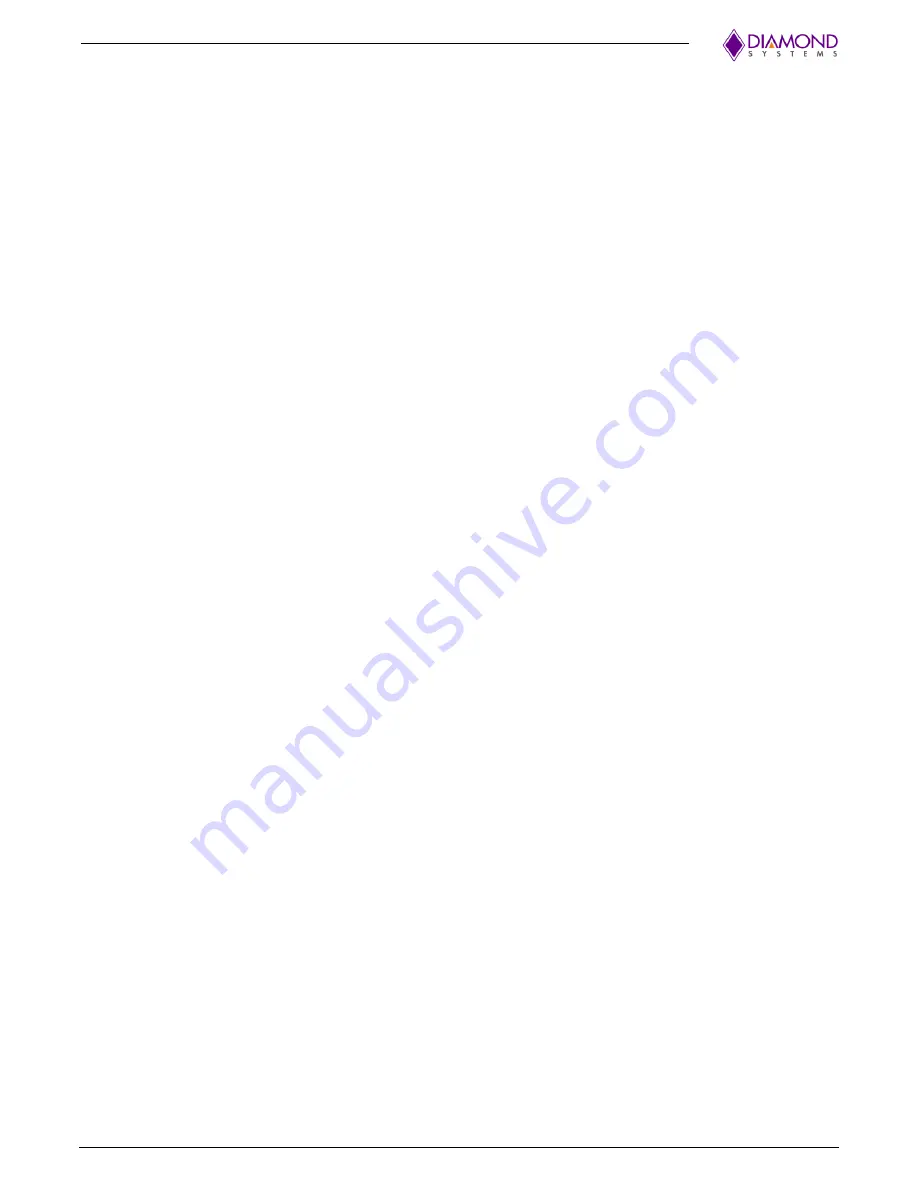
www.diamondsystems.com
Zeta User Manual Rev 1.0
Page 42
14.2.8
Measurement Accuracy and Calibration
Although the A/D circuit has 16-bit resolution (meaning it can resolve input voltages to within 1/2
16
or 1/65536 of
its input range), The measurement accuracy is not necessarily the same. All A/D circuits exhibit two inherent errors
known as offset and gain errors. In addition, all A/D circuits will experience some minor drift as the ambient
temperature changes, as well as lesser drift over long periods of time.
To minimize the size and cost of the A/D circuit while still providing reasonable performance, the A/D circuit on
Zeta base board does not provide calibration features to eliminate these errors. Instead the circuit was designed
to minimize the inherent offset, gain, and drift characteristics. The specifications at the end of this manual indicate
the worst-case offset, gain, and temperature drift errors in the circuit. Most boards will exhibit errors much lower
than these values (typically 25-50% of the published values), so the A/D measurements can typically be used
satisfactorily in your application without concern.
If higher accuracy is required, a software or digital calibration technique can be implemented in your application.
Measure two known voltages close to the lower and upper limits of the input range you are using. The ideal values
are between 1% and 5% at the bottom end and 95% and 99% at the top end. Compare the actual A/D readings of
these input voltages to the expected values, and then store the differences in a file. Then you can use these errors
to apply an offset and gain factor to each A/D reading on that board forevermore. Although this technique does
not eliminate temperature and drift errors, it will eliminate the largest portion of the total error and provide more
accurate measurements and better overall product performance.
When considering accuracy, it is important to consider all the contributions to measurement error. In addition to
the inherent A/D errors, the sensors connected to the A/D also have their own offset, gain, and temperature/time
drift errors. Usually these errors will be published as a simple accuracy figure in a percentage form. One percent
error on a 16-bit A/D is 655 LSBs, so if your sensor has a 1% error specification, that is already more than 10x the
typical A/D reading error, and therefore software calibration of the A/D readings alone will not provide any
material benefit. However, the same technique described above can be applied with the sensor connected using
known input conditions (for example empty scale and scale with a precision weight applied), so that you can
eliminate total system error.
To include A/D error values into the input voltage calculation, use this formula:
Input voltage = ((ADC
–
Cmin) / (Cmax
–
Cmin)) * (Vmax
–
Vmin) + Vmin
ADC = A/D code
Vmax = Test input voltage at top end of A/D scale used in calibration procedure
Vmin = Test input voltage at bottom end of A/D scale used in calibration procedure
Cmax = A/D code at Vmax input
Cmin = A/D code at Vmin input
This formula works for both unipolar and bipolar input ranges.
14.2.9
Input Impedance
Another factor that can significantly affect A/D measurement accuracy is the ratio between the input impedance
of the A/D circuit and the output impedance of the signal being measured. The voltage seen by the A/D converter
is a simple resistor divider between the two impedances, with the input signal at the top of the divider and the
A/D in the middle. The higher the output impedance of the input signal, the greater the error will be. Conversely,
the higher the input impedance of the A/D circuit, the lower the error will be. Zeta base board uses high
impedance, ultra-low-offset buffer op amps to boost the input impedance to well over 10 GigOhms (the input
impedance is calculated based on the specified input current of 75pA). This ensures that the source impedance of
any expected input signal will not have any material effect on the A/D readings.