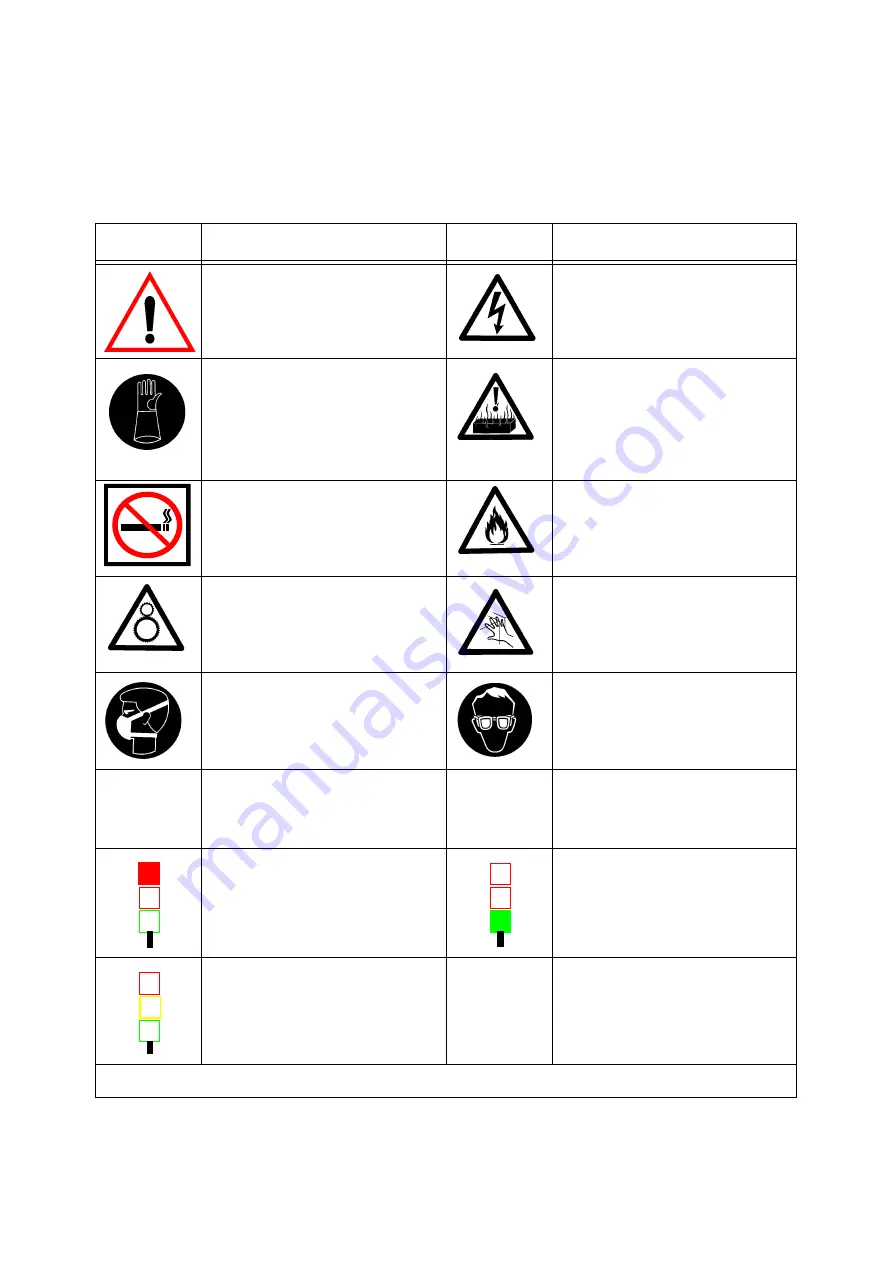
ICON
DESCRIPTION
ICON
DESCRIPTION
Only Qualified personnel is allowed to work on the
equipment.
Never eat, drink or smoke while working on the
machine.
Wash thoroughly before eating, drinking or smoking.
High voltages are present on various parts of the sys-
tem.
Before working on the electrical circuit, turn main
power off and block the mainswitch with a padlock.
Always wear heat resistant gloves and protective
clothing when working on the machine.
If possible allow the machine to cool down before
starting working on the machine.
When burned, immerse in cold water immediately.
When the burn is severe, consult a physician as soon
as possible.
Always wear heat resistant gloves and protective
clothing when working on the machine.
If possible allow the machine to cool down before
starting working on the machine
When burned, immerse in cold water immediately.
When the burn is severe, consult a physician as soon
as possible.
No smoking or open fire near the machine.
Be sure a fire-extinguisher is in the surroundings of
the machine.
No smoking or open fire near the machine.
Be sure a fire-extinguisher is in the surroundings of
the machine.
All moving parts of the system, including pulleys,
belts, chains, coolingfans, sprocketwheels, vacuum-
doors and cylinders presents a potential danger.
Be careful with covers and doors. Always pay atten-
tion to opening and closing.
The vapours in the board preparation module are
chemical.
Also the dust on the surface of the solderpot is dan-
gerous when inhaled.
Avoid inhaling this vapours / dust by using mouth
protection.
When working on the machine, always protect your
eyes with safety glasses.
Nitrogen
N
2
Follow the safety precautions and procedures
described in the
Material Safety Data Sheet
of
the Nitrogen supplier.
UPS
Uninterruptible
Power Source
When mainswitch is switched OFF,
always
switch
the UPS to OFF.
Signal light RED
- E-stop Active
Signal light GREEN
- Steady = Machine Run,
- Flashing slow = Machine not at setpoint, machine
stop
Signal light ORANGE
- Steady = Overload (outfeed full), Machine will
block,
- Flashing slow = Alarm
- Flashing fast = Critical alarm. Machine will block
If these rules are not observed it can cause personal injury and/or damage to the machine
SAFETY RULES
GENERAL INFORMATION
Содержание Vitronics Soltec DeltaWave 6622cc
Страница 4: ...iv ...
Страница 8: ... ...
Страница 30: ...INSTALLATION 22 CHAPTER 1 1 8 INSTALLATION SHEET See next pages ...