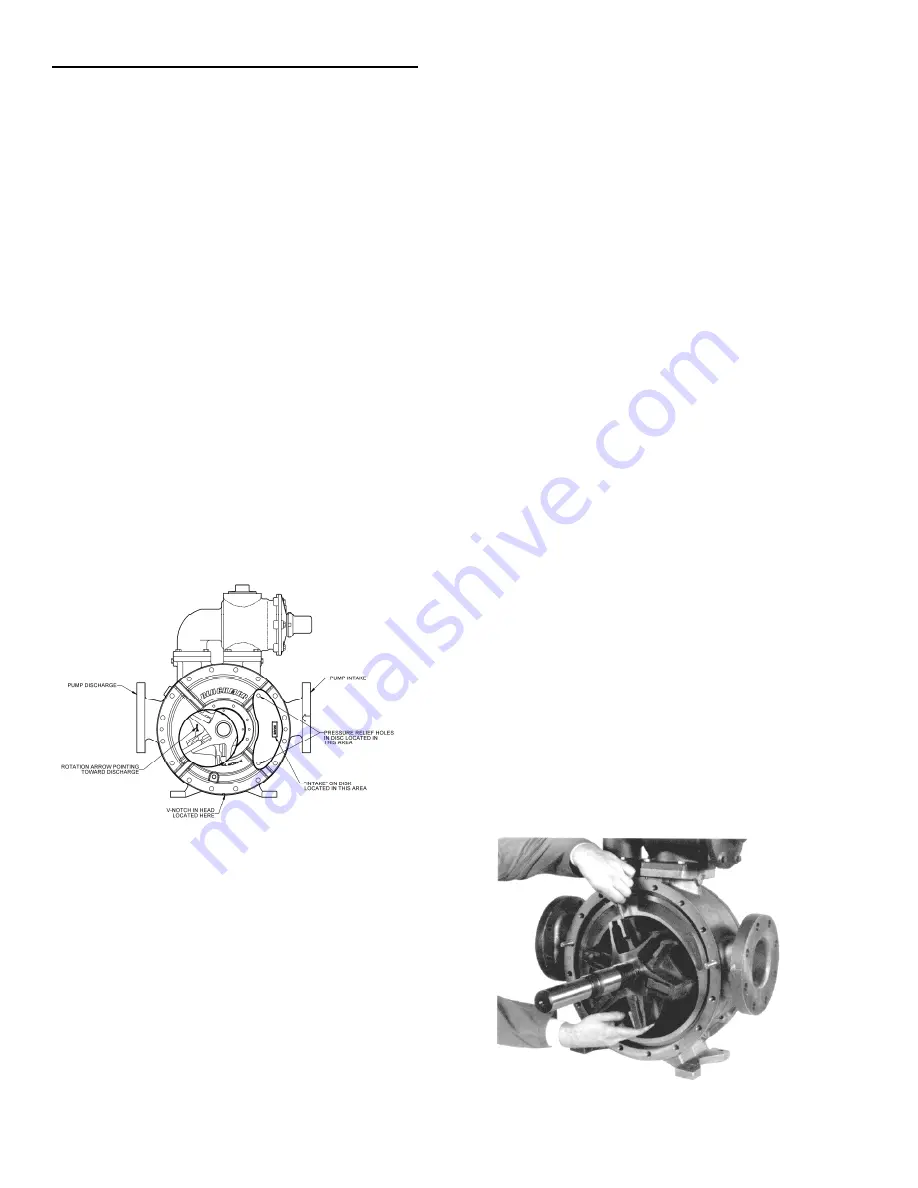
106-A00 Page 14/20
MAINTENANCE: MLN4B, MRLN4B
PUMP ASSEMBLY
Before reassembling the pump, inspect all component
parts for wear or damage, and replace as required.
Wash out the bearing/seal recess of the head and
remove any burrs or nicks from the rotor and shaft.
Remove any burrs from the liner (41).
1. LINER
–
The liner has a close fit with the casing (12);
take care to avoid finger injury during installation.
a. Align and start the liner (41) and liner key (74)
together into the pump casing. The word "INTAKE,"
which is cast into the liner, must be towards the
intake side of the pump. NOTE: The intake port is
marked with an inward facing arrow.
b. Lightly tap the outer edge of the liner with a plastic
or lead hammer to fully insert it into the casing.
2. DISC
–
Before the disc is attached to the head,
make sure both surfaces are clean and smooth.
Gently file away any burrs or rough spots.
a. Place a disc (71) on the head (20 or 20A) with the
counter-bored screw holes facing up.
b. Position the disc so that
when the head is
mounted
with the drain hole and V-notch down,
the word "INTAKE" on the disc will be towards the
intake side of the pump. The two disc holes must
be in the 2 and 4 o'clock positions if the inlet is on
the right (see Figure 10).
c.
Install the four lockwashers (71B), tangs outward,
and machine screws (71 A) to attach the disc to the
head.
Figure 10
3.
HEAD ASSEMBLY
a. To mount the head assembly (20) to the casing
(12), first install the head O-ring (72) in the groove
formed where the disc meets the head.
b. Grease the entire chamfer on the pump casing
where the head O-ring will need to slide into
position.
c.
Place the head assembly (20 or 20A) on the studs,
with the V-notch and drain hole facing down
(towards the bottom of the pump).
d. Check to make sure the word "INTAKE" on the disc
is towards the intake side of the pump when the
head is mounted.
e. Install and tighten the two nuts (21C) on the head
studs.
f.
Install and tighten the head capscrews (21) uniformly,
making sure the head O-ring (72) slides into place
without damage.
4.
SLEEVE BEARINGS (Bushings) –
If the sleeve bearing
(24) has been removed from the hub (20C), a new bearing
must be installed prior to attaching the hub assembly to
the head.
a. To aid installation, heat the hub in an oven at 200°F
(93°C) before installing the bearing.
b. Place the bearing (24) in the bearing bore on the
inside face of the hub (20C) with the tapered end
inward.
c.
Using an arbor press, press the bearing into the hub
in one continuous motion, until it is flush with (or
slightly below) the inside face of the hub. Starting and
stopping the pressing motion may result in a cracked
bearing.
5.
HUB ASSEMBLY
a. Before attaching the hub assembly (20C) to the
mounted head (20), grease the three head chamfers.
b. Install the hub O-rings (72A & 72B), and slide the hub
(20C) onto the shaft with the V-notch of the hub
towards the bottom of the pump.
c.
Install and tighten the two hub capscrews (21D) to pull
the hub into place. BEGIN WORKING ON THE
OPPOSITE SIDE OF THE PUMP.
6. ROTOR AND SHAFT –
It is necessary to install the
bottom vanes and the push rods in the rotor while inserting
the rotor and shaft into the pump casing.
a. Partially install the rotor and shaft (13) into the open
side of the pump and through the bore of the installed
head (20). Be careful not to damage the disc face with
the shaft end.
NOTE: When installing the rotor and
shaft, the rotation arrow on the rotor must point in
the direction of pump rotation-towards the
discharge side of the pump when the arrow is
positioned directly below the shaft.
See Figure 10.
b. Keep part of the rotor (13) outside the casing (12) such
that the three bottom vanes (14)(rounded edge
outward) can be inserted into the rotor slots and held in
place while all three push rods (77) are inserted. See
Figure 11.
c. The rotor and shaft (13), with the three bottom vanes
(14) installed, can now be
fully
inserted into the casing
(12).
d. Install the remaining vanes (14) in the top positions of
the rotor.
Figure 11
Содержание PSG BLACKMER MLN4B
Страница 19: ...106 A00 Page 19 20 NOTES ...