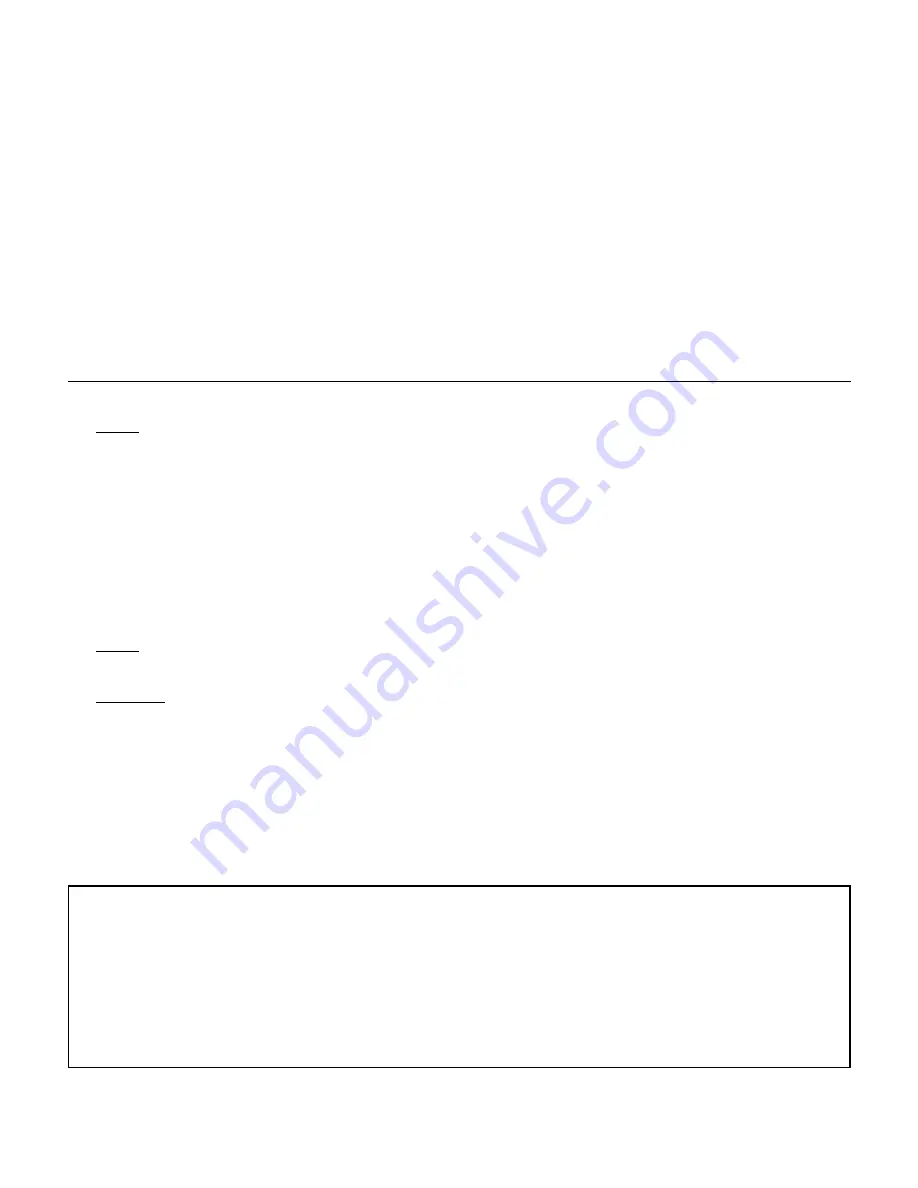
Maintenance Instructions
Important:
To keep tool safe a Preventative Maintenance Program is recommended whenever portable power tools are used. The program should include
inspection of air supply lines, air line pressure, proper lubrication and repair of tools. Refer to ANSI B186.1 for additional maintenance information.
•
Use only genuine Dynabrade replacement parts to insure quality. To order replacement parts, specify
Model#
,
Serial#
and
RPM
of your air tool.
•
All Dynabrade Rotary Vane air tools must be used with a Filter-Regulator-Lubricator to maintain all warranties. Dynabrade recommends the following:
10681
Air Filter-Regulator-Lubricator (FRL) – Provides accurate air pressure regulation and two stage filtration of water contaminants. Operates 55
SCFM/1,558 LPM @ 100 PSIG with 1/2" NPT female ports.
•
Dynabrade recommends one drop of air lube per minute for each 20 SCFM (example: if the tool specification states 40 SCFM, set the drip rate on the
filter-lubricator to 2 drops per minute). Dynabrade Air Lube (P/N
95842
: 1 pt 473 ml) is recommended.
Routine Preventative Maintenance:
•
Check free speed of tool regularly and after service using a tachometer without accessory mounted.
•
Make a simple check of vibration level after each service.
•
Periodically remove the collet insert and clean the inside diameter and slots from debris to keep accessories secure and reduce vibration.
•
Inspect collet regularly for nicks, cuts, sharp edges and runout. Replace damaged or worn inserts with genuine Dynabrade inserts.
•
Inspect shroud for wear or damage. Shrouds that are bent and severely worn or subject to a wheel breakage must be replaced.
•
Inspect diamond impregnated steel mounted wheel before mounting. Do not use mounted wheels that are damaged or warped.
•
Check diamond impregnated steel mounted wheel - speed rating. Rating of wheel must be greater than the tool speed marked on the housing.
•
If diamond impregnated steel mounted wheel damage occurs, investigate to determine the cause and correct before issuing tool for work.
•
Mineral spirits are recommended when cleaning the tool and parts. Do not clean tool or parts with any solvents or oils containing acids, esters,
ketones, chlorinated hydrocarbons or nitro carbons.
•
DO NOT clean or maintain tools with chemicals that have a low flash point (example: WD-40
®
).
•
A Motor Tune-Up Kit (P/N
96529
) is available which includes high wear and medium wear motor parts.
•
Air tool labels must be kept legible at all times, if not, reorder label(s) and replace. User is responsible for maintaining specification information i.e.:
Model #, S/N, and RPM. (See Assembly Breakdown)
•
Blow air supply hose out prior to initial use.
•
Visually inspect air hoses and fittings for frays, visible damage and signs of deterioration. Replace damaged or worn components.
•
Refer to Dynabrade's Warning/Safety Operating Instructions Tag (Reorder No.
95903
) for safety information.
After maintenance is performed on tool, add a few drops of Dynabrade Air Lube (P/N
95842
) to the air line and start the tool a few times to lubricate air motor.
Check for tool vibration before mounting abrasive wheel accessory.
Handling and Storage:
•
Use of tool rests and storage hangers are recommended.
•
Protect tool inlet from debris (see Notice below).
•
DO NOT carry tool by air hose or near the tool throttle lever.
•
Protect diamond impregnated steel mounted wheel from exposure to water, solvents, freezing temperature and extreme temperature changes.
– See Manufacturer's Instructions –
•
DO NOT USE diamond impregnated steel mounted wheels that have been dropped or show signs of warpage, cracks, nicks or other defects.
•
Store accessories in protective racks or compartments to prevent damage.
Notice
All Dynabrade motors use the highest quality parts and metals available and are machined to exacting tolerances. The failure of quality pneumatic motors
can most often be traced to an unclean air supply or the lack of lubrication. Air pressure easily forces dirt or water contained in the air supply into motor
bearings causing early failure. It often scores the cylinder walls and the rotor blades resulting in limited efficiency and power. Our warranty obligation is
contingent upon proper use of our tools and cannot apply to equipment which has been subjected to misuse such as unclean air, wet air or a lack of
lubrication during the use of this tool.
3
Lifetime Warranty
All Dynabrade portable pneumatic power tools are rigorously inspected and performance tested in our factory before shipping to our customers. If a Dynabrade
tool develops a performance problem and an inherent defect is found during normal use and service, Dynabrade will warrant this tool against defects in
workmanship and materials for the lifetime of the tool. Upon examination and review at our factory, Dynabrade shall confirm that the tool qualifies for warranty
status, and will repair or replace the tool at no charge to the customer. Normally wearable parts and products are NOT covered under this warranty. Uncovered
items include bearings, contact wheels, rotor blades, regulators, valve stems, levers, shrouds, guards, O-rings, seals, gaskets and other wearable parts.
Dynabrade’s warranty policy is contingent upon proper use of our tools in accordance with factory recommendations, instructions and safety practices. It shall not
apply to equipment that has been subjected to misuse, negligence, accident or tampering in any way so as to affect its normal performance. To activate lifetime
warranty, customer must register each tool at www.dynabrade.com. Dynabrade will not honor lifetime warranty on unregistered tools. A one-year warranty will be
honored on all unregistered portable pneumatic power tools. Lifetime warranty applies only to portable pneumatic tools manufactured by Dynabrade, Inc. in the
USA. Lifetime warranty applies only to the original tool owner; warranty is non-transferable.