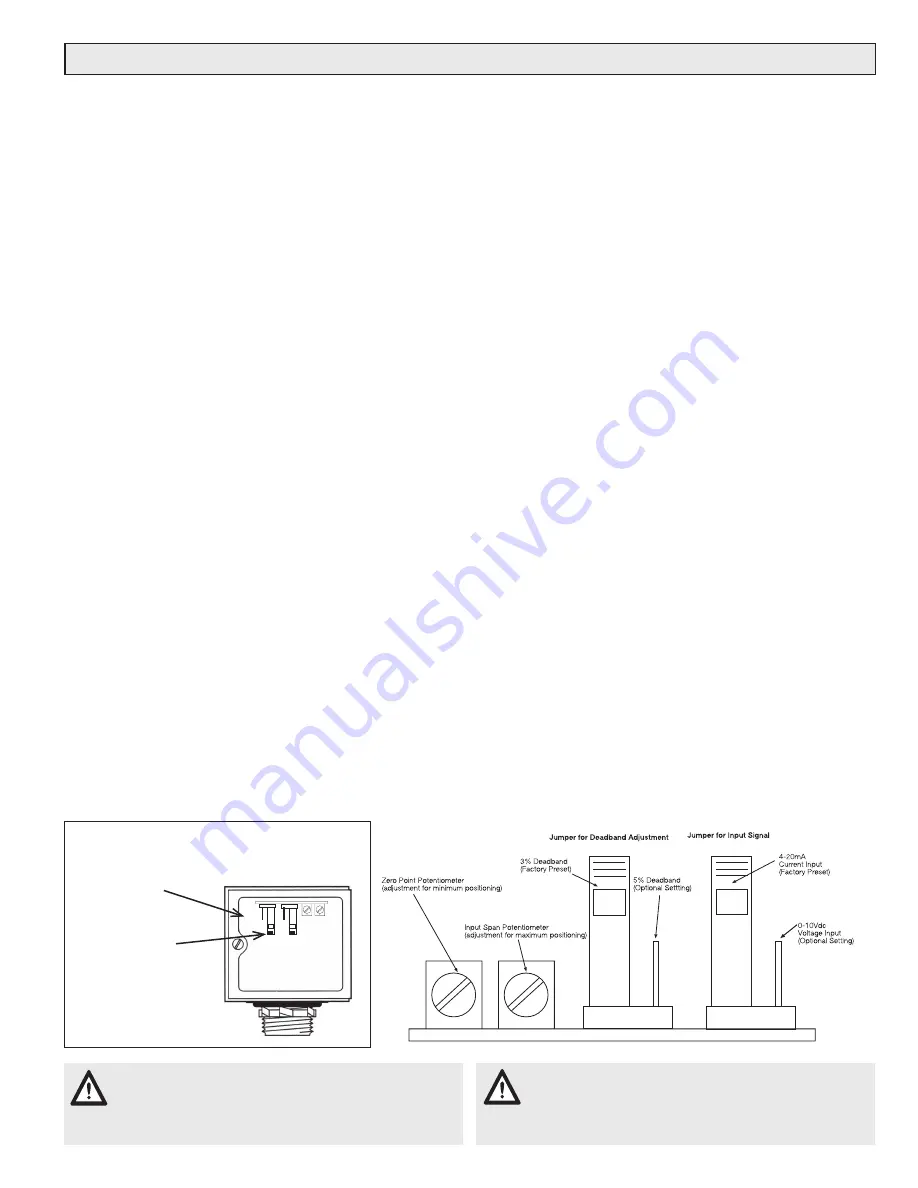
3 … 4
ADJUSTMENT
CAUTION: Do not apply a voltage source input to
CP-9302 actuator drive that is configured for current
input. Doing so may damage the drive.
CAUTION: Static charges produce voltages high
enough to damage the electronic components. Fol-
low static electricity precautions when servicing the
device(s).
Figure 2
If a CP-9302-702 requires adjustments to its startpoint, or input span, make adjustments according to the following:
CP-9302-702 Adjustment (Preparation)
From the factory, the actuator is calibrated such that it drives
to 90 degrees with 20mA applied and 0 degrees with 4mA
applies. To reduce the 90 degree position or increase 0
degree position, following the procedure below.
Initial Setup
1. Turn off all power and input signals to the actuaton.
2. Remove the metal cover. This allows access to the poten-
tiometers and the input/deadband jumpers.
3. Disconnect the drive’s yellow and blue leads from the
controller.
4. Connect the drive’s leads to the corresponding lead on
an instrument capable of producing 4-20mA +/- 0.1mA
(current calibrator).
Minimum Position Calibration
1. Apply power to the actuator, then turn on the “current
calibrator”.
2. Adjust the “current calibrator” until the mA input equals
the desired zero point current. This is typically 4mA.
NOTE:
The minimum position current input (zero point)
potentiometer and maximum position current input (span)
potentiometer can be physically turned indefinitely; but
they have an effective limit of 25 turns. Relative to the
start point (4 mA / 0 degrees), rotating the post CW
causes the actuator to drive toward 90 degrees. Con-
versely rotating the pots CCW causes the actuator to
drive back toward zero. This is true of both the START
POINT and SPAN adjustments.
NOTE:
There is a slight delay (approx. 3 seconds) in actua-
tor movement when a potentiometer is adjusted. Make
final adjustments slowly to prevent over adjusting. If
adjusted properly, when the unit just begins to drive, it
should stop within 5 degrees. Over adjusting will lower
the actual start point.
3. With the desired current input for the minimum position
applied (typically 4mA), adjust the zero point potentiometer
so the actuator shaft drives to it’s zero point (minimum po-
sition). It is best to adjust the start point potentiometer until
the actuator shaft just starts to move off its zero point.
Maximum Position Calibration
1. Apply power to the actuator, then turn on the “current
calibrator”.
2. Adjust the “current calibrator” until the mA input equals the
desired finish point (maximum position). This is typically
20mA.
3. With the desired current input for maximum position (typi-
cally 20mA), the actuator will drive towards 90 degrees.
Once the actuator stops, adjust the span potentiometer
so the actuator shaft drives to the maximum position. It
is best to adjust the span potentiometer until the actuator
shaft just moves to its finish point.
4 . Remove the current calibrator and turn off power to the
actuator. Then, reconnect the drive’s leads to the control-
ler.
5. Reinstall the cover.
6. Reapply power to the actuator and turn on the controller .
NOTE:
Occasionally, an adjustment to the input span setting
results in a change to the start point setting, due to a small
interaction between these two settings. After adjusting the
input span potentiometer, ensure that both settings meet
requirements by repeating steps 7 - 9.
NOTE:
When setting the potentiometers; only move the
actuator shaft in one direction. If the shaft is moved in the
opposite dirrection, the deadband will affect the setting.
Metal cover of
CP-9302-702
Location of pot.
adjustments and
jumpers under
metal cover
Top view of CP-9302-702
(the black box)
Potentiometer Adjustments and Jumpers