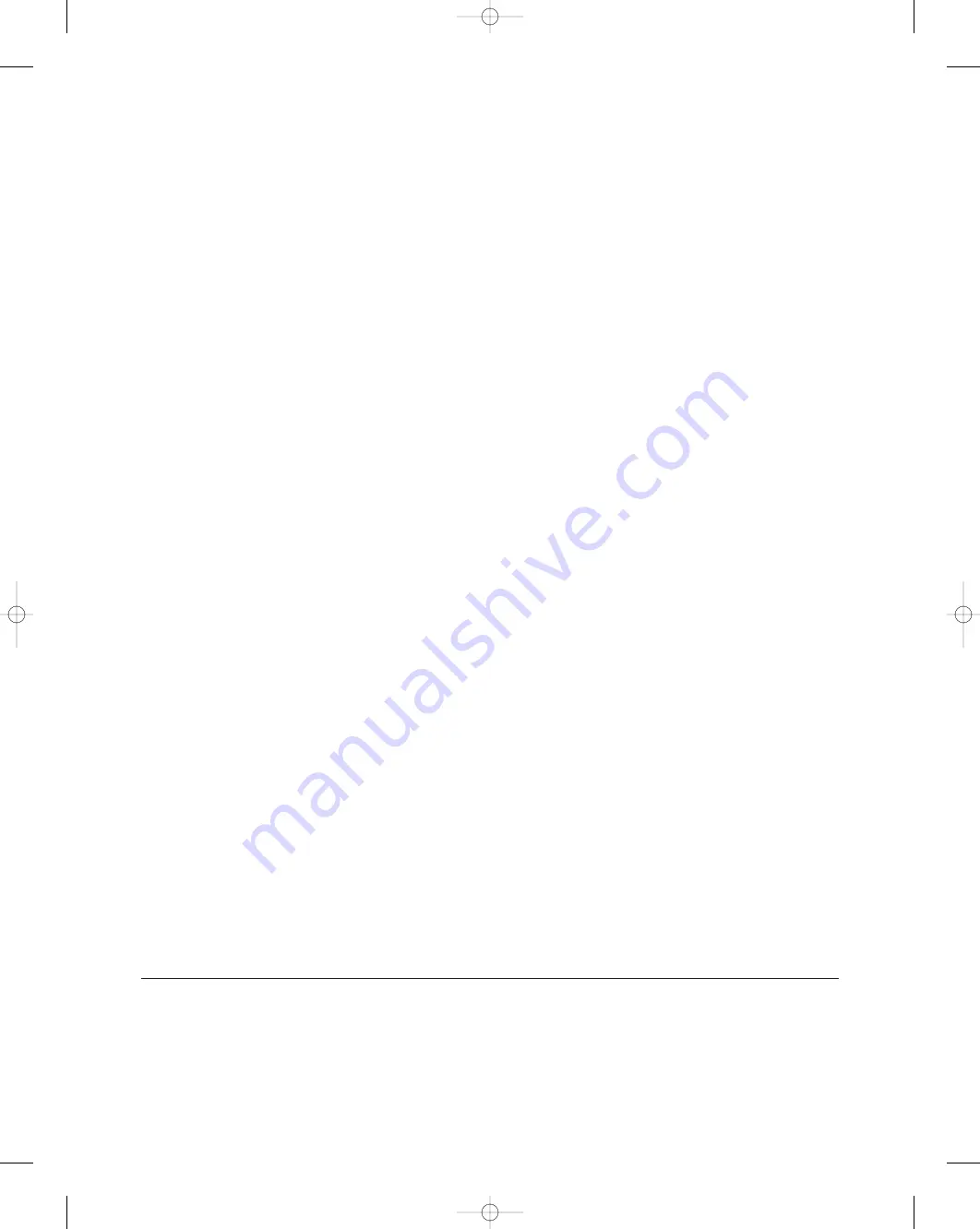
47
Technical Support
1-800-223-4570
removed the suspect shotshell, complete the stroke of
the handle you started.
Troubleshooting Section #2, Casefeeder
1. General casefeeder information: Capacity is 80
shotshells. Electric motor information: 110V AC for
US customers and 220V AC (3 RPM) for European
customers.
2.
The shotshells jam in the clear funnel.
Always
check the shotshells to make sure that no flattened or
stepped on shotshells get into the casefeeder.
Suggestion: Use the clear feed tube to gauge any
shotshell to make sure that it can slide through the
tube before placing it in the casefeeder bowl.
3.
It looks like half of a shotshell is hanging out of
the bottom of the casefeed body.
A shotshell can jam
in the casefeed body if the mouth of the shotshell is so
deformed that it gets stuck on the casefeed phish
inside the casefeed body. Simply remove the shotshell
by pulling it out.
4.
I have noticed that the microswitch does not
shut the motor off.
The microswitch uses the pressure
of the shotshell against the aluminum arm on the
switch to turn the motor off. You can bend the
aluminum arm as needed to assure that the switch is
activated.
Troubleshooting Section #3, General
1.
It’s important that you make complete, full
strokes of the operating handle when using the SL
900.
2.
Never use any solvent-type lubricants such as
Brakefree or WD-40. These will cause the mainshaft
to seize in the main bore.
3.
When I operate the machine, some shotshells
get stuck and strike the mouth of the sizing die.
The
shotshells may have a deformed rim or base. Throw
the bad shotshells away.
Another possible cause is that a shot pellet may
have fallen into the pocket area, stopping the
shotshell from feeding in to the shellplate. Inspect the
shellplate grooves for any smashed shot or other
debris.
4.
The operating handle stopped halfway through
its stroke.
The first thing to do when this occurs is to
tap every shotshell. See if you can feel which one is in
a bind. It may be that the primer is not fully seated
into the shotshell.
It’s important that you make
complete, full strokes of the operating handle when
using the SL 900.
It may be that the first shotshell has struck the
mouth of the sizing die, or a wad or smaller gauge
shotshell is stuck inside the first shotshell and has
jammed itself onto the depriming pin. Or it may be
that a wad has not entered the shotshell properly and
is caught on the mouth of the shotshell.
Whatever the cause, remove the suspect round by
lowering the shotshells out of the dies, then remove
the problem round from the machine.
5.
I’m not sure if the powder charge is correct.
Always use a reputable loading manual. The powder
bar does not come set from the factory. You must use
a scale to adjust the weight of the powder charge
being dispensed. The machine manual has detailed
instructions on how to set up the powder measure.
6.
When I use the machine some of the wad petals
get caught and fold beneath the shot tube.
Then a
spill might occur because the shot is too high in the
shotshell. Always inspect the wads before you place
them into the wad seater. You can use your thumb to
press the petals open, then insert the wad into the
wad seater.
7.
How do I remove that last amount of shot from
the shot bar?
When all the shot has been drained out
of the large hopper, place a plastic container or coffee
can next to the shot dispenser drain. Rotate the plastic
shot drain with your index finger and hold it there
until all the shot has emptied. Any remaining shot in
the shot bar (#16738) and dispenser can be removed
by running a hull through the machine.
8.
When I cycle the handle the wad swing arm hits
the edge of the toolhead as it tries to go thru the hole.
We have placed an adjustment set screw below the
foot of the wad swing arm inside the platform
(#13789, see the schematic on page 10). Using a 1/8”
Allen wrench turn the screw as needed to center the
wad swing arm in the hole it passes thru in the
toolhead.
9. The shot dispenser and the powder systems use
a 10-32 thread kep nut (#13817). These nuts may
become loose over time and should be replaced with
Nylock nuts (#13841).
10. The shot dispensing tube (#17479) is designed
to flex during operation. Do not shorten the tube for
any reason or it will no longer function as it was
designed to.
NOTE:
All electrical/electronic components in Dillon
equipment are covered by a one year warranty.
SL 900, May 2007 5/21/07 11:51 AM Page 47