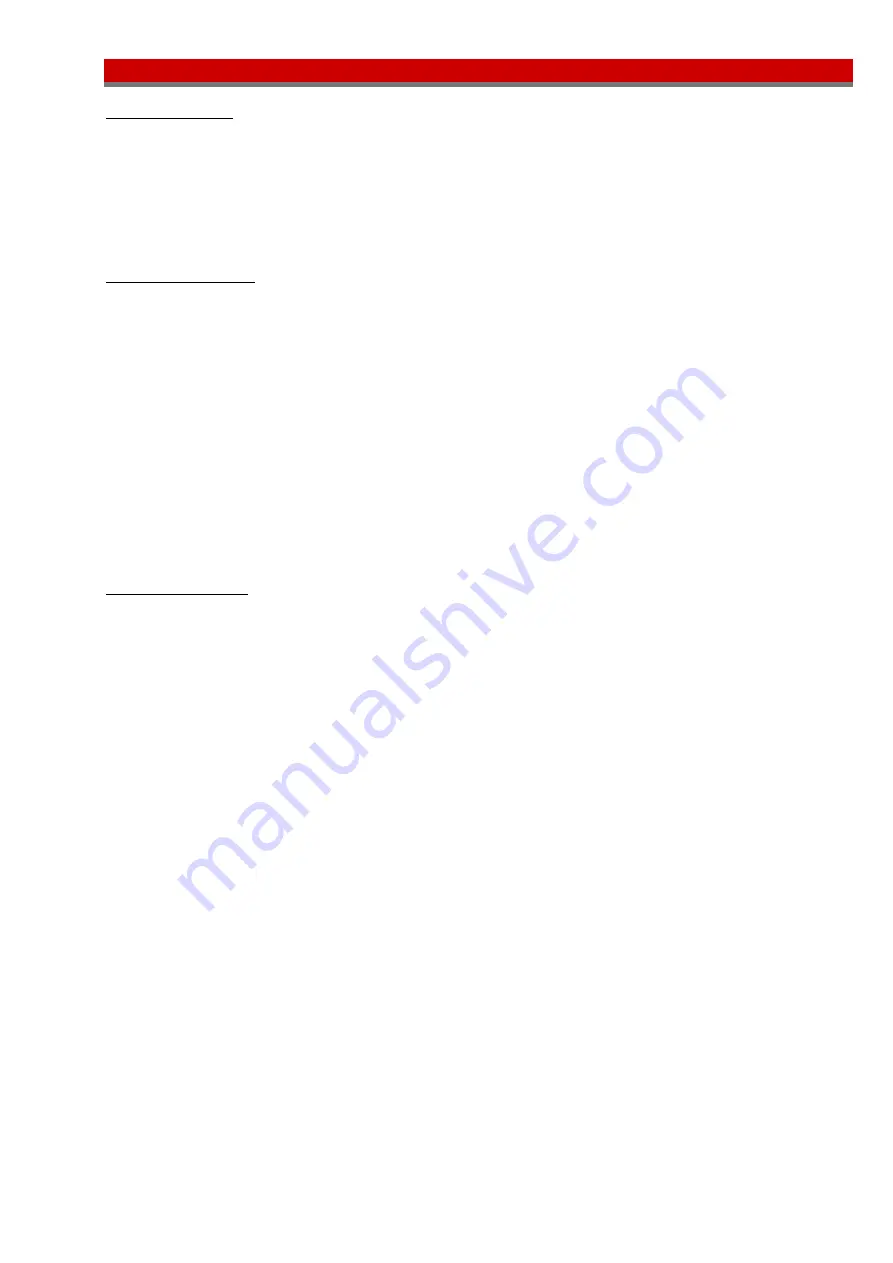
13
Maintenance instructions
Daily inspection:
1.
Ensure that the unit is free of chips and dirt that can cause disruption.
2.
Ensure that the unit is running smoothly and that it is not making any unusual sounds. In the event of
any abnormal noise, immediately stop the machine and cal for service staff to rectify the fault.
3.
Check that there is no external leakage on the hydrocheck. In the event of leakage, immediately call for
service staff to rectify the fault and then refill oil. See chapter ”Oil refilling of the Hydrocheck”.
Monthly inspection:
1.
Check the oil level in the hydrocheck using the green oil-level indicator, see Fig. 15. Pos 1.
At max. oil level, the indicator is completely visible, and when only 2 - 3 mm (.078 – .118 In) are
showing it is advisable to add oil. If the green indicator is inadvertently depressed, it can be reset by
manually pulling it out again. To grip the indicator pin, loosen the hexagonal protective sleeve. For
refilling of oil see chapter ”Oil refilling of the Hydrocheck”.
2.
Check the belt drive for wear and proper tension, see chapter ”Drive belt tension and Transmission
change out“.
3.
Check the locking of the settings:
- Adjustment screw for transition to working feed. (Applicable for pneumatic, electric and proximity
limit switches.)
- If linear transducer, sleds attachment to the adapter.
- Drilling depth and forward-reverse position.
- Positive stop.
- Working feed rate.
Annual inspection:
In addition to the daily and monthly inspections, the following points should be observed.
1.
Check the units pneumatic feed system for:
-
External
leakage.
- Leakage at the piston seal by performing the following. Advance the feed spindle to the positive stop
with out activating the signal for the forward-reverse position and check that there is no leakage of air
on the minus side.
Note!
Disconnect the hose to port 2, see Fig. 3 on page 6. Check correspondingly
for leakage at the piston seal when the feed spindle is in ”home postion”.
- Check that the feed spindle advances and retracts at an air pressure of 2 Bars (29 Psi). Without feed
control the feed spindle should advance and retract at 1 Bar (14.5 Psi).
In the event of leakage or if the feed spindle is sluggish, the feed system should be dismantled and
cleaned and all seals should be replaced.
Note!
When reassembling, lubricate bushings, seals, and the
cylinder barrel with a suitable grease.
2.
Check the hydrocheck for:
- Scratches or marks on the hydrocheck piston rod.
- Leakage at the piston by lowering the working feed rate to 0 and checking that the feed spindle
practically stands still.
- Advance and retraction of the hydrocheck at 2 Bars (29 Psi) pressure. See paragraph 1 above.
In the event of leakage or problems with any of the above mentioned points, the hydrocheck should be
dismantled and cleaned and all seals and damaged parts should be replaced. For refilling of oil see
chapter ”Oil refilling of the Hydrocheck”.
3.
Check the lubrication of the drive shafts splines by separating the belt housing from the mid-section.
Note that in certain cases the pulley on the drive shaft must be removed, see chapter ”Drive belt tension
and Transmission change out“. If necessary, lubricate the splines with a suitable grease.
Содержание BE 481
Страница 18: ...18 Spare parts drawing ...
Страница 23: ...23 Spare parts drawing ...