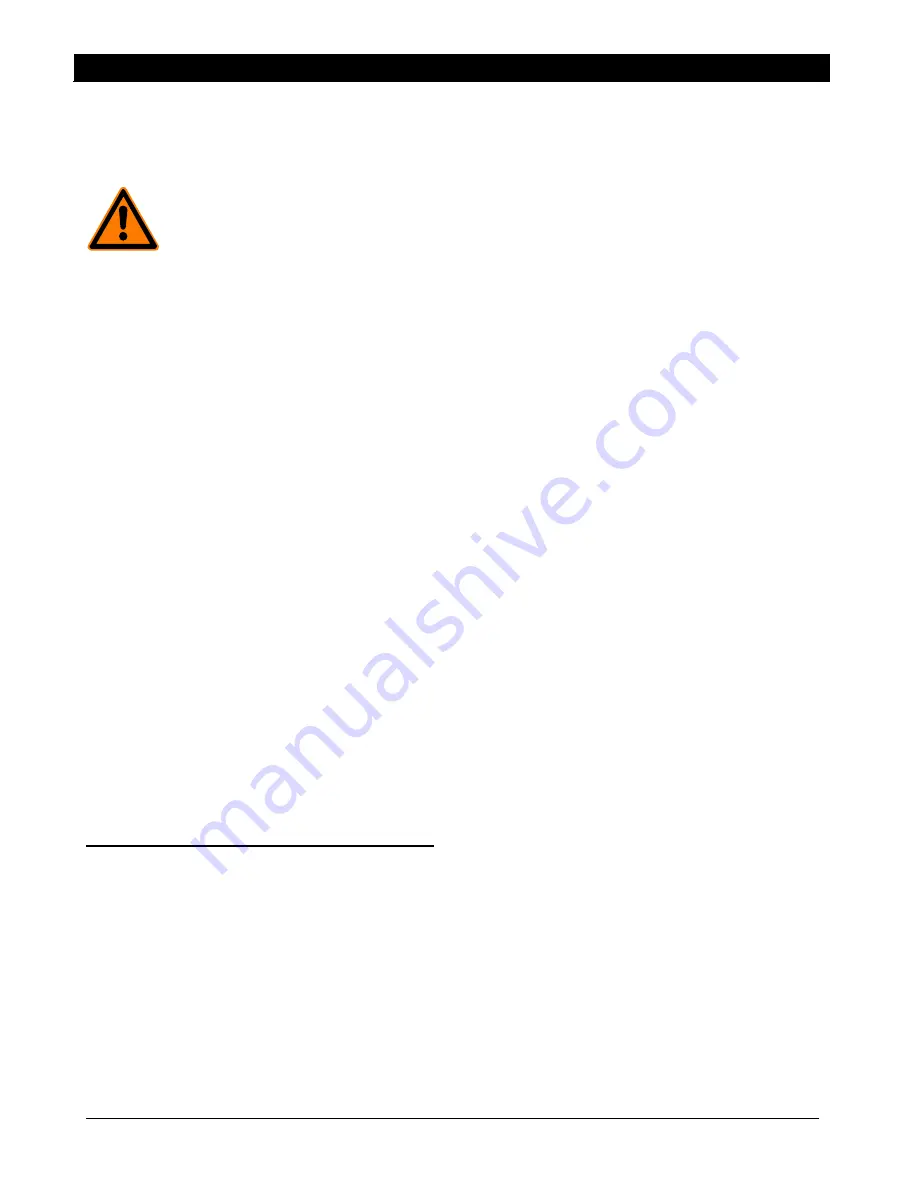
DCF-3000 Installation, Operation & Maintenance
DOM0000007, Revision A
`
Page 6 of 7
Maintenance
To service the DCF-3000 filter unit, isolate it from the process air and
electrical supply using proper lockout/tagout plant procedures.
Depressurize and de-energize all sources of power. Utilize proper
application of PPE for the process conditions.
WARNING:
Equipment should be shut down and
isolated from energy sources and other equipment
before any inspection or servicing to prevent risk of
shock or process fluid leakage.
FAILURE TO FOLLOW THIS WARNING MAY LEAD TO DEATH,
SEVERE INJURY OR PROPERTY DAMAGE.
Maintenance Schedule
Frequency of inspection is at the discretion of the customer and may
need to be increased or decreased accordingly. The wear of certain
items depends on how often the filter is used and the abrasiveness of
the product being filtered.
Weekly
Inspection for leakage around the actuator shaft seal.
To eliminate weeping, tighten that packing as necessary by
tuning star wheel (Figure 1, item 6 or 13) clockwise. If the
packing (Figure 1, item 7 or 15), has reach maximum
adjustment and or leaking persists after adjustment disassemble
the unit and replace the packing.
Monthly
Inspect the cleaning discs for excessive wear. Remove the
cleaning discs and inspect.
Remove the actuator lid assembly and inspect the inside of the
filter element. Inspect the inside of the filter element for
excessive wear. The lid seal (Figure 1, item 11) should be
replaced to maintain a proper seal. If the element is removed
from the housing, the seals (Figure 2, item 7) should be
replaced to maintain a proper seal. Over time, gaskets will take
on a permanent “set”.
Inspect the actuator assembly. When the actuator begins to fail,
the differential pressure will rise. This occurs because the
actuator cannot sufficiently drive the cleaning disc assembly.
Remove the actuator assembly and check for air leakage
around the gland seal. Check for any side to side movement in
the actuator shaft. If either of these problems exist, the actuator
can be rebuilt (Figure 2, item 2) Inspect the actuator shaft for
damage or excessive wear. If damage exists to the shaft, the
actuator shaft must be replaced.
Troubleshooting
Symptoms
A
Actuator doesn’t operate properly
B
Purge valve will not operate properly
C
Leakage at lid seal
D
Reduction in flow rate or high differential pressure
E
Drop in filtrate quality
Possible Faults
A
Actuator doesn’t operate properly
1
No power
a
Check safety switch position.
b
Check to see if the filter system is receiving adequate
power.
c
Check to see if the filter system is set to the proper
voltage.
d
Check all wiring connections.
2
No air supply
a
Check to see if the filter system is receiving adequate
air.
b
Check for air leaks.
c
If included check to see if the air bleed valve is
closed and the air block valve is open.
d
Check to see if the airlines are connected to the
correct ports.
3
Actuator seals have worn out
a
Check the air filter and water separator for operation.
b
Replace the actuator
4
Actuator installed improperly
a
Confirm the element hold-down plates are properly
installed and are securing the actuator.
5
Faulty solenoid valve
a
Check to see whether the manual override button on
the solenoid valve actuates the cylinder.
6
Actuator cleaning disc carrier is seized.
a
Inspect and clean actuator assembly of built-up
solids.
7
Cleaning disc not cleaning the filter screen
a
Inspect and clean the filter screen.
b
Inspect and replace the cleaning disc.
B
Purge valve will not operate properly
1
No power
a
Check to see if the filter system is receiving adequate
power.
b
Check to see if the filter system is set to the proper
voltage.
c
Check all wiring connections.
2
No air
a
Check to see if the filter system is receiving adequate
air.
b
Check for air leaks.
c
Check to see if the air bleed valve is closed and the
air block valve is open.
d
Check to see if the airlines are connected to the
correct ports.
3
Damaged rotary Actuator seals
a
Order a factory repair kit and replace the seals.
4
Faulty solenoid valve
a
Check to see whether the manual override button on
the solenoid valve actuates the cylinder
5
Damaged purge valve
a
Replace or rebuild purge valve
6
Debris caught in purge valve
a
Remove debris from purge valve
C
Leakage at lid seal
1
Loose lid nuts/bolts
a
Tighten lid/nut bolts.
2
Dirty lid sealing surfaces
a
Clean lid sealing surfaces
3
Damaged sealing surfaces
a
Repair or replace filter station
4
Damaged lid O-ring
a
Remove and replace with factory lid O-ring