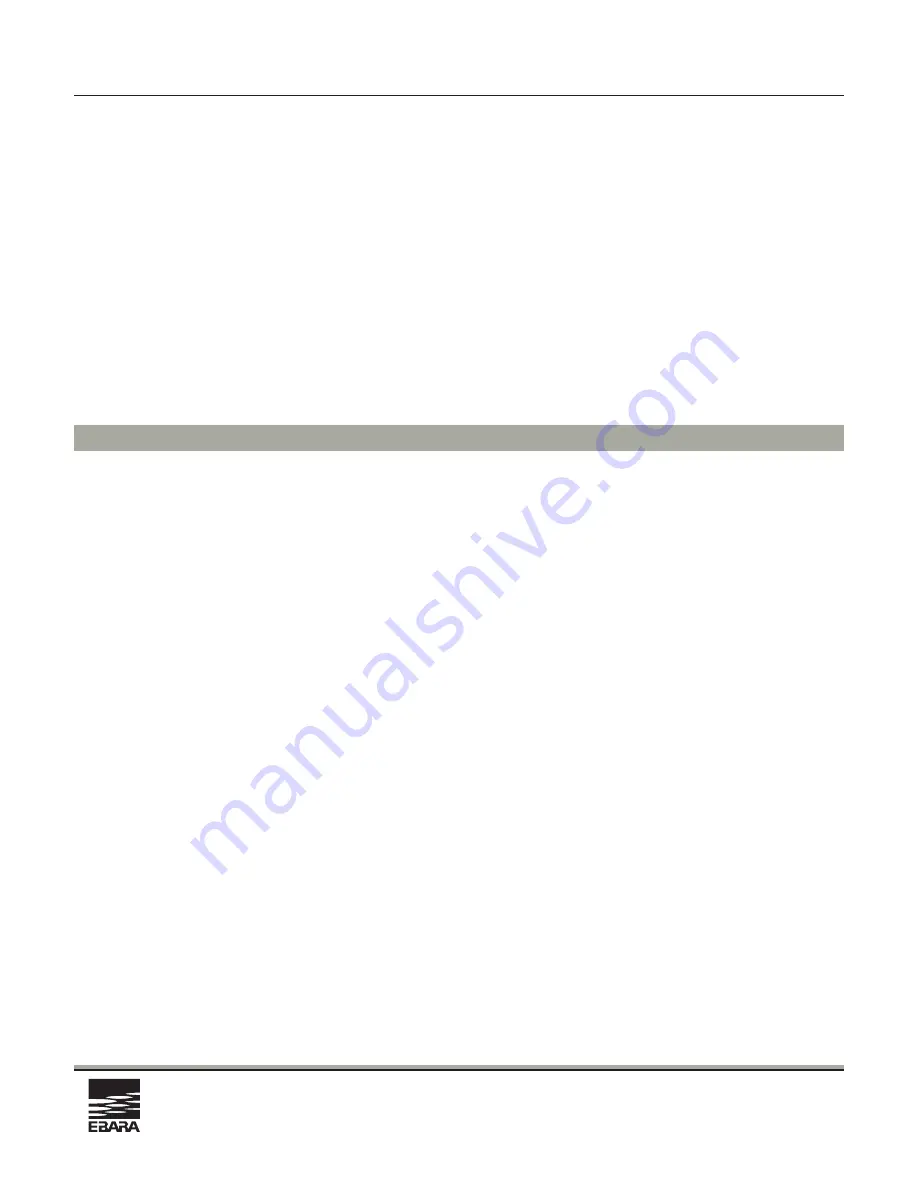
13
EBARA
PUMPS AMERICAS CORPORATION
www.pumpsebara.com
(t) 803.327.5005
(f) 803.327.5097
rev. 03/22
End Suction Centrifugal
GS Series
7.2
STARTING THE PUMP
1.
Shut off the main delivery valve. Open the suction valve if it is closed.
2.
Turn on and off the switch to start the motor once or twice, to ensure that there are no faults in the
startup.
3. When the rotation speed remains stable at the nominal speed, gradually open the delivery valve.
4.
Check that there are no significant variations in the pump pressure and in the current absorbed by the
motor. Check that there are no significant vibrations and/or unusual noises.
5. Follow the same procedure during subsequent startups if the operating conditions are normal, observing
the instructions in Chapter 8. Maintenance.
7.3
STOPPING THE PUMP
Before stopping the pump, you are advised to close the delivery valve gradually.
If the pump stops due to a sudden lack in the power supply, disconnect the motor switch. This will avoid the
pump starting up again as soon as the power supply returns, thereby endangering staff.
8. MAINTENANCE
Maintenance operations must be performed by qualified personnel: an error may lead to damage caused
by electrical discharge, fire or malfunctions that in turn could lead to an accident.
Make sure that the operating power switch is disconnected during maintenance; the pump could start up
suddenly if it is in automatic mode.
If the liquid being pumped is hot water, keep at a safe distance until it has cooled down. Similarly, do not
touch the surface of the motor without making sure that the temperature has dropped to a tolerable level.
8.1
DAILY INSPECTION
1.
Significant variations in pressure, capacity, electricity, vibrations or noise may be a sign of a malfunction
of the pump. Refer to section 8.5 “Troubleshooting”. It is advisable to keep a daily register on the
operating conditions to allow discovering any symptoms that may be the result of a potential failure.
2. The maximum temperature for the bearing is 104°F above the ambient temperature, with a maximum
total limit of 176°F
3. Generally, the mechanical seal does not show any leaks. Sometimes, at the beginning of operation
there is a small leak of water which then gradually decreases. If, during normal operation, there is a
major leak of water, you need to replace the seal.
Содержание GS Series
Страница 2: ......