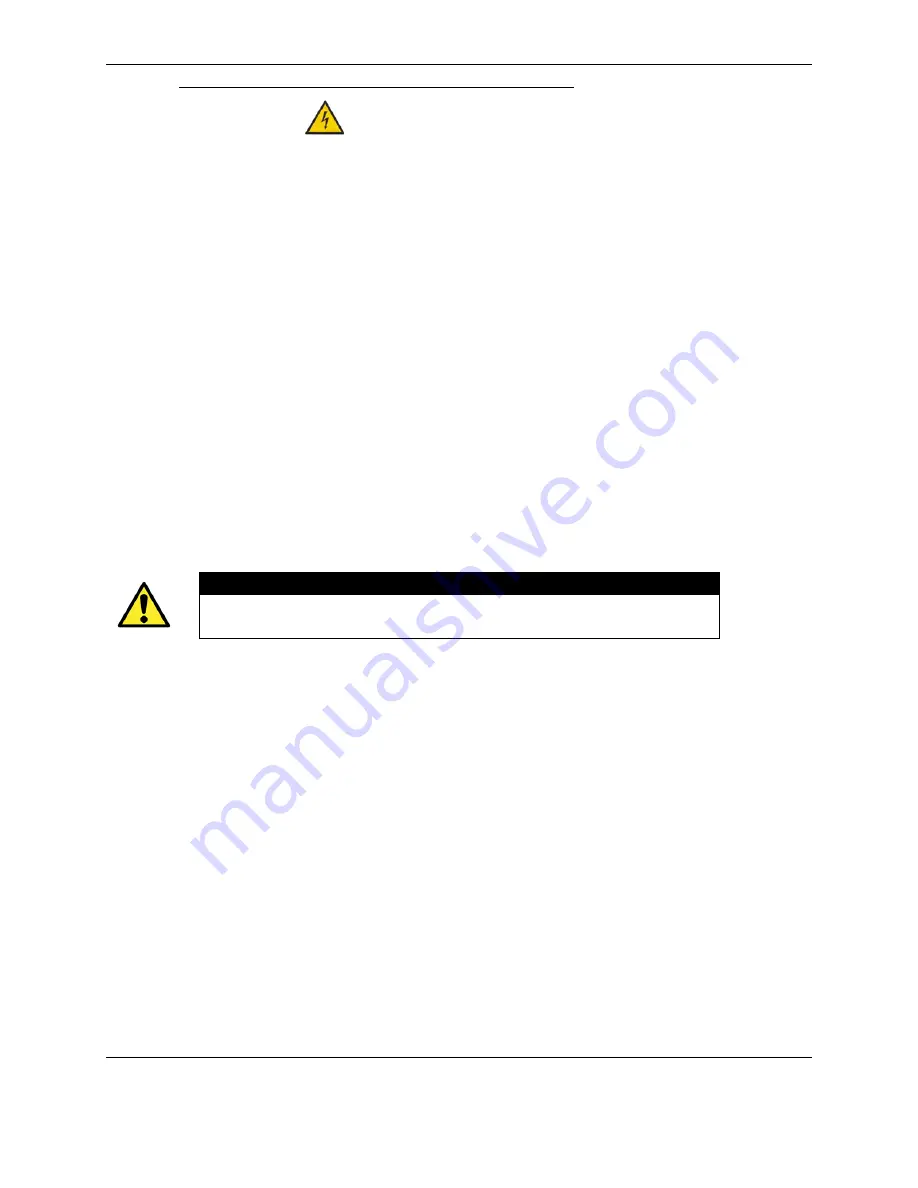
Page | 11
This document is proprietary. No disclosure, reproduction or use of any part thereof may be made without the expressed
written permission of Ebbco Inc. or its subsidiaries.
Section 3:
System Installation and Operation Procedures
3.5 Start-Up Procedure
1) Fill the clean side of the system tank (smaller side) with filtered water (min 20 micron) with a TDS
level no greater than 150 PPM. Fill the clean tank so it completely fills and spills over the dividing
baffle into the dirty tank (larger side). Keep filling the clean tank until the water level inside of the dirty
tank is just below the city water make-up port.
2) Prime the system pump by loosening the prime nut on the top of the pump housing and letting the air
bleed out. Tighten the nut once water is flowing out of the port.
Note: While clockwise may typically be the normal factory set rotation, some motors do rotate
counter-clockwise. Every pump leaves our facility with an arrow affixed to the motor correctly
identifying the motor rotation direction. Advise said arrow for proper motor rotation direction.
3) The motor(s) have been synchronized at the factory, but if they are running in reverse have a
qualified industrial electrician swap over one of the incoming power lines at the electrical panel.
4) Carefully open the bleeder valve on top of vessel # 2 to bleed out the trapped air. Close the bleeder
valve once all the air is purged and fluid start to escape the valve.
Note: The inlet pressure gauge (on vessel # 1) should read approximately 38 PSI.
5) Water should be flowing from the clean tank over the dividing baffle into the dirty tank. The fluid may
appear cloudy and/or have a foam layer on top after initial startup or with installation of a new filter.
This is normal and should clear itself up within due time.
6) Ensure the ozone generator is on once the water quality clears up; bubbles should be coming out of
the dispersion stone (located inside the clean tank) and rising towards the surface.
7) Let system run until the TDS meter on the electrical panel reads within the preset TDS level (40
– 100
PPM).
8)
After the previous steps have been accomplished, start sending water to the customer’s water-jet by
turning feed pump on via the control switches on the electrical panel.
Note
:
The Float Valve Assembly on the water make-up in the dirty side of the
Closed Loop should be set to maintain a water depth of 10 - 12"