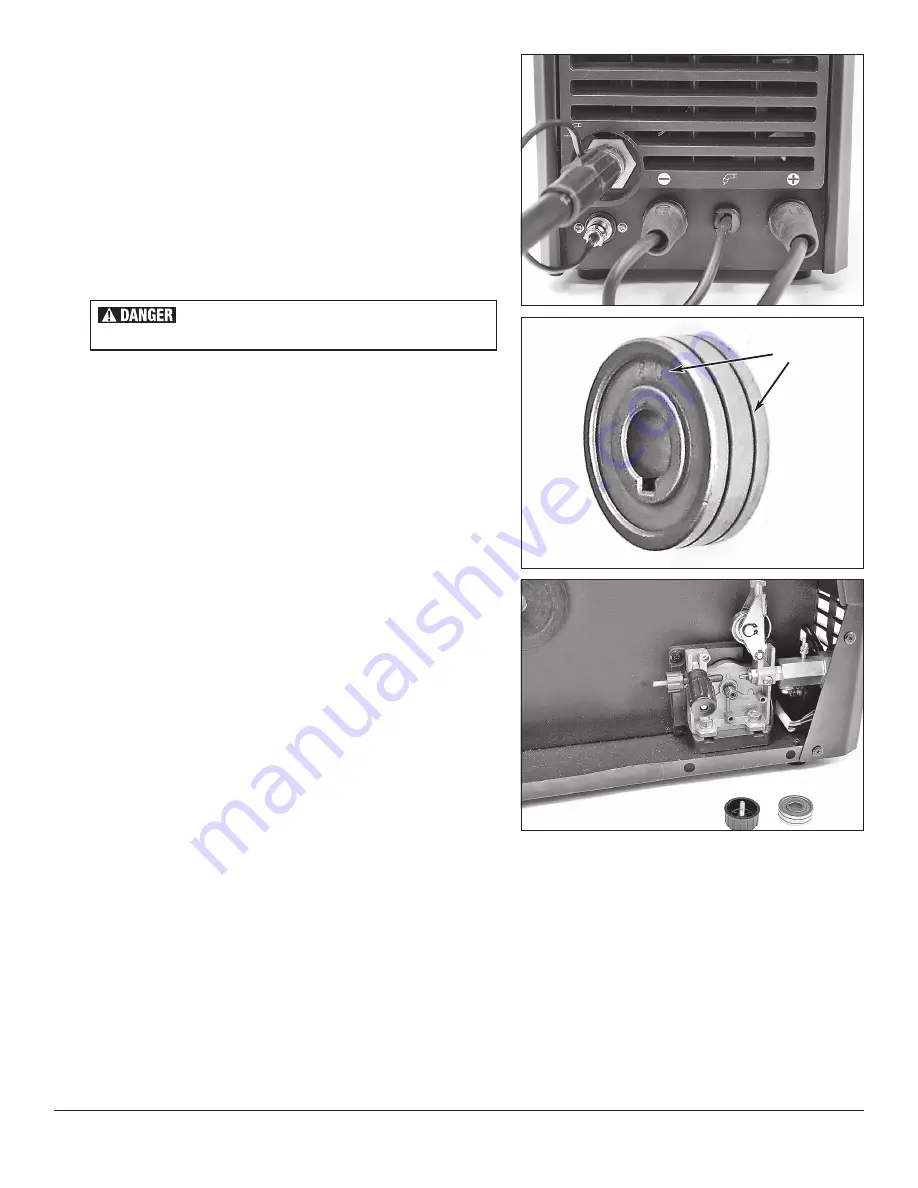
14
Eastwood Technical Assistance: 800.343.9353 >> [email protected]
SET-UP FOR FLUX CORE WELDING
The Eastwood MIG 180 comes factory set-up to weld with Solid Wire and Shielding Gas.
Flux Core does not require shielding gas.
Three changes to the Set-Up need to be made to MIG Weld with Flux Core wire:
- Reverse polarity from DCEP to DCEN.
- Install Flux Core wire.
- Position Drive Roller to accept Flux Core wire.
CHANGING THE POLARITY TO DCEN FOR WELDING WITH FLUX CORE WIRE
To use a Flux Cored wire, the Polarity of the short Integral Ground Connection Lead
[d]
attached to the Front Panel must be reversed
(FIG 14)
.
• Disconnect the Short, Integral Ground Connection Lead
[d]
from the Positive (+)
Connection Receptacle
[e]
by rotating the Rubber Insulator 1/2 turn Counter-
Clockwise and pulling outward.
• Align the key of the brass ferrule with the notch of the receptacle at the 12:00
position, then insert the Lead
[d]
onto the Negative ( - ) Connection Receptacle
[c]
, seat fully and rotate 1/2 turn Clockwise to lock
(FIG 14)
.
• Insert and lock the Ground Clamp Cable into the (+) Positive Connection
Receptacle
[e]
(FIG 14)
.
POSITIONING DRIVE ROLLER FOR WIRE SIZE
The Eastwood MIG 180 Wire Drive Roller has twin grooves to accommodate both 0.023”
[6mm] and 0.030”/0.035” [0.8mm/0.9mm] wire.
The MIG 180 Drive Roller is factory set and up ready to use 0.030” (0.8mm) solid wire.
IMPORTANT NOTE:
In this position, the actual, 0.030”/ [0.8mm] groove is inboard, un-
der the wire while the 0.8 marking for the 0.030” [0.8mm] wire is visible on the outward
face of the Drive Roller.
To Clarify; The stamped marking on the side of the drive roller indicates the size of the
groove on the opposite side of the roller
(FIG 15)
.
Reverse the drive roller position according to the following procedure:
• Open the side door of the Welder to access the drive motor compartment.
• Push the Pressure Adjuster rearward, pivot it down and out of the way then pivot
the Tension Arm up away from the Drive Roller
(FIG 16)
.
• Loosen and remove the Drive Roller Retaining Knob
(FIG 16)
.
• Remove the Drive Roller and view the wire sizes stamped on each side of the
Roller.
• Install the Drive Roller in the orientation so that the chosen wire size stamping
is facing outward making sure shaft key aligns with the Drive Roller keyway
(FIG 15)
.
• Reinstall the Drive Roller Retaining Knob on the shaft.
• Replace the Tension Arm and re-latch the Pressure Adjuster.
FIG. 14
FIG. 14
FIG. 15
FIG. 15
FIG. 16
FIG. 16
ELECTRIC SHOCK CAN CAUSE INJURY OR DEATH!
Disconnect Welder from power supply before beginning.
B
B
cc
dd
ee
bb
Size
Size
✓
✓