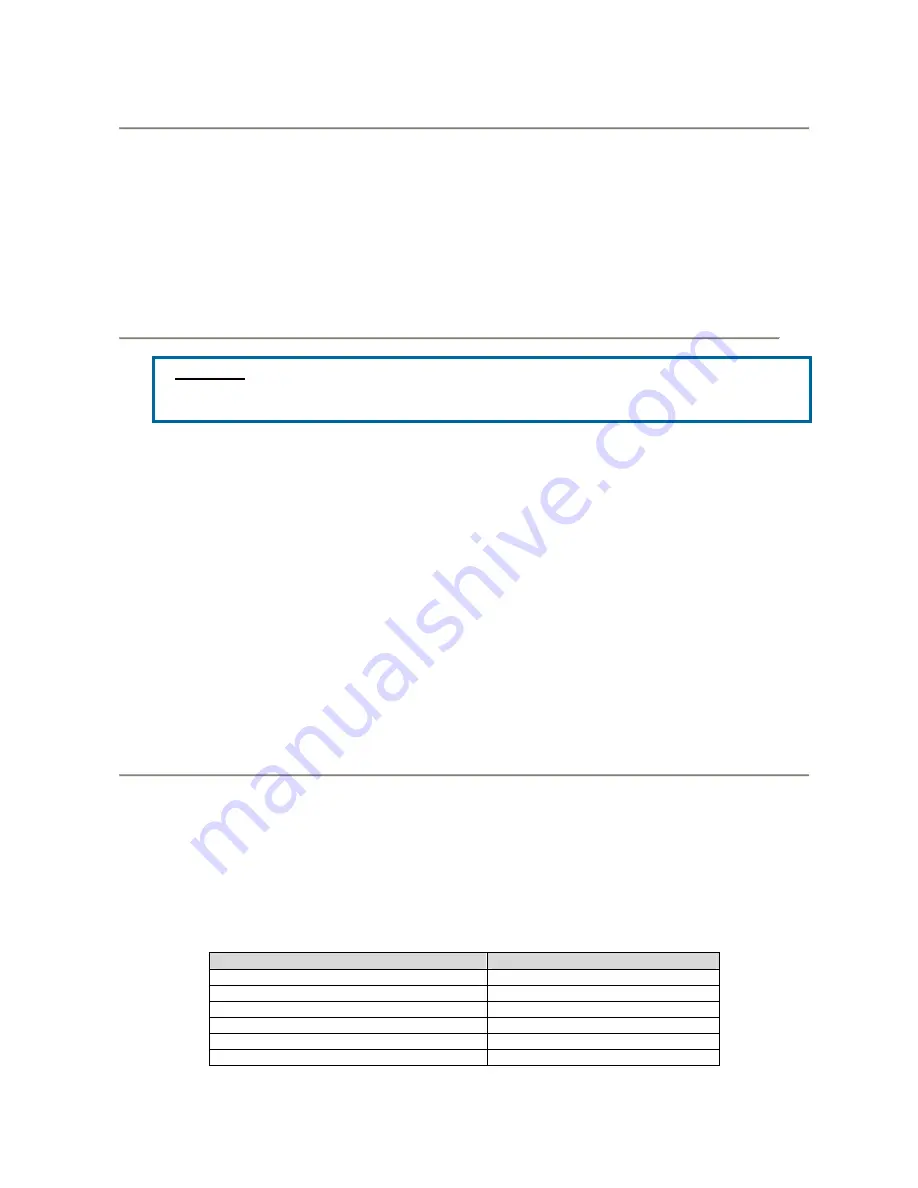
15
13. HANDLING AND TRANSPORTATION
Prior to shipping, the equipment is carefully packed in cardboard package. During transportation and storage,
always maintain the pump the right way up as indicated on the box. On receipt check that package has not
been damaged. Then, storage the machine in a dry location.
⇒
Due to machine contained weight and size, it is not necessary the use of material handling
equipment. Anyway, we recommend to lift the equipment observing the right way up shown on
the cardboard package.
14. OPERATING HAZARDS
Power supply
Any type of intervention must not be carried out before unplugging the machine from power supply. Make
sure that no one can start it up again during the intervention. All the installed electric and electronic equipment,
reservoirs and basic components must be grounded.
Flammability
The lubricant generally used in lubrication systems is not normally flammable. However, it is advised to avoid
contact with extremely hot substances or naked flames.
Pressure
Prior to any intervention, check the absence of residual pressure in any branch of the lubricant circuit as it may
cause oil sprays when disassembling components or fittings.
Noise
Pump does not produce excessive noise, less than 70 dB(A).
15. PRECAUTIONS
No particular operating hazards characterize the machine, except for the following precautions:
♦
Operator’s contact with the lubricant in case of piping breaking/opening or during
refill/maintenance. -> Protection against direct and indirect contact with the fluid must be provided
by the user:
the operator must be provided with suitable individual protective clothing and devices
(tit VIII – 626).
♦
Use of incompatible lubricant. Main unauthorized fluids:
⇓
Fluids
Dangers
Lubricants containing abrasive components
Premature wear of pump
Lubricants containing silicon
Pump failure
Petrol – solvents – inflammable liquids
Fire – explosion –seal damage
Corrosive products
Pump damage - danger to persons
Water Pump
oxidization
Food Products
Contamination of the product
WARNING: It is necessary to carefully read about the instructions and the risks involved in
the use of lubrication machines. The operator must know the machine
functioning through the User and Maintenance Manual.