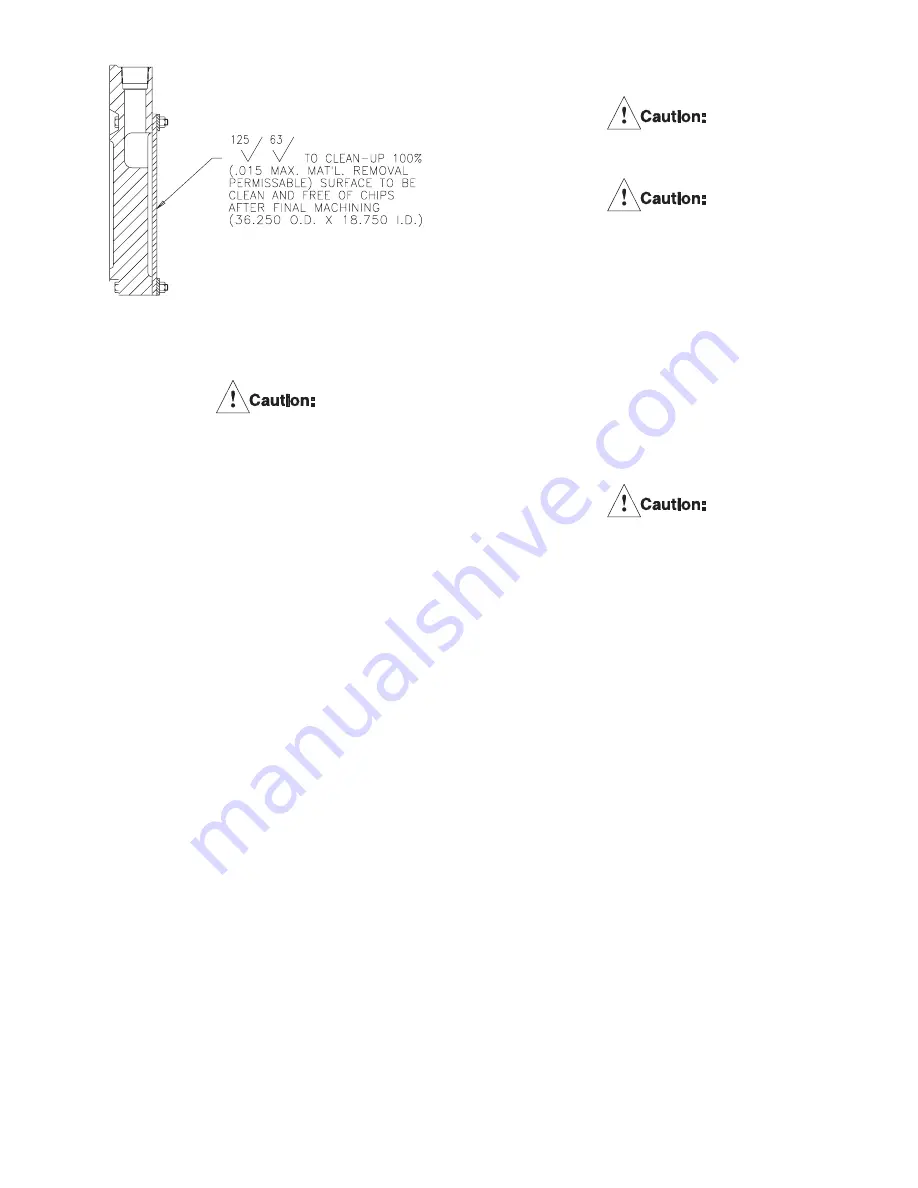
WCB 11060 (PDF Format)
19
© Copyright Eaton Corp., 1998. All rights reserved
June, 1998
NOTE: New wear plates (3), on 36 WCBs,
require machining after they are installed.
See figure 13 for machining specifications.
Failure to machine wear plate face
could result in a reduction of torque.
4.5.10
Re-assemble per section 4.8.
4.6
Cylinder Seal Replacement
Note: Item numbers (#) are shown on
Figures 1- 5.
4.6.1
See the Section 7.0 for the appropriate seals
for each WCB tensioner.
4.6.2
Disconnect the air connections.
4.6.3
While supporting the cylinder, loosen the
locknuts (18) ONE TURN AT TIME and in
an alternating (crosswise) pattern until the
spring force is completely relieved. Remove
the locknuts and washers (17). Remove any
wear spacers stored under locknuts. Mark
all of the water outlet ports for identification.
Deep well sockets are required. See table
10 for size and depth of socket required.
4.6.4
Using lifting equipment, carefully remove
the cylinder (19) and piston (33) as an
assembly. Set aside in a clean area.
Note: If a stud (6) should happen to come
loose, remove it completely, clean the
threads on the stud and the threads in
the mounting flange. Apply Locquic
®
Primer Grade “T” to the stud threads. After
the threads have dried, assemble to the
mounting flange using Loctite
®
#262. The
end of the stud must not extend past the
mounting surface of the mounting flange.
Loctite
®
#262 must be shaken prior
to application.
Loctite
®
#262 may irritate sensitive
skin. Refer to the product label for
proper safety precautions.
4.6.5
Place the cylinder and piston assembly with
the piston facing down on blocks approxi-
mately 6" (150 mm) high. The blocks must
only contact the cylinder (19) so that the
piston (33) will be free to move out of the
cylinder bore.
4.6.6
If a regulated air line is available, the piston
can be partially ejected from the cylinder by
applying no more than 15 PSIG (1.0 bar) to
the cylinder.
Application of a higher pressure
may cause damage to the
components.
4.6.7
To complete the removal of the piston from
the cylinder, open all air inlets. Alternately
insert a 0.50" (12 mm) diameter by 6" (150
mm) long wood dowel into each air inlet and
gently tap the piston with a mallet so that it
moves evenly out of the cylinder. Be careful
not to damage the sealing surfaces of the
piston or cylinder by cocking the piston in the
cylinder.
4.6.8
Inspect the cylinder sealing surface
condition for nicks or scratches or any other
defect which may prevent the seals from
being effective. Replace the cylinder,
if necessary.
4.6.9
Noting how the lips of the seals are oriented
in the piston grooves, remove the seals.
4.6.10
Thoroughly clean the seal grooves in the
piston and apply a thin, even coat of Parker
“O” Lube
®
to the seal grooves, the seals, the
sealing surfaces of the cylinder and to the
chamfer on the piston.
Figure 13