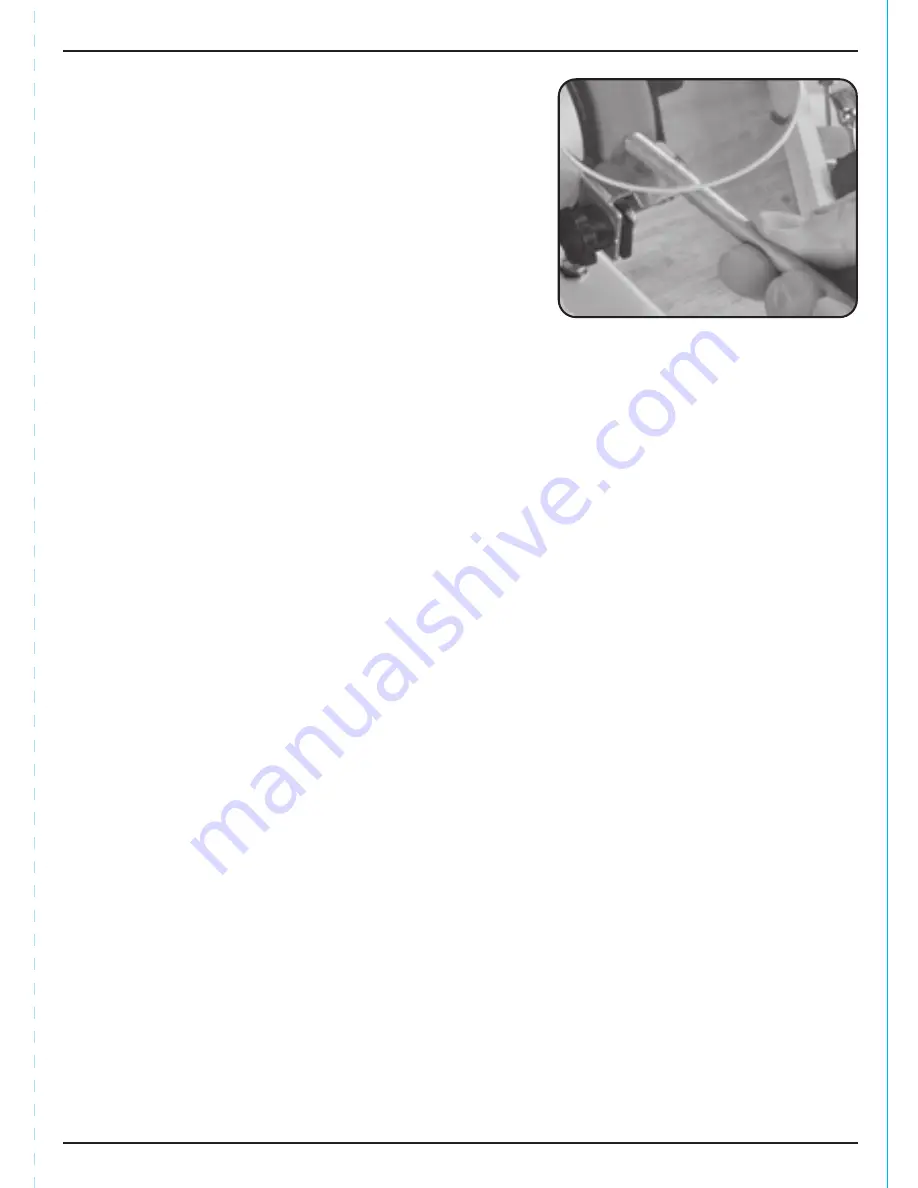
19
10.1 USING THE GRINDING WHEEL – FIG. 11
Warning!
Always wear appropriate personal protective
equipment, including eye, hearing and respiratory
protection, when using this machine.
Note:
Remove the plug from the socket before carrying
out adjustment, servicing or maintenance.
Warning!
Never fit any attachment with a rated
maximum speed that is lower than the ‘no load’ speed
of the grinder.
– If necessary, follow the instructions outlined in
section 9.4 on page 16 for attaching the grinding
wheel to the machine.
– Press the switch
at the side of the machine to turn on power to the machine.
Adjusting wheel speed
– The variable speed control dial also acts as an “on/off” switch (switching off when the dial
is turned to its furthest position anticlockwise).
– Turning the dial clockwise from the “off” position, the dial will initially click to “on”and
the machine will run at minimum speed – increasing incrementally turning clockwise, until
a maximum rotational speed of 10,000 rpm is reached with the dial at its furthest point.
Grinding
– Adjust tool rest to correct angle.
– Present the workpiece smoothly on to the grinding wheel face with a light and even
pressure without causing the wheel to slow.
– Best results are achieved if the grinder is allowed to rotate at its maximum speed. Excess
pressure from the workpiece can damage the wheel and overload the motor.
– Always hold the workpiece against the tool rest with both hands.
– Grind against the edge of the workpiece to avoid burrs.
– Never grind on the sides of the wheels.
– Never try to grind material that is too small to grip safely.
– When grinding metal, ensure that you are properly protected against the production of
sparks and that any flammable materials are stored away from the work area .
– During metal grinding operations, the workpiece can swiftly become hot. It is advisable to
quench the workpiece in a cold water bath to prevent heat damage. A finer graded
grinding wheel will generate less heat and may prevent heat damage.
– Check grinding wheels regularly for wear or damage. Replace wheels that are worn more
than 25%. Damaged wheels should be discarded immediately as they are dangerous and
can cause the grinder to vibrate.
– After grinding fine edge tools, they should be honed by hand on a fine slip stone.
10. OPERATION & USE
FIG.11