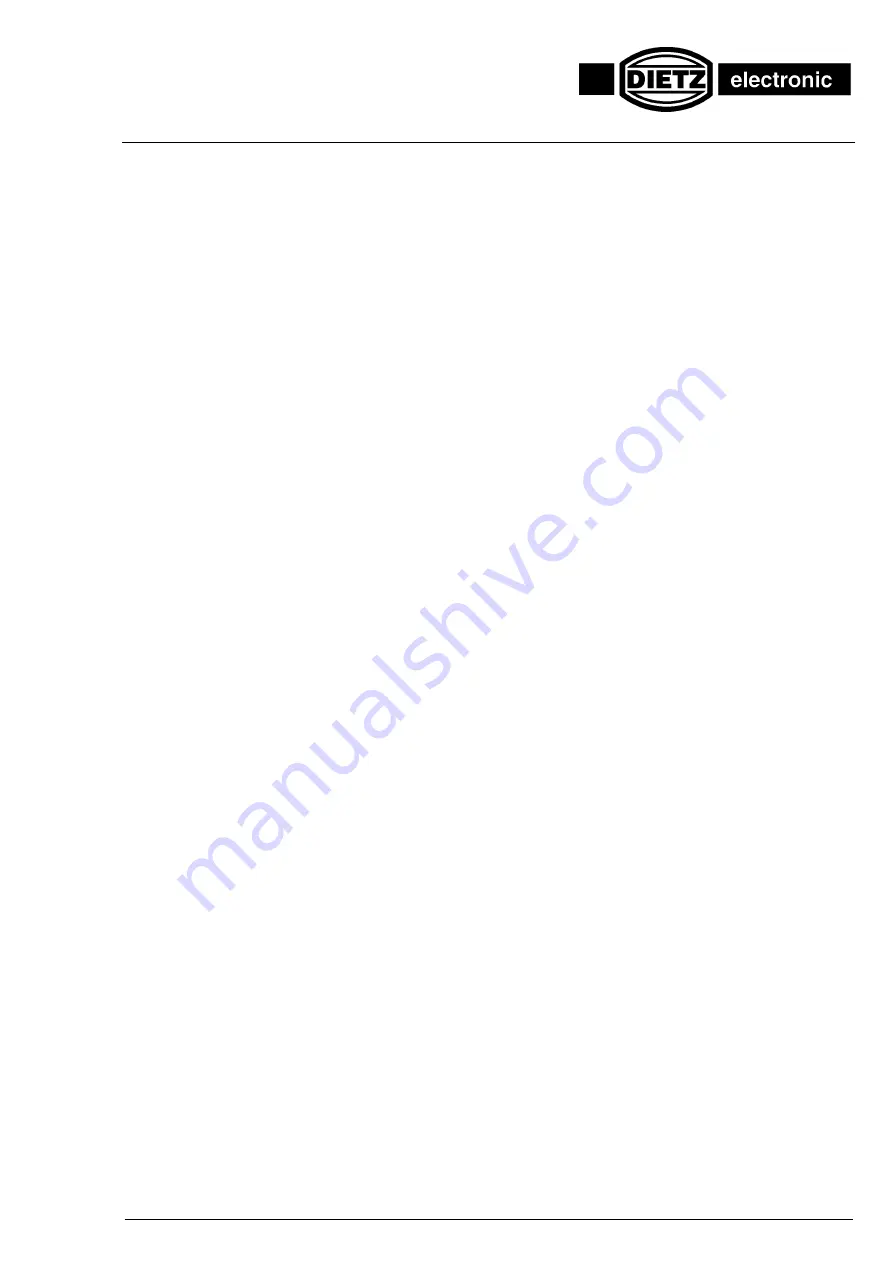
VECTORDRIVE DSV 5444
Top technology in drive electronics
07.07.04 10:12
Dietz-electronic
page 31 of 60
Motor output inadequate. Motor does not produce load.
♦
Check rotor flow F0 and rotor time constant T. Measure motor voltage with a moving-iron instrument if
necessary and set parameter F0 to produce half the motor voltage when idling.
♦
The optimum setting for the rotor time constant T is achieved when the minimum current is required for
maximum motor torque (the poorer the cos f value of the motor and the smaller the construction size, the
lower the value of "T").
♦
Check motor terminal block for correct circuit (star/delta connection).
Rotary field function test
♦
If not factory-set, the VECTORDRIVE DSV 5444 frequency inverter parameters should be set by means
of the automatic parameter-setting facility (terminal program Shift-F7) based on the motor rating plate.
Then connect the control system ("E" command). The motor should stay silent and a slight whistling
sound should be audible (cycle noise of frequency inverter). If after switching on the error message I
2
dt
appears, the motor rotary field to transducer rotary field assignment is incorrect. In this case, the rotary
field of the motor should be changed by interchanging two connecting lines on the motor. If this does not
produce the required result, the transducer must be checked (see "I
2
dt" fault in the troubleshooting sec-
tion). It is advisable to heavily reduce the current limit for the test ("S" command) (e.g. S = s
max
/10) to keep
the current load on the motor low. In this case the motor will oscillate or vibrate if the rotary field is incor-
rect.
Motor reacts independently of setpoint value at very low speed and draws high current levels
☞
Attention: In the case of high current and low speed, the signal A6 is active for some seconds
what means the torque curve (TER.EXE) runs to the limit. This state causes a strong overload-
ing of the motor and the converter. Stop the drive
immediately
and search for the error!
♦
Rotary field on motor incorrect or rotary position transducer not running with motor.
♦
Pole number "F31" incorrect
♦
Transducer point number not suitable (1024 1Vss is standard)
♦
Change two motor phases
Rotary position transducer error message or erratic running
♦
Cable wired incorrectly (no screening)
♦
TTL type rotary position transducer fitted instead of 1Vss
♦
Rotary position transducer faulty
♦
Coupling faulty or transducer screen not provided on both sides
♦
Pin 12 on connector X3 must have connection to DSV PE.
Motor hums when static or buzzes loudly at low speeds
♦
Gain values too high
♦
Reduce P value of stopping, starting and running.
External 24 V voltage supply short-circuited as soon as an input is activated or connected on the DSV
♦
24 V level exceeded by more than 25%
♦
The fuse elements on the DSV have been activated
♦
Please return the unit to our factory for checking
Static message displayed although the motor is turning slowly
♦
Transducer coupling loose.