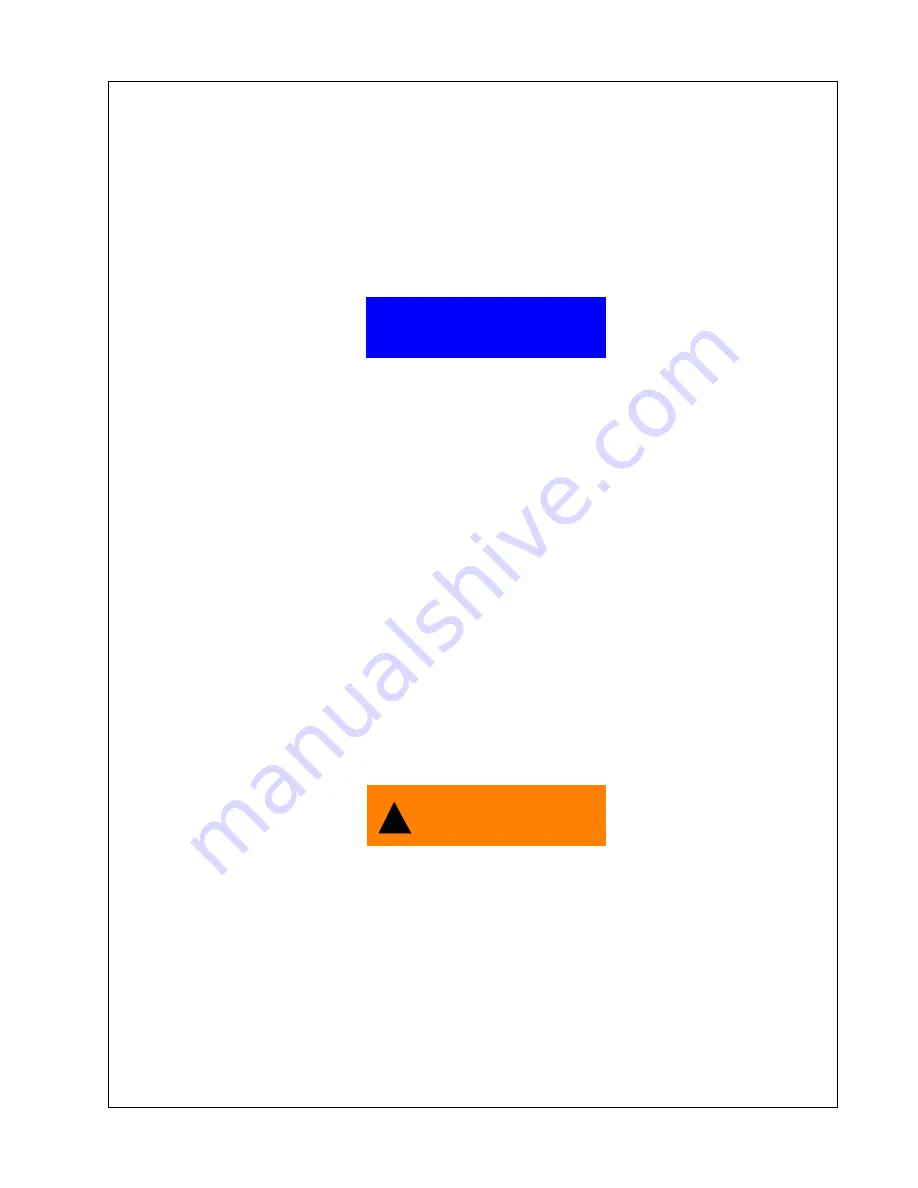
MAINTENANCE
Operating & Maintenance Manual
Book: 46553446 (3-15-2010) Rev A
47
Premature wear of both the engine and compressor is ASSURED whenever dust-laden air is
permitted to enter the engine’s combustion chamber or compressor intake.
The flexible hoses used in the fuel, oil and air lines on these units are primarily used for their
ability to accommodate relative movement between components. It is important they be
periodically inspected for wear and deterioration. It is also important the operator does not use
the hoses as convenient hand hold or steps. Such use can cause early cover wear and hose
failure.
NOTICE
Some of the air lines are nylon tubing. The associated fittings are “push-
in” design. Features are as follows:
Pulling on the tubing will cause the inner sleeve to withdraw and compress, thus tightening the
connection. The tubing can be withdrawn only while holding the sleeve against the fitting. The
tubing can be removed and replaced numerous times without losing its sealing ability.
To install the nylon tubing, make a mark (with tape or grease pencil) approximately 7/8 inch
from the end of the tubing. Insert the tubing into the sleeve and “push-in” past the first
resistance to the bottom. The mark should be approximately 1/16 inch from the sleeve, for the
3/8 inch O.D. tubing; 1/8 inch for the 0.25 inch O.D. tubing. This will ensure that tubing is fully
engaged in the sealing mechanism.
Compressor Oil Filters
The oil filter must be replaced every 500 hours of operation or six (6) months, whichever
comes first.
To service oil filters it will first be necessary to shut the unit down. Wipe off any external dirt
and oil from the exterior of the filter to minimize any contamination from entering the lubrication
system. Proceed as follows:
WARNING
!
High pressure air can cause severe injury or death from hot oil and flying
parts. Always relieve pressure before removing caps, plugs, covers or
other parts from pressurized air system.
1. Open the service air valve(s) to ensure that system is relieved of all pressure. Close the
valve(s).
2. Turn the spin-on filter element counterclockwise to remove it from the filter housing.
Inspect the filter.
3. Inspect the oil filter head to be sure the gasket was removed with the oil filter element.
Clean the gasket seal area on the oil filter head.
Содержание P260/HP220WYM
Страница 2: ...2...
Страница 5: ...Book 46553446 3 15 2010 Rev A 3 Foreword...
Страница 8: ...Operating Maintenance Manual Foreword 6 Book 46553446 3 15 2010 Rev A...
Страница 9: ...Book 46553446 3 15 2010 Rev A 7 DRAWBAR NOTICE...
Страница 11: ...DRAWBAR NOTICE Operating Maintenance Manual Book 46553446 3 15 2010 Rev A 9...
Страница 12: ...Operating Maintenance Manual DRAWBAR NOTICE 10 Book 46553446 3 15 2010 Rev A...
Страница 13: ...Book 46553446 3 15 2010 Rev A 11 Safety...
Страница 16: ...Operating Maintenance Manual Safety 14 Book 46553446 3 15 2010 Rev A...
Страница 18: ...Operating Maintenance Manual Safety 16 Book 46553446 3 15 2010 Rev A...
Страница 19: ...Safety Operating Maintenance Manual Book 46553446 3 15 2010 Rev A 17...
Страница 21: ...Safety Operating Maintenance Manual Book 46553446 3 15 2010 Rev A 19...
Страница 23: ...Book 46553446 3 15 2010 Rev A 21 Noise Emission...
Страница 28: ...Operating Maintenance Manual Noise Emission 26 Book 46553446 3 15 2010 Rev A...
Страница 29: ...Book 46553446 2 8 10 Rev A 27 GENERAL DATA...
Страница 32: ...Operating Maintenance Manual GENERAL DATA 30 Book 46553446 3 15 2010 Rev A...
Страница 33: ...Book 46553446 3 15 2010 Rev A 31 OPERATION...
Страница 43: ...Book 46553446 3 15 2010 Rev A 41 LUBRICATION...
Страница 45: ...Book 46553446 3 15 2010 Rev A 43 MAINTENANCE...
Страница 55: ...Book 46553446 3 15 2010 Rev A 53 Troubleshooting...
Страница 65: ...Revision History Rev Level EC Number Comments A B C D E SVC 31204 Original Release...