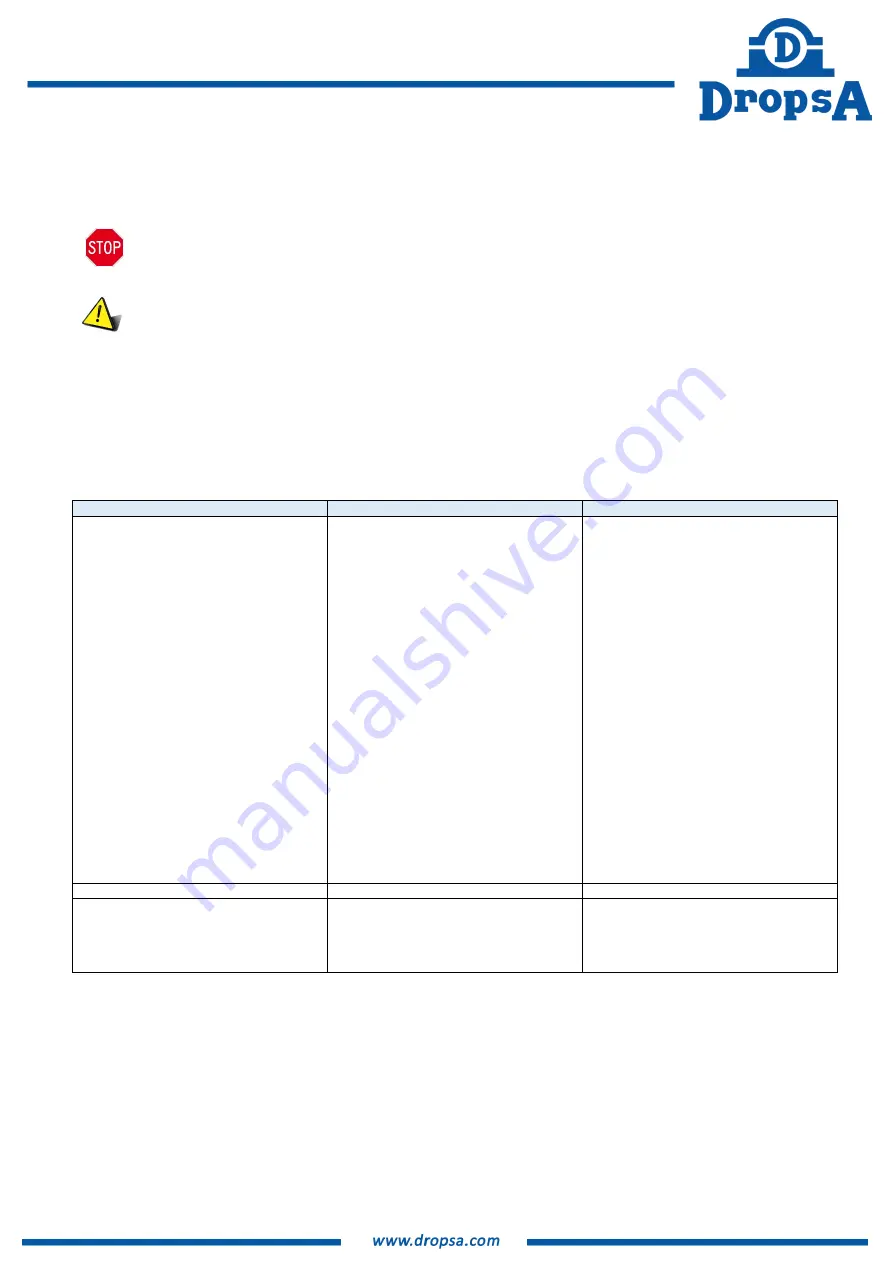
22
8. Troubleshooting
8.1 Problems, causes and solutions
ATTENTION
The machine can be opened and repaired only by authorised DropsA personnel.
DANGER
To carry out all the indicated operations, wear adequate personal protective equipment.
Below is a troubleshooting table highlighting the main failures, probable causes and possible
solutions. If, after having consulted the diagnostics table, you are unable to solve the problem, do not
search the failure by removing parts of the machine. Please contact the DropsA Technical Department
and report the detected failures, with a detailed description.
Fault
Cause
Solution
The electric pump does not dispense lubricant.
The electric motor does not work.
The reservoir is empty.
The pump does not engage. Causes of the pump
failing to engage:
• The motor turns in reverse (clockwise);
• The motor turns in the right direction, but the
stirring paddle does not turn;
• Air bubbles in the lubricant.
The pressure regulation valve (bypass) has been
calibrated to a value that is too low.
Dirt in the check valve.
Check the connection between the motor and
the electrical power supply.
Check the motor windings.
Check that the motor terminal strip connection
plates are positioned in accordance with the
power supply voltage.
Fill the reservoir.
Attention: if the reservoir has emptied without
the minimum level electrical signal being sent,
the minimum level contact must be checked.
Remove the reservoir cover and check to ensure
that the stirring paddle turns clockwise and
moves the lubricant; otherwise, invert two of
the three motor phases.
See above.
Disconnect the pump delivery pipe and bleed
the lubricant until eliminating air bubbles.
The pump does not pressurise.
Possible pumping element malfunction.
Replace the pumping element.
No minimum level signal when there is no
lubricant in the reservoir.
Incorrect minimum level adjustment.
Check for the correct operation of the level
probe as follows:
check for the correct adjustment of the laser
level.