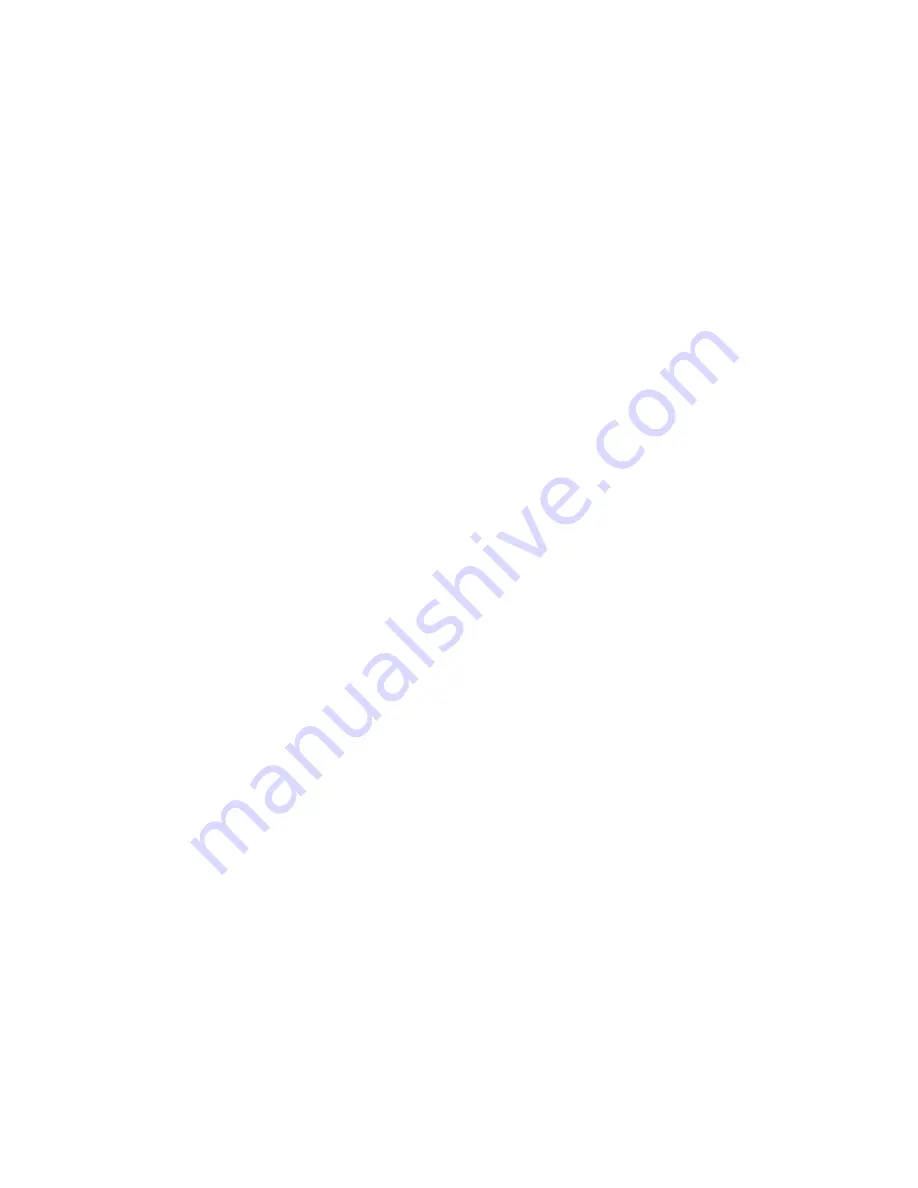
- Page 11 -
I.B. 8926-1
CONDUIT
Install conduit in such a manner as to prevent water from
entering and accumulating in the conduit or the enclo-
sure. Eliminate sags in conduit. Have the conduit enter
the motor control center (MCC) in the areas designated
for conduit entry on the plan views. See pages 30 and
31 of this booklet and outline drawings shipped with the
MCC. Keeping conduit within the shaded areas shown
in the plan views will avoid cable interference with struc-
tural members and live bus. (See Part 12.)
WIRING
Install the line and load conductors sized in accordance
with the NEC. Use copper wire only for control ter-
minations. Use copper wire only for power termi-
nations unless they are marked “CUIAL.” Use con-
ductors with a temperature rating of 75
°
C or higher, but
regardless of the insulation temperature rating select the
wire size on the basis of 75
°
C wire ampacity. Using a
higher temperature wire ampacity table often results in
a smaller cross-section of copper available for carrying
heat away from terminals.
Install insulated wire and cable at a temperature suffi-
ciently warm to prevent the insulation from cracking or
splitting.
When more than one conduit is run from a common
source or to a common load, be sure to have each con-
duit carry conductors from each phase and the same
number of conductors per phase. If the phase conduc-
tors are not distributed uniformly, eddy currents will be
generated in the steel between the conduits.
Locate conductors within the MCC to avoid physical dam-
age and to avoid overheating. Secure incoming power
lines in a manner adequate to withstand the forces which
will act to separate the conductors under short-circuit
conditions. Use the cable ties furnished in both horizon-
tal and vertical wireways to support the load and inter-
connection wire. Use a shielded communications cable
inside of flexible metal conduit to protect very low volt-
age signals transmitted to or from a computer or pro-
grammable controller.
Lugs furnished with the MCC and its components are
for Class B and Class C stranding. Verify the compatibility
of wire size, type, and stranding with the lugs furnished.
Where they are not compatible, change the wire or lugs
accordingly. If crimp lugs are used, crimp with the tools
recommended by the manufacturer.
Use care in stripping insulation to avoid nicking or ring-
ing the metal.
All field wiring to control units should be made in accord-
ance with the wiring drawings that are furnished with the
control center. Load and control wiring can be brought
in through the upper and/or lower horizontal wireways.
Determine the type of wiring installed in the control center
(NEMA Type B or C) and proceed per the appropriate
paragraph below.
The phase sequence of the power circuit load termi-
nals (left-to-right: T1, T2, T3) in units mounted on
the rear side of the MCC is opposite to that of the
load terminals in units mounted on the front side of
a back-to-back MCC. To obtain the same direction
of rotation for a motor connected to a rear-mounted
unit as for one connected to a front-mounted unit,
relabel the terminals in the rear-mounted unit: T3,
T2, Tl, and wire accordingly. Refer to the warning
sticker supplied with rear-side units.
When making connections to the load terminals be sure
to leave sufficient slack in the wires so that the unit can
be withdrawn to the detent position for maintenance. See
page 20.
NEMA TYPE B WIRING
Each control unit is factory assembled with devices
interwired within the unit. In addition, all control wiring is
carried to unit terminal blocks mounted on the right-hand
side of the unit. See Figure 15. Bring the field wiring of
control wires from a horizontal wireway into the vertical
wireway on the right-hand side of the applicable control
unit and terminate them at the unit terminal blocks. Bring
load wiring from the vertical wireway, under the bottom
right-hand side of the unit, to terminations within the unit.
See below.
ENGAGING PULL-APART TERMINAL BLOCKS
The male portion of the pull-apart terminal block is lo-
cated in a plastic bag tied to the pivot rod inside the unit.
This terminal block can be wired outside of the vertical
wireway. To engage the terminal block, align the fingers
of the male connector with the slot at the back of the
female portion of the terminal block. Then rotate the
male portion forward and to the left into the female por-
tion of the terminal block.
Each male portion of the pull-apart terminal block has
two cavities adjacent to the. center terminal screw to
PART 4
INSTALLING CONDUIT AND WIRING
Содержание Freedom 2100
Страница 26: ...Page 26 I B 8926 1...
Страница 32: ...Page 32 I B 8926 1 Part 11 PLAN VIEWS...
Страница 33: ...Page 33 I B 8926 1...