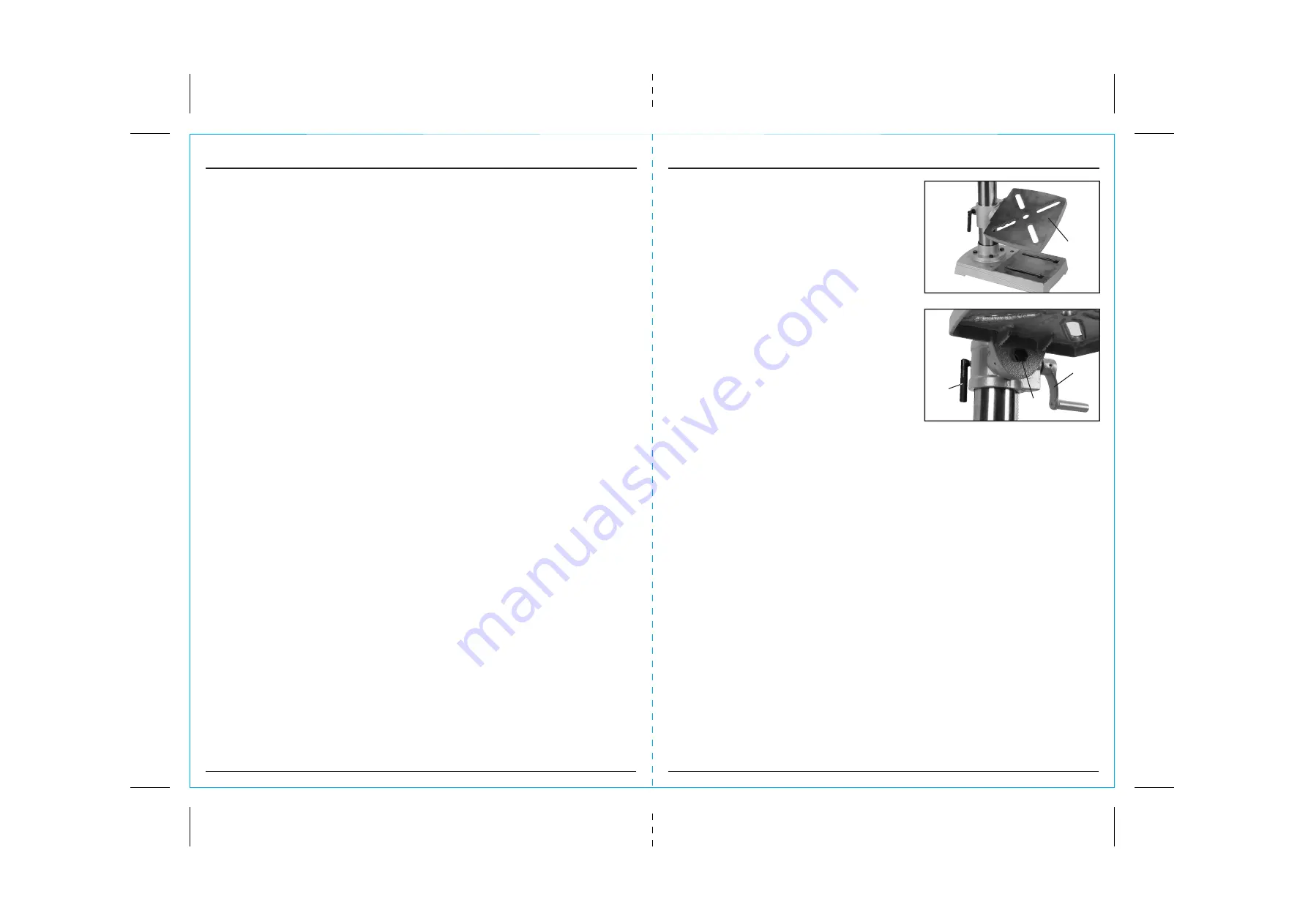
FIG.13
FIG.14
9. SETTING
THE
DRILL
5.2 ADDITIONAL SAFETY INSTRUCTIONS FOR DRILLS
MECHANICAL HAZARDS:
1.
Crushing.
When setting/changing a tool or maintaining the machine avoid crushing injuries
sustained between fixed and moving elements of the machine.
2.
Cutting or Severing.
At all times the workpiece shall be clamped as manual support will lead
to injury.
3.
Entanglement.
Switch off the machine for maintenance, workpiece loading/unloading, swarf/chip
removal, cutting/lubrication fluid application as contact with rotating spindle or tool will cause
entanglement and possibly lead to injury and entrapment.
4.
Impact.
Ensure the workpiece is securely clamped at all times to avoid sudden movement
(rotation) or ejection causing injury. Ensure any special tools associated with tool exchange, i.e.
chuck key are removed prior to attempting to start the machine.
5.
Stabbing, Cutting or Puncture Wounds.
Take care when handling the tools and avoid contact
with swarf and burrs created during drilling as they are extremely sharp.
ELECTRICAL HAZARDS:
1.
Contact with Live parts.
During commissioning, maintenance and trouble shooting operations
do not remove, open or expose any electrical, terminal and control boxes due to the danger of
electrocution. If the main cable is damaged, unplug the machine immediately and have the cable
replaced before continuing.
AUDIBLE HAZARDS:
1.
Hearing Loss.
Wear ear defenders during operation to avoid damage to hearing, however ensure
this does not interfere with speech communications or audible warnings.
MATERIAL HAZARDS:
1.
Contact and Inhalation.
Wear personal protective equipment to avoid contact from harmful
fluids, gases or dust thrown or created during the drilling process.
2.
Fire or Explosion.
Do not drill or drill in the vicinity of flammable or combustible materials.
LOCATION:
1.
Posture.
Ensure when mounting the machine that the chosen location does not lead to unhealthy
posture or repetitive strain during normal operation.
2.
Lighting.
Adequate lighting must be provided to ensure no operations are light impaired possibly
leading to injury.
3.
Reach.
Do not reach over or around the machine at any time.
UNEXPECTED START-UP:
1.
Remove the plug.
Remove the plug from the socket before carrying out adjustment, servicing
or maintenance.
ERRORS OF FITTING:
1.
Tools.
Ensure a suitable tool for the job in hand is securely and correctly fitted prior to starting the
machine. Guards shall be fitted and in place at all times.
STABILITY:
1.
Toppling.
The drill shall be securely bolted down to a suitable and level surface to prevent the
machine from overturning leading to injury.
2.
Slipping.
Ensure the area is clean of any residue cutting/lubrication fluid and other materials
which may lead to a slip, trip or other such hazard.
5. HEALTH AND SAFETY INFORMATION
- 8 -
- 17 -
9.4 WORK TABLE ADJUSTMENT -
FIGS. 13 - 14
For versatility, the work table
5
can be raised or
lowered, tilted ±45° or rotated 360° around the column.
To tilt the table, loosen the 18mm bolt
6
.
Adjust the table’s degree of tilt and re-secure with
locking bolt
6
. Use the scale as a guide.
Alternatively use a protractor off the table to the drill bit
for more accuracy.
To raise/lower the table working height, loosen locking
handle
7
and turn the height adjustment crank
handle
8
to raise or lower the table. Alternatively
while locking handle
7
is loose the table can be
rotated 180° to further increase the distance between
the chuck and workpiece. When the adjustments are
complete re-secure locking handle
7
.
The slots in the work table and base can
accommodate locking bolts to secure a small vice
enabling safe clamping of the workpiece.
CAUTION:
A drill bit snagging on a piece of work will
violently grab the piece of material, whipping it round
and is likely to result in personal injury. Always ensure
the workpiece is securely clamped.
5
7
8
6