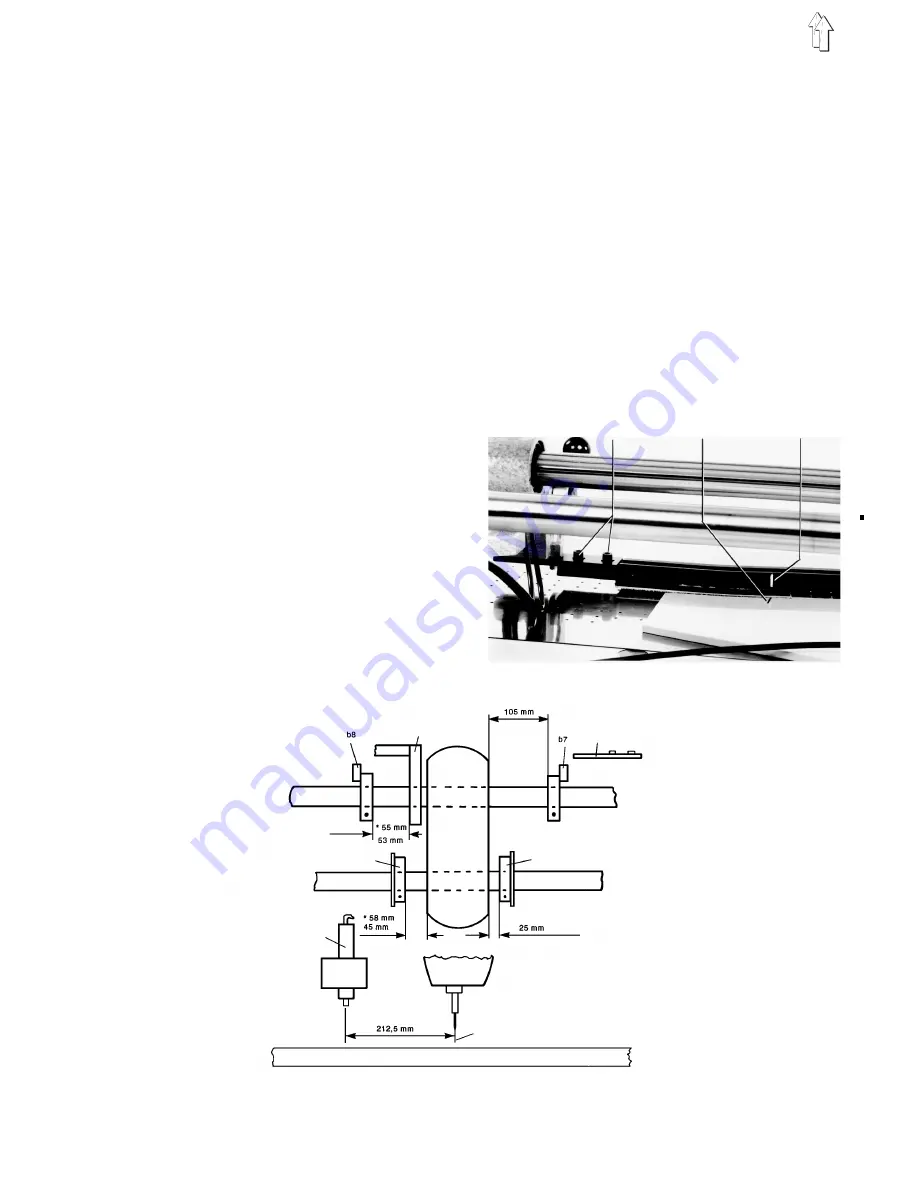
Fine Adjustment
–
Switch on main switch.
–
With the right diode lit and a longer tap of the
L<-W->R key, set the parameter to 0 with the
numeric keypad.
–
Conduct a reference run by pressing the
<-O-> key. The carriage travels to the left.
When reaching the switch b7 this is run past by
a bit. The step motor switches over and at first
runs at low speed to the reference point (b7)
and then runs with return speed to thr right end
position.
The distance between the middle of the
cylinder 4 and the middle of the needle should
then be 212.5 mm. The right end position is to
be precisely set by adjusting the bracket_6 and
repeated reference runs.
Note!
This is the initial carriage position which must be
exactly adhered to in order to be able to alternate
work with different material guide rails.
2.2 Left end position
Set the left position with the L<-W->R key. The left
diode lights up.
Conduct a refernce run with the <-O-> key. The
carriage stops in the left end position. This position
corresponds to the position of the switch b7 as
described in Section 2.1. It must not be altered.
In order to avoid a collision of the carriage by a
possible malfunction, the stopper 7 is to be set at a
distance of 25 mm from the cast part 8. See
illustration in Sec. 2.1 and the dimension sketch.
2.3 Marking on the material guide rail
and the material stopper
The marking 3 on the rail and the marking 2 on the
material stopper must lie exactly opposite each
other. They show the extreme sewing length range
1000 or 1250 mm, that is, the seam end.
The curved rail contour must correspond to that of
the material stopper.
After loosening the screws 1 located at the left and
right the rail can be aligned in its slots to the
contour of the material stopper.
The carriage end position set at switch b7 may not
be changed for this purpose.
1 2 3
bracket for the left end position 212.5 mm
Stopper for the left carriage end position
Mounting plate
Step motor
Needle
Cylinder for the rail
Stopper for the right carriage end position
Last
guide
under
the head
Table-top
* Measure by long transport carriage (Sewing length 1250 mm)
5
Содержание 744-122
Страница 7: ...11 10 1 2 88 mm 3 4 5 6 8 ...