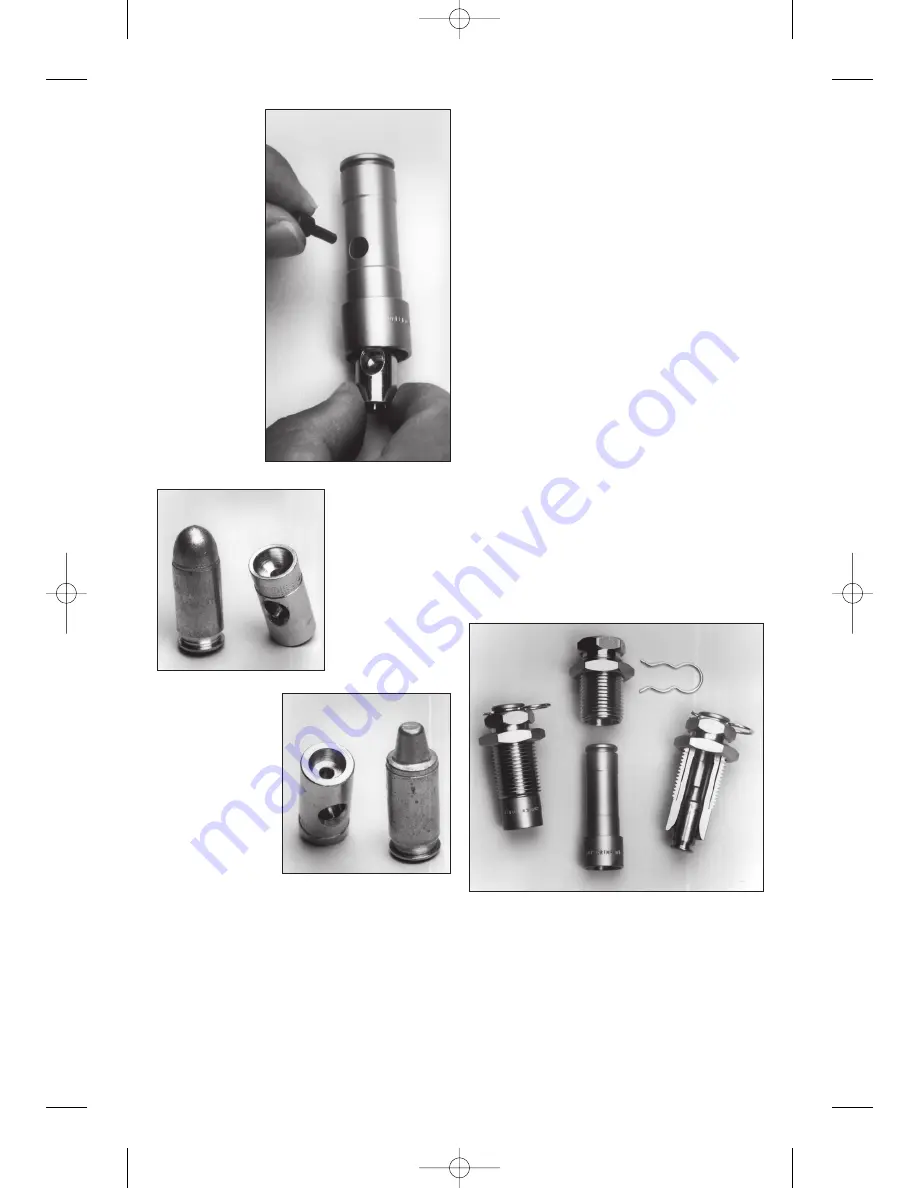
Fig 6. The
double-ended
seating stem
can then be
removed for
cleaning or
changing by
pushing out
the black cross
pin. Note that
the seat stem
is doubled
ended and can
be reversed to
match the
shape of your
bullet.
Figs 7 & 8.
Choose the
seating stem
which best fits
your bullet.
Fig 7 is the round
nose seating stem
and Fig 8 is the
semi-wadcutter
seating stem.
When the
desired configu-
ration is found
push the stem
back into the
insert and
replace the cross
pin. Reinsert the
seating insert
into the die
body. Replace
the clip and pro-
ceed.
Adjustment.
Place a sized
and belled case
into the seating
station of the
shellplate.
Next place a bullet on the mouth of the
case and cycle the handle down. Screw the
die down until it makes contact with the
bullet. Raise the handle a small amount and
screw the die down 1/2 turn. Cycle the han-
dle down and raise it to the top. Remove the
case with the partially seated bullet and
measure the overall length with dial
calipers.
Compare the length to that suggested in
your loading manual. If the OAL is too long
turn the seating die down in 1/8 turn incre-
ments and cycle the handle again.
Repeat the above process until the proper
seating depth is achieved.
Note:
One full turn of the die is approxi-
mately 0.070 of an inch. As you get closer
to your desired length do not turn the die
down in more than 1/8 turn increments.
When the desired OAL has been achieved
snug the lock ring while the cartridge is in
the die.
Crimp adjustment.
Place a belled case
with a seated bullet into the crimping station
of the shellplate and, with the die out of the
toolhead, cycle the handle down. Leave the
handle down and start the die into the tool-
head. Screw the die down until it contacts
the case.
Now, raise the handle (to pull the car-
tridge part way out of the die), screw the die
down 1/8 of a turn and then lower the han-
dle again. Remove the case from the die and
check for the proper crimp. (Note: refer to a
loading manual for proper crimp dimen-
sion.)
If your case is not crimped enough,
place the cartridge back into the shellplate
and repeat your adjustments in 1/8 turn
increments until you achieve the proper
crimp.
Fig 9. Crimp die assembly. On the left the
completed assembly is shown before screw-
ing it into the toolhead.
IMPORTANT Now is the time to try this
round to see that it fits the barrel or cylinder
of your gun. Also, if you’re loading for a
semi-auto, it’s a good idea to load 10-20
rounds and fire them. It’s depressing to load
a thousand rounds and then find out they
won’t function the action of your gun.
Fig 6
Fig 7
Fig 8
Fig 9
Dillon Die Instructions, May 2007 5/22/07 1:47 PM Page 3