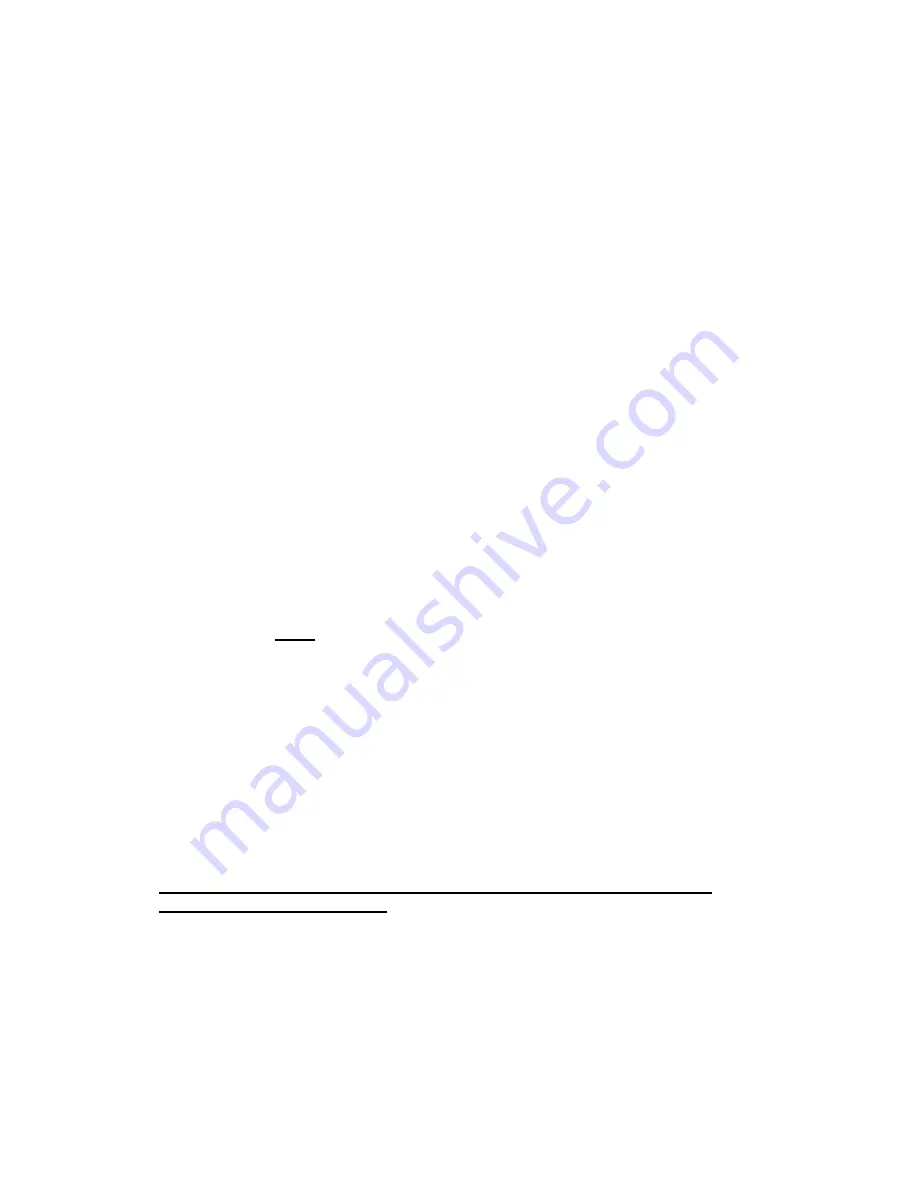
5
BOTTOM ENTRY
Connect to a suitable cold drinking water supply using 15mm copper pipe and
push on the ‘T’ piece supplied. The ‘T’ has been blanked off using a brass plug.
Leave this plug in place. Push the ‘T’ piece firmly onto the water inlet solenoid
pipe with the brass plug facing forward. Then push the 15mm cold water supply
firmly into the bottom of the fitting.
To avoid damage to the unit, do not use any solder connections whilst pipes are
connected to the boiler.
REAR ENTRY
For rear entry of cold water supply, remove the plug from the ‘T’ piece by
compressing the grey collar and pulling out. Push the plug firmly into the bottom
of the ‘T’ piece.
Push the ‘T’ piece firmly into the water inlet solenoid pipe with the ‘T’ facing the
wall.
Push the 15mm cold water supply firmly into the ‘T’ fitting.
To avoid damage to the unit, do not use any solder connections whilst pipes are
connected to the boiler.
OVERFLOW PIPE BOTTOM ENTRY
In your fitting kit you will find a straight push on connector with a small length of
15mm copper tube pushed into it.
This connector
must
be pushed onto the corresponding overflow pipe on the
bracket (alongside the solenoid).
If you wish to extend the overflow, remove the copper pipe supplied and replace
with pipe of your chosen length. The pipe must have a continuous fall and
should not be longer than 200mm (if a longer run is required use 22mm pipe to
avoid airlocks). The overflow pipe should have no more than four right angle
bends and should discharge to a safe visible position.
Under certain conditions, the overflow pipe could vent steam, hot water or cold
water and the manufacturers cannot be held responsible should damage arise
from such discharge if the overflow pipe has not been directed to a suitable
position where overflowing water can run away safely.
Under no circumstances should the overflow pipe be allowed to vent
inside the case of the boiler.