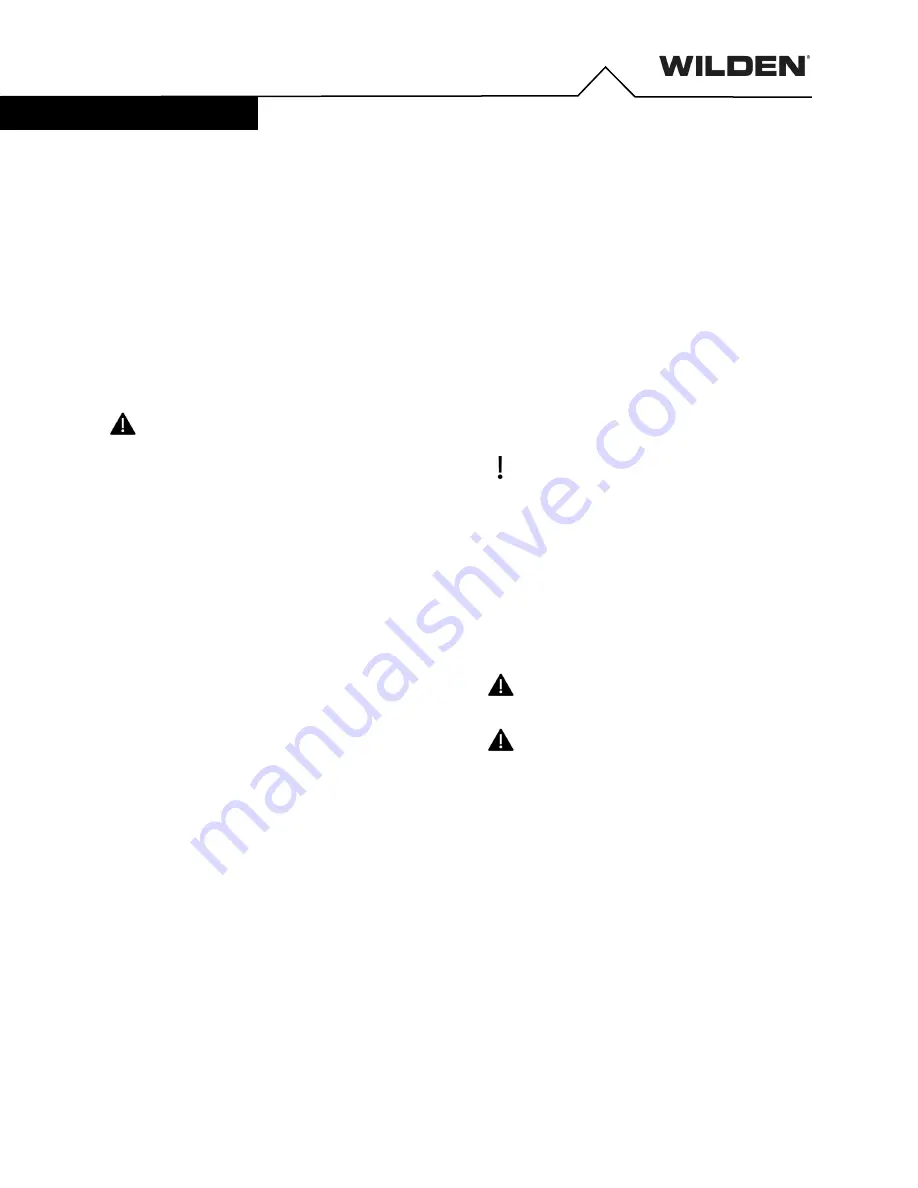
WIL-11113-E-04
10
HS430S High Pressure Bolted Metal
SECTION 6
W
ilden
pumps are designed to meet the performance requirements of
even the most demanding pumping applications. They have been
designed and manufactured to the highest standards and are available in
a variety of liquid path materials to meet your chemical resistance needs.
Refer to “Performance” for an in-depth analysis of the performance
characteristics of your pump. Wilden offers the widest variety of elastomer
options in the industry to satisfy temperature, chemical compatibility,
abrasion resistance and flex concerns.
The suction pipe size should be at least equal to or larger than the
diameter size of the suction inlet on your Wilden pump. The suction hose
must be a non-collapsible, reinforced type because these pumps are
capable of pulling a high vacuum. Discharge piping should also be equal
to or larger than the diameter of the pump discharge, which will help
reduce friction losses.
CAUTION:
All fittings and connections must be airtight.
Otherwise, pump suction capability will be reduced or lost.
Months of careful planning, study and selection efforts can result in
unsatisfactory pump performance if installation details are left to chance.
You can avoid premature failure and long-term dissatisfaction by
exercising reasonable care throughout the installation process.
Location
Noise, safety and other logistical factors usually dictate where equipment
will be situated on the production floor. Multiple installations with
conflicting requirements can result in congestion of utility areas, leaving
few choices for additional pumps.
Within the framework of these and other existing conditions, locate every
pump in such a way that the following six key factors are balanced against
each other to maximum advantage:
Access:
First, the location should be accessible. If it’s easy to
reach the pump, maintenance personnel will be able to perform
routine inspections and adjustments more easily. If major repairs
become necessary, ease of access can play a key role in speeding
the repair process and reducing total downtime.
Air Supply:
Every pump location should have an air line large
enough to supply the volume of air necessary to achieve the
desired pumping rate. Use up to a maximum of 5.9 bar (85 psig) air
supply pressure.
Solenoid Operation:
When operation is controlled by a solenoid
valve in the air line, three-way valves should be used. This valve
allows trapped air between the valve and the pump to bleed off,
which improves pump performance. You can estimate pumping
volume by counting the number of strokes per minute, and then
multiplying that figure by the displacement per stroke.
Muffler:
Using the standard Wilden muffler, sound levels are
reduced below OSHA specifications. You can use other mufflers to
reduce sound levels farther, but they usually reduce pump
performance.
Elevation:
Selecting a site that is well within the pump’s dynamic lift
capability will assure that loss-of-prime issues will be eliminated. In
addition, pump efficiency can be adversely affected if proper
attention is not given to site location.
Piping:
Final determination of the pump site should not be made
until the piping challenges of each possible location have been
evaluated. The impact of current and future installations should be
considered ahead of time to make sure that inadvertent restrictions
are not created for any remaining sites.
The best choice possible will be a site involving the shortest and
straightest hook-up of suction and discharge piping. Unnecessary elbows,
bends and fittings should be avoided. Pipe sizes should
be selected to keep friction losses within practical limits. All piping should
be supported independently of the pump. In addition,
the piping should be aligned to avoid placing stress on the
pump fittings.
Flexible hose can be installed to aid in absorbing the forces created by the
natural reciprocating action of the pump. If the pump is to be bolted down
to a solid location, a mounting pad placed between the pump and the
foundation will assist in minimizing pump vibration. Flexible connections
between the pump and rigid piping will also assist in minimizing pump
vibration.
If the pump is to be used in a self-priming application, make sure that all
connections are airtight and that the suction lift is within the model’s
ability.
NOTE:
Materials of construction and elastomer material have an
effect on suction lift parameters. Please refer to “Performance”
for specifics.
When pumps are installed in applications involving flooded suction or
suction head pressures, a gate valve should be installed in the suction line
to permit closing of the line for pump service.
Pumps in service with a positive suction head are most efficient when inlet
pressure is limited to 0.5–0.7 bar (7–10 psig). Premature diaphragm
failure may occur if positive suction is 0.7 bar (10 psig) and higher.
Single-Point Exhaust
Pro-Flo SHIFT pumps can be used for submersible applications when
using the Pro-Flo SHIFT's single-point exhaust.
CAUTION:
All Wilden pumps are capable of passing solids. Use
a strainer on the pump intake to ensure that the pump's rated
solids capacity is not exceeded.
CAUTION:
Do not exceed 5.9 bar (85 psig) air
supply pressure.
SUGGESTED INSTALLATION, OPERATION, MAINTENANCE
AND TROUBLESHOOTING