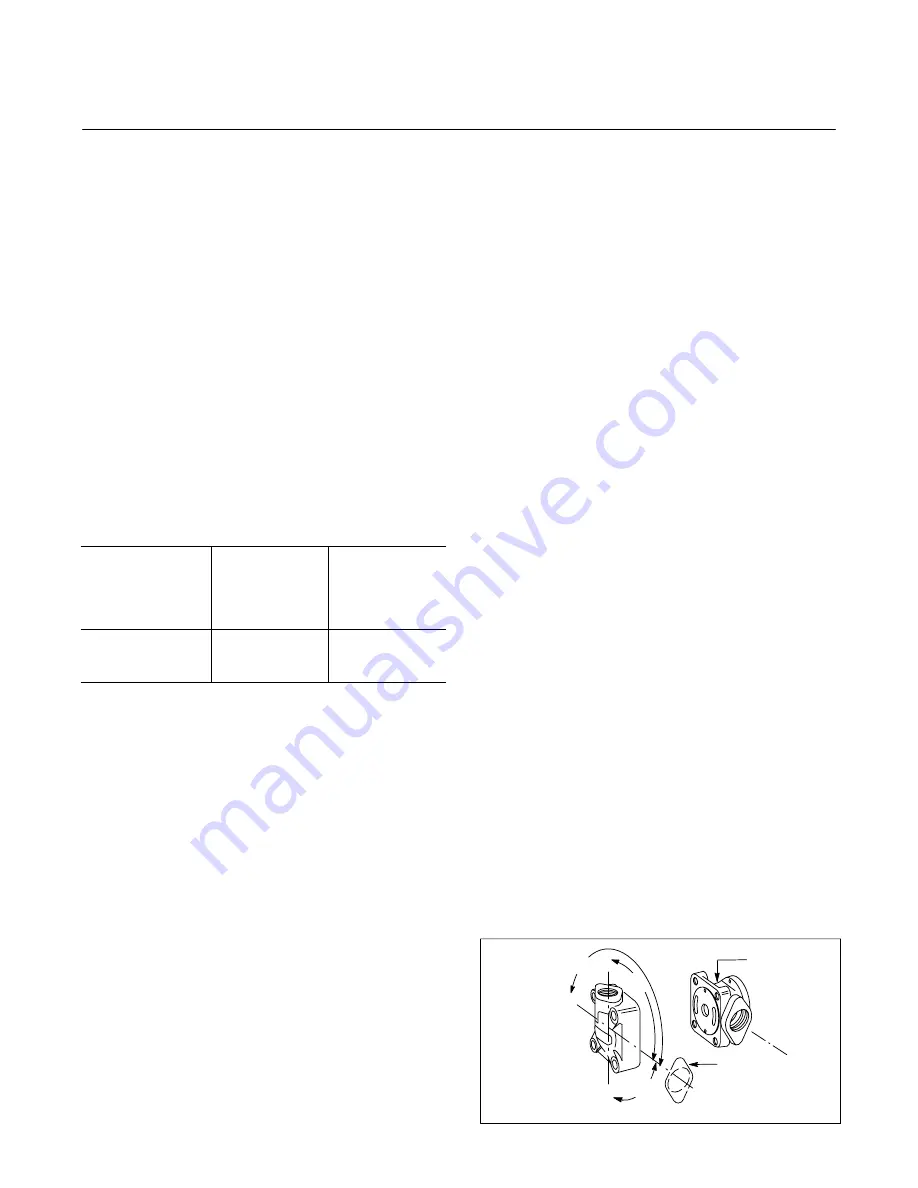
9
3. Certain other types of petroleum oils are suitable for
Mobile hydraulic service if they meet the following provisions:
a. Contain the type and content of antiwear
compounding fould in MS crankcase oils or have passed
pump tests similar to those used in developing the antiwear
type hydraulic oils.
b. Meet the viscosity recommendations shown in
Table 3.
c. Have sufficient chemical stability for Mobile
hydraulic system service.
The following types of oil are suitable if they meet the above
three provisions:
– Series 3 Diesel Engine Oil
– Automatic Transmission Fluid Types A, F and
DEXRON
– Hydraulic Transmission Fluid Types C-1 and C-2
Table 3 summarizes oil types recommended for use with
Vickers equipment in Mobile hydraulic systems by viscosity
and service classification.
Hydraulic System
Operating
Temperature
Range
(Min.* to Max.)
SAE
Viscosity
Designation
American
Petroleum
Institute (API)
Service
Classification
0
°
F to 180
°
F
0
°
F to 210
°
F
50
°
F to 210
°
F
10W
10W-30**
20-20W
MS
MS
MS
* Ambient start-up temperature
** See paragraph on Viscosity Index
Table 3. Oil Recommendations
The temperatures shown in Table 3 are cold start-up to
maximum operating. Suitable start-up procedures must be
followed to insure adequate lubrication during system
warm-up.
Arctic conditions represent a specialized field where
extensive use is made of heating equipment before starting.
If necessary, this, and judicious use of SAE 5W or SAE
5W-20 oil in line with the viscosity guide lines shown in the
table, may be used. Dilution of SAE 10W (SM) oil with
maximum of 20% by volume of kerosene or low temperature
diesel fuel is permissible. During cold start-up, avoid high
speed operation of hydraulic system components until the
system is warmed up to provide adequate lubrication.
Operating temperature should be closely monitored to avoid
exceeding a temperature of 130
°
F with any of these light
weight or diluted oils.
Where special consideratins indicate a need to depart from
the recommended oils or operating conditions, see your
Vickers sales representative.
Cleanliness
Thorough precautions should always be observed to insure
the hydraulic system is clean:
1. Clean (flush) entire new system to remove paint, metal
chips, welding shot, etc.
2. Filter each change of oil to prevent introduction of
contaminants into the system.
3. Provide continuous oil filtration to remove sludge and
products of wear and corrosion generated during the life of
the system.
4. Provide continuous protection of system from entry of
airborne contamination.
5. During usage, proper oil filling and servicing of filters,
breathers, reservoirs, etc., cannot be over emphasized.
F. Overload Protection
A relief valve must be installed in the system, unless it is an
integral part of the pump. The relief valve limits pressure in
the system to a prescribed maximum and protects the
component from excessive pressure. The setting of the relief
valve depends on the work requirements of the system and
the maximum pressure ratings of the system components.
G. Port Positions
The pump cover can be assembled in four positions with
respect to the body. A letter in the model code (Table 2)
identifies the cover position as shown in Figure 6.
Disassembly and assembly procedures are in Section VI, B
and D.
H. Start-Up
With a minimum drive speed of 600 RPM, a pump should
prime almost immediately, if provision is made to initially
purge the air from the system. Failure to prime within a
reasonable length of time may result in damage due to lack
of lubrication. Inlet lines must be tight and free from air leaks.
However, it may be necessary to crack a fitting on the outlet
side of the pump to purge entrapped air.
Figure 6.
Opposite
Inlet
90
°
Clockwise
from Inlet
A
D
C
In Line
With Inlet
Inlet Position
Pump Body
180
°
90
°
90
°
B