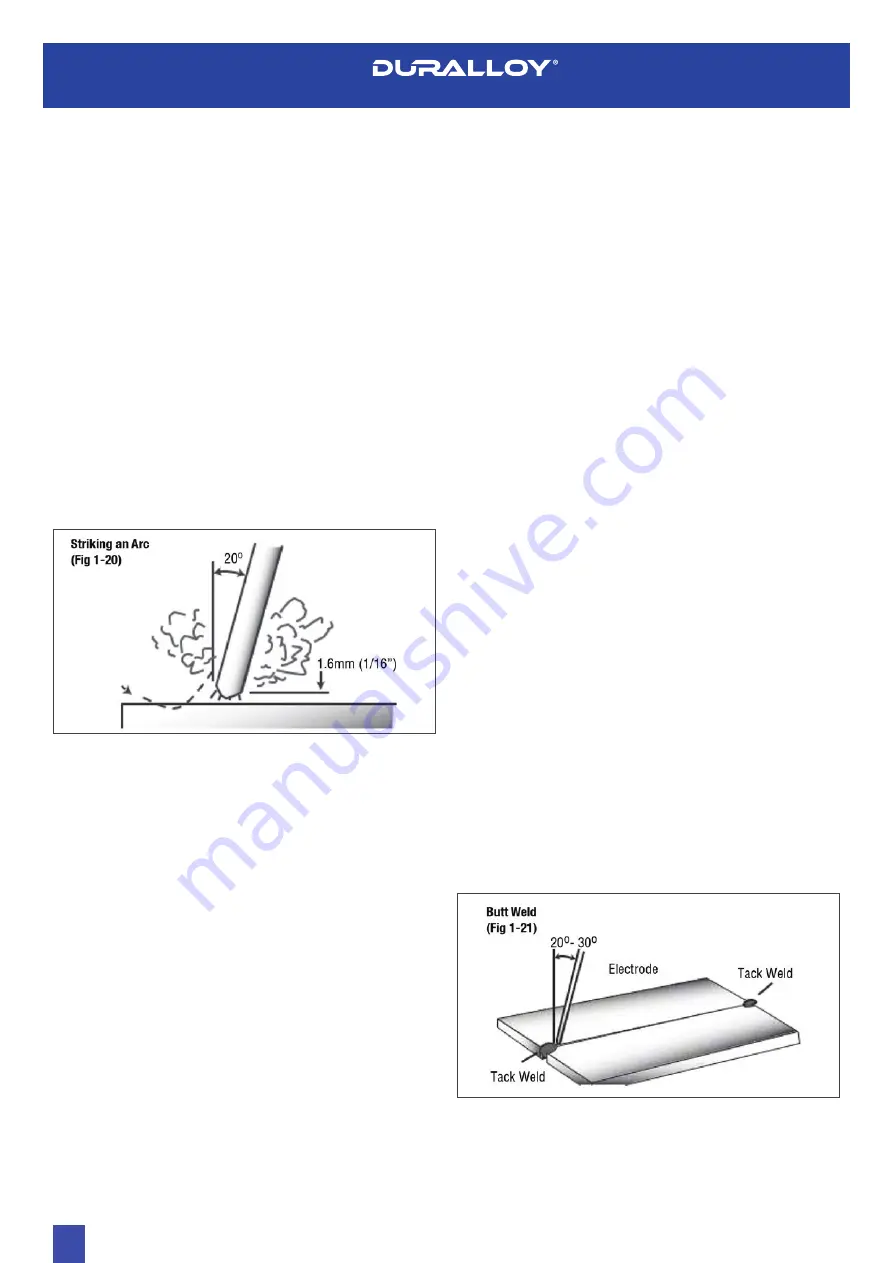
www.duralloy.net.au
|
1300 369 456
18
MULTIMIG 200 PFC MV
OWNER’S MANUAL
Striking the Arc
Practice this on a piece of scrap plate before going on to more
exacting work. You may at first experience difficulty due to the tip
of the electrode “sticking” to the work piece. This is caused by
making too heavy a contact with the work and failing to withdraw
the electrode quickly enough. A low amperage will accentuate
it. This freezing-on of the tip may be overcome by scratching the
electrode along the plate surface in the same way as a match
is struck. As soon as the arc is established, maintain a 1.6mm to
3.2mm gap between the burning electrode end and the parent
metal. Draw the electrode slowly along as it melts down.
Another difficulty you may meet is the tendency, after the arc is
struck, to withdraw the electrode so far that the arc is broken
again. A little practice will soon remedy both of these faults.
Arc Length
The securing of an arc length necessary to produce a neat weld
soon becomes almost automatic. You will find that a long arc
produces more heat.
A very long arc produces a crackling or spluttering noise and the
weld metal comes across in large, irregular blobs. The weld bead
is flattened and spatter increases. A short arc is essential if a high
quality weld is to be obtained although if it is too short there is the
danger of it being blanketed by slag and the electrode tip being
solidified in. If this should happen, give the electrode a quick
twist back over the weld to detach it. Contact or “touch-weld”
electrodes such as E7014 Stick electrodes do not stick in this way,
and make welding much easier.
Rate of Travel
After the arc is struck, your next concern is to maintain it, and this
requires moving the electrode tip towards the molten pool at the
same rate as it is melting away. At the same time, the electrode
has to move along the plate to form a bead.
The electrode is directed at the weld pool at about 20º from
the vertical. The rate of travel has to be adjusted so that a well-
formed bead is produced.
If the travel is too fast, the bead will be narrow and strung out and
may even be broken up into individual globules. If the travel is too
slow, the weld metal piles up and the bead will be too large.
Rate of Travel
Having attained some skill in the handling of an electrode, you
will be ready to go on to make up welded joints.
A. Butt Welds
Set up two plates with their edges parallel, as shown in Figure
1-21, allowing 1.6mm to 2.4mm gap between them and tack weld
at both ends. This is to prevent contraction stresses from the
cooling weld metal pulling the plates out of alignment.
Plates thicker than 6.0mm should have their mating edges
bevelled to form a 70º to 90º included angle. This allows full
penetration of the weld metal to the root. Using a 3.2mm E7014
Stick electrode at 100 amps, deposit a run of weld metal on the
bottom of the joint.
Do not weave the electrode, but maintain a steady rate of travel
along the joint sufficient to produce a well-formed bead. At first
you may notice a tendency for undercut to form, but keeping the
arc length short, the angle of the electrode at about 20º from
vertical, and the rate of travel not too fast, will help eliminate this.
Содержание MULTIMIG 200 PFC MV
Страница 1: ...MULTIMIG 200 PFC MV OWNER S MANUAL www duralloy net au 1300 369 456 ...
Страница 9: ...www duralloy net au 1300 369 456 WIRING DIAGRAM 9 MULTIMIG 200 PFC MV OWNER S MANUAL ...
Страница 21: ...www duralloy net au 1300 369 456 21 MULTIMIG 200 PFC MV OWNER S MANUAL MMA TROUBLESHOOTING ...
Страница 28: ...www duralloy net au 1300 369 456 ...