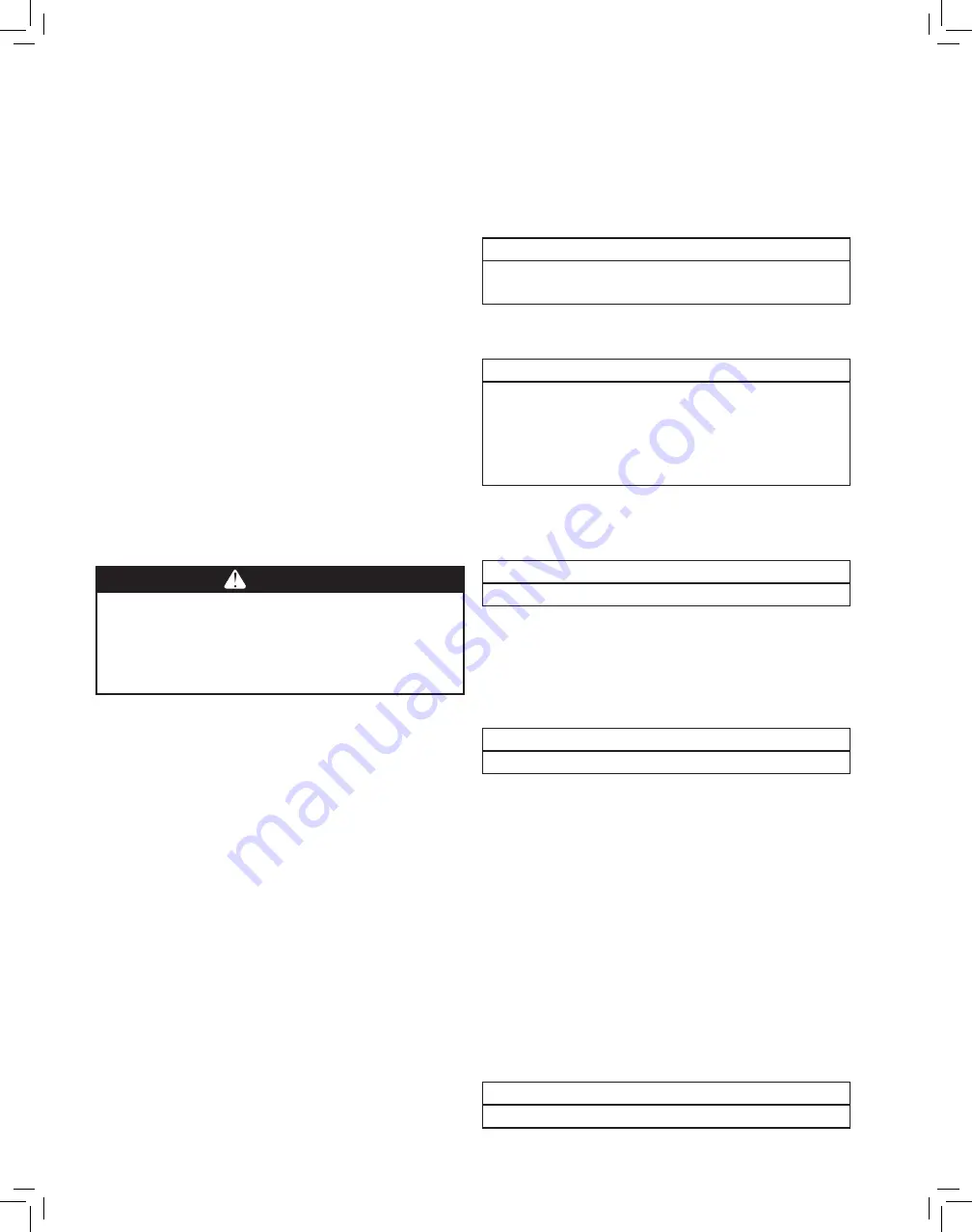
6
Section II
Maintenance
2-1. Lubrication
Unless otherwise specified, actuators are shipped packed
with grease which should be sufficient for one month
of normal operation. For normal operation, the actuator
should be lubricated once a month using Mobile XHP461
or XHP462 Extreme Pressure grease.
This grease has been thoroughly evaluated in Duff-
Norton actuators and has demonstrated superior
lubricating properties affecting both wear life and
maximum duty cycle.
Duff-Norton is not aware of an
equivalent grease. If this grease is not available in
your area please contact your local supplier for their
recommendations. Greases containing molybdenum
disulfide should not be used.
For severe service conditions, the actuators should
be lubricated more frequently using the above grease
(daily to weekly depending upon the conditions). If duty
is heavy, an automatic lubrication system is strongly
recommended.
CAUTION
Where lifting screws are not protected from airborne,
dirt, dust, etc., bellows boots should be used. Inspect
frequently at regular intervals to be certain that a
lubricating film is present. Lifting screws should never
be run dry.
2-2. Rebuild Procedure
Duff-Norton recommends the following procedures for
assembly and disassembly of actuators.
1. Tag critical parts to facilitate reassembly.
2. Mark mating surfaces to ensure proper meshing.
3. Clean and lubricate all parts as required.
4. All seals must be replaced when rebuilding.
5. All screws, washers and other small common parts
must be replaced if damaged in any way.
6. Replace damaged or frozen lubrication fittings with
new ones.
2-3 Required Tools
A bearing puller or press, and common hand tools are
necessary for proper assembly and disassembly.
2-4. Disassembly (Refer to Figure 3-1)
1. Remove lifting screw (5) from actuator.
2. Remove bottom pipe (4) from shell (3) (upright
models) or shell cap (2) (inverted models) or base
plate as applicable.
3. Loosen and remove set screws (1) in cap (2) and
remove cap from shell (3).
NOTE
It may be necessary to break shell cap or base plate
loose with a hammer.
4. Remove gear (6A) or worm gear and nut assembly
(6B) from shell (3).
NOTE
To facilitate removal of the gear from the shell on
models with 50- ton or higher load ratings, partially
reassembly the lifting screw into the worm gear (or
worm gear and nut assembly) and use a hoist or pulley
block to lift on the screw.
5. Remove top load bearing (7) which may be attached
to either shell cap (2) or worm gear (6A) or anti-
backlash nut.
NOTE
Use only a soft face hammer to tap bearings loose.
6. Remove bottom load bearing (8) which may be
attached to either the shell (3) base plate or worm
gear (6A).
7. Remove four cap screws (9) from each of the two
worm flanges (11) and remove flanges.
NOTE
Be careful not to lose flange shims (12).
8. Press oil seal (13) out of flange (11).
9. Remove worm (14) and worm bearings (15) from
shell (3) by striking one end of worm with a soft face
hammer.
10. Remove worm bearings (15) from worm (14) with
bearing puller or press. (Note: This step will not
be necessary if worm or worm bearings are not
damaged.
11. If actuator is keyed, remove screw in shell cap and
tap key out of keyway.
2-5. Cleaning
1. Use degreasing solvent to remove grease or oil from
all parts.
NOTE
Remove grease from unit and do not reuse old grease.