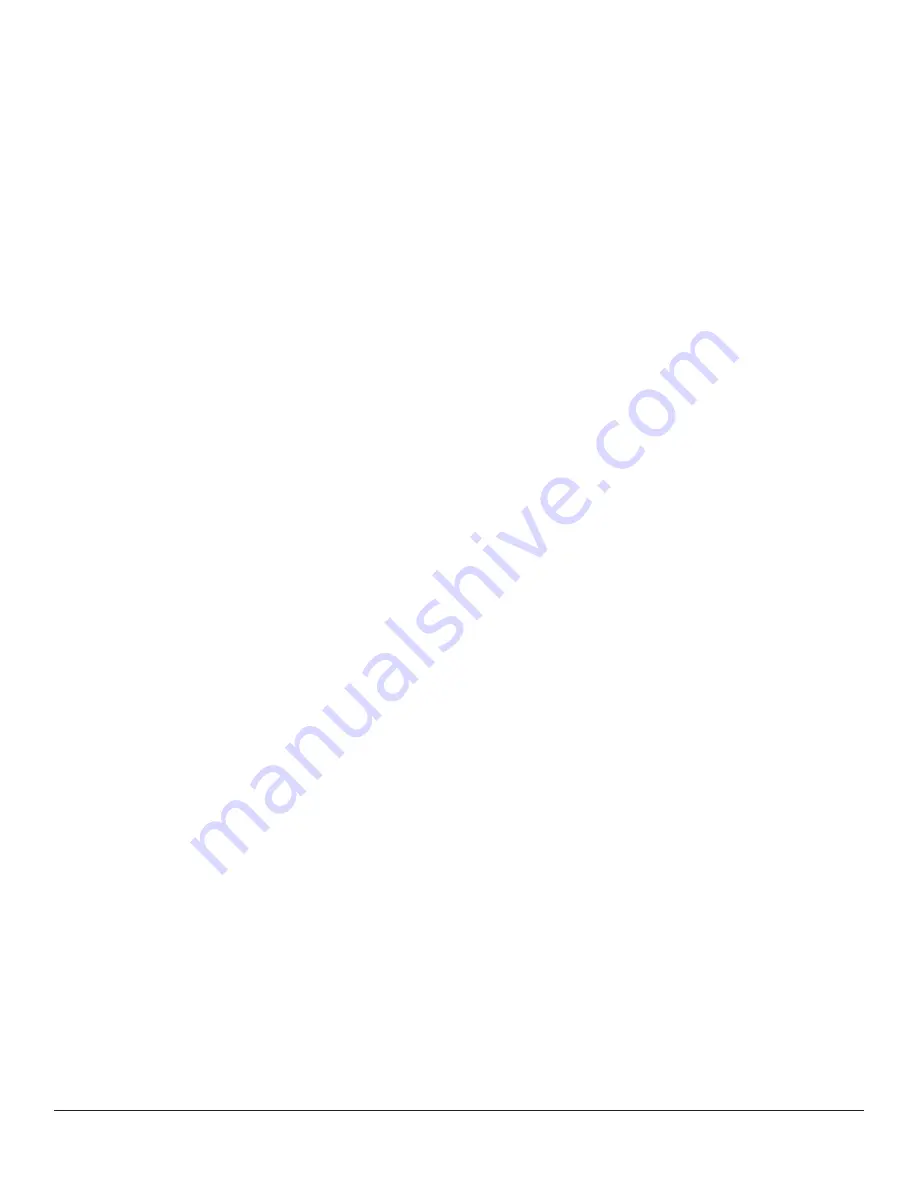
8
Eastwood Technical Assistance: 800.343.9353 >> [email protected]
BENDING BRAKE OPERATION
With all the Fingers in place, bends up to 90° can be made in 20 gauge mild steel panels up to 30” wide metal. To do so;
• Measure and mark the desired bend line on your sheetmetal panel.
• Raise the Fingers by rotating the Handle Upward.
• Slide panel under the Fingers lining up your pre-marked bend line with the lower, knife-edge of the Fingers.
• Rotate the Handle downward to clamp the Fingers against the Sheetmetal panel.
• Grasping the Handle once again, lift upward, bending your panel until the desired bend angle is achieved.
NOTE:
The use of an angle gauge or protractor (not included) is recommended to verify bend angle.
• Depending on the particular alloy being bent, it may be necessary to rotate the Handle slightly beyond the desired angle to allow for “springback”.
Some trial and error is suggested in scrap material before making final bends.
SLIP ROLLER
Adjustments
It is not possible to preset the Slip Roll to a pre-determined, measured radius so it will require some trial and error to achieve the correct radius.
NOTE:
It is important to remember that you can always pass the metal through the machine multiple times, increasing the radius with each pass.
Before making an actual piece for your project, work with some scrap pieces of the same size and thickness to practice on and to dial in the desired radius.
The more often you use the Slip Roll, the more familiar you will get with the adjustments required to make a specific radius.
Note that two of the three Rollers (Upper and Rear) are adjustable/moveable while The Lower Roller is the driving roller and is fixed in place.
• Adjust Rollers to Parallel – Turn the Thickness Adjustment Screws
(R) (FIG 1)
up or down as required, to be sure that the Upper and Lower Rollers are
parallel. The use of calipers to check the gap side to side between the Rollers is strongly recommended.
• Adjust for thickness – Slip a piece of metal, the same thickness as your planned project piece, between the Upper and Lower Rollers.
NOTE:
Once the Rollers are set parallel to one another, turn both Thickness Adjustment Screws an equal amount when adjusting for metal
thickness to maintain parallelism. Turn the Screws downward until some light pressure is being exerted on the metal.
• Adjust for Metal Radius – Adjusting the Rear Roller Knobs
(S) (FIG 4)
sets the radius of the piece. The more this Roller is raised, the smaller the radius of
the part will be. Be sure to adjust the Knobs equally on both sides to avoid creating a conical shape.
ROLLING OPERATION
• With the piece of sheet metal you will be rolling inserted between the Top and Bottom front Rollers, gradually rotate the Hand Crank
(A)
(Clockwise as
viewed from the right side) to begin forming the metal into the rollers until the piece is directly above the Rear Roller. Make sure it is tracking evenly before
continuing and readjust if necessary.
• Rotate the Hand Crank (Clockwise as viewed from the right side) to form the piece. Continue rotating the hand crank until the entire piece exits the Rollers.
NOTE:
If a tighter radius is desired, the piece may be re-run through the Rollers with the Rear Roller raised as needed.