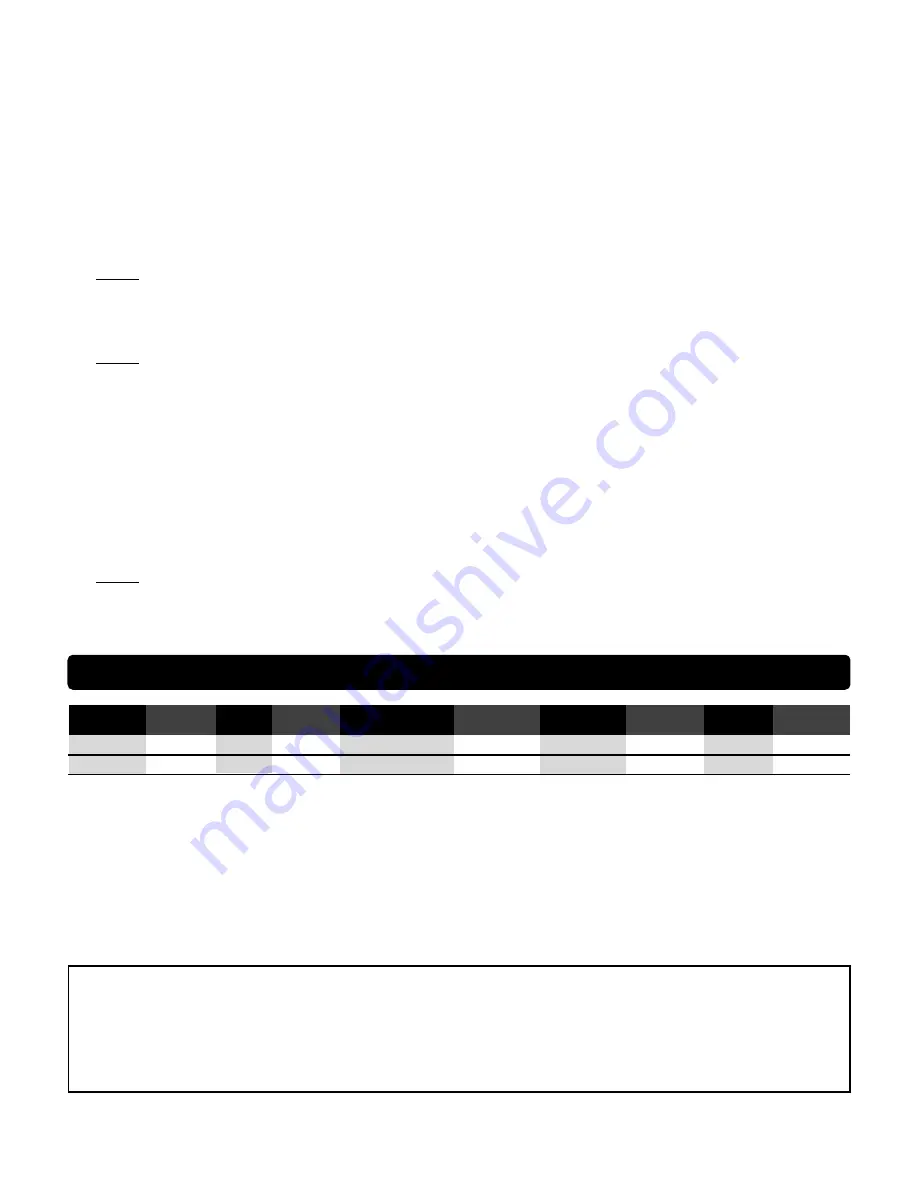
Maintenance Instructions
Important:
A preventative maintenance program is recommended whenever portable power tools are used.
•
Use only genuine Dynabrade replacement parts to insure quality. To order replacement parts, specify
Model#
,
Serial#
and
RPM
of your air tool.
•
It is strongly recommended that all Dynabrade rotary vane air tools be used with a Filter-Regulator-Lubricator to minimize the possibility of misuse due
to unclean air, wet air or insufficient lubrication. Dynabrade recommends the following:
11411
Air Filter-Regulator-Lubricator (FRL) – Provides accurate
air pressure regulation and two stage filtration of water contaminants. Operates 55 SCFM/1,558 LPM @ 90 PSIG with 1/2" NPT female ports.
•
Dynabrade recommends one drop of air lube per minute for each 20 SCFM (example: if the tool specification states 40 SCFM, set the drip rate on the
filter-lubricator to 2 drops per minute). Dynabrade Air Lube (P/N
95842
: 1 pt 473 ml) is recommended.
•
Grease the planetary gear assembly with the
95542
Grease by applying
2-3 plunges
with the
95541
Grease Gun after
every 50 hours
of use
for maximum gear life.
Routine Preventative Maintenance:
Check free speed of Extension Die Grinder using a tachometer. This governor controlled grinder should be speed
checked every 20 hours of use or weekly, whichever occurs more frequently.
•
DO NOT disassemble the governor for any reason. Reorder correct speed – governor assembly (See Assembly Breakdown) and recheck free speed of
tool with a tachometer.
•
Periodically remove collet insert and clean the inside diameter and slots from debris to keep accessories secure and reduce vibration.
•
Mineral spirits are recommended when cleaning the tool and parts. Do not clean tool or parts with any solvents or oils containing acids, esters,
ketones, chlorinated hydrocarbons or nitro carbons.
•
DO NOT clean or maintain tools with chemicals that have a low flash point (example: WD-40
®
).
•
A Motor Tune-Up Kit (P/N
96532
) is available which includes high wear and medium wear motor parts.
•
Air tool labels must be kept legible at all times, if not, reorder label(s) and replace. User is responsible for maintaining specification information i.e.:
Model #, S/N, and RPM. (See Assembly Breakdown)
•
Blow air supply hose out prior to initial use.
•
Visually inspect air hoses and fittings for frays, visible damage and signs of deterioration. Replace damaged or worn components.
•
Refer to Dynabrade's Warning/Safety Operating Instructions Tag (Reorder No.
95903
) for safety information.
After maintenance is performed on tool, add a few drops of Dynabrade Air Lube (P/N
95842
) to the air line and start the tool a few times to lubricate air motor.
Check for excessive tool vibration.
Handling and Storage:
•
Use of tool rests, hangers and/or balancers is recommended.
•
Protect tool inlet from debris (see Notice below).
•
DO NOT carry tool by air hose or near the tool throttle lever.
•
Protect abrasive accessories from exposure to water, solvents, high humidity, freezing temperature and extreme temperature changes.
•
Store accessories in protective racks or compartments to prevent damage.
Notice
All Dynabrade motors use the highest quality parts and metals available and are machined to exacting tolerances. The failure of quality pneumatic motors
can most often be traced to an unclean air supply or the lack of lubrication. Air pressure easily forces dirt or water contained in the air supply into motor
bearings causing early failure. It often scores the cylinder walls and the rotor blades resulting in limited efficiency and power. Our warranty obligation is
contingent upon proper use of our tools and cannot apply to equipment which has been subjected to misuse such as unclean air, wet air or a lack of
lubrication during the use of this tool.
One Year Warranty
Following the reasonable assumption that any inherent defect which might prevail in a product will become apparent to the user within one year from the
date of purchase, all equipment of our manufacture is warranted against defects in workmanship and materials under normal use and service. We shall
repair or replace at our factory, any equipment or part thereof which shall, within one year after delivery to the original purchaser, indicate upon our
examination to have been defective. Our obligation is contingent upon proper use of Dynabrade tools in accordance with factory recommendations,
instructions and safety practices. It shall not apply to equipment which has been subject to misuse, negligence, accident or tampering in any way so as to
affect its normal performance. Normally wearable parts such as bearings, contact wheels, rotor blades, etc., are not covered under this warranty.
Machine Specifications
3
Model
Motor
Motor
Sound
Air Flow Rate
Air Pressure
Spindle
Weight
Length
Height
Number
HP (W)
RPM
Level
CFM/SCFM (LPM)
PSIG (Bars)
Thread
Pound (kg)
Inch (mm)
Inch (mm)
52672
1 (745)
3,400
80 dB(A)
6/41 (1,160)
90 (6.2)
3/8"-24 male
4 (1.8)
16-7/8 (428)
1-7/8 (48)
52673
1 (745)
4,500
80 dB(A)
6/42 (1,189)
90 (6.2)
3/8"-24 male
4 (1.8)
16-7/8 (428)
1-7/8 (48)
Additional Specifications: Air Inlet Thread 3/8" NPT • Hose I.D. Size 3/8" or 10 mm • Air Flow Rate Based At Max HP. • Air Pressure 90 PSIG Max