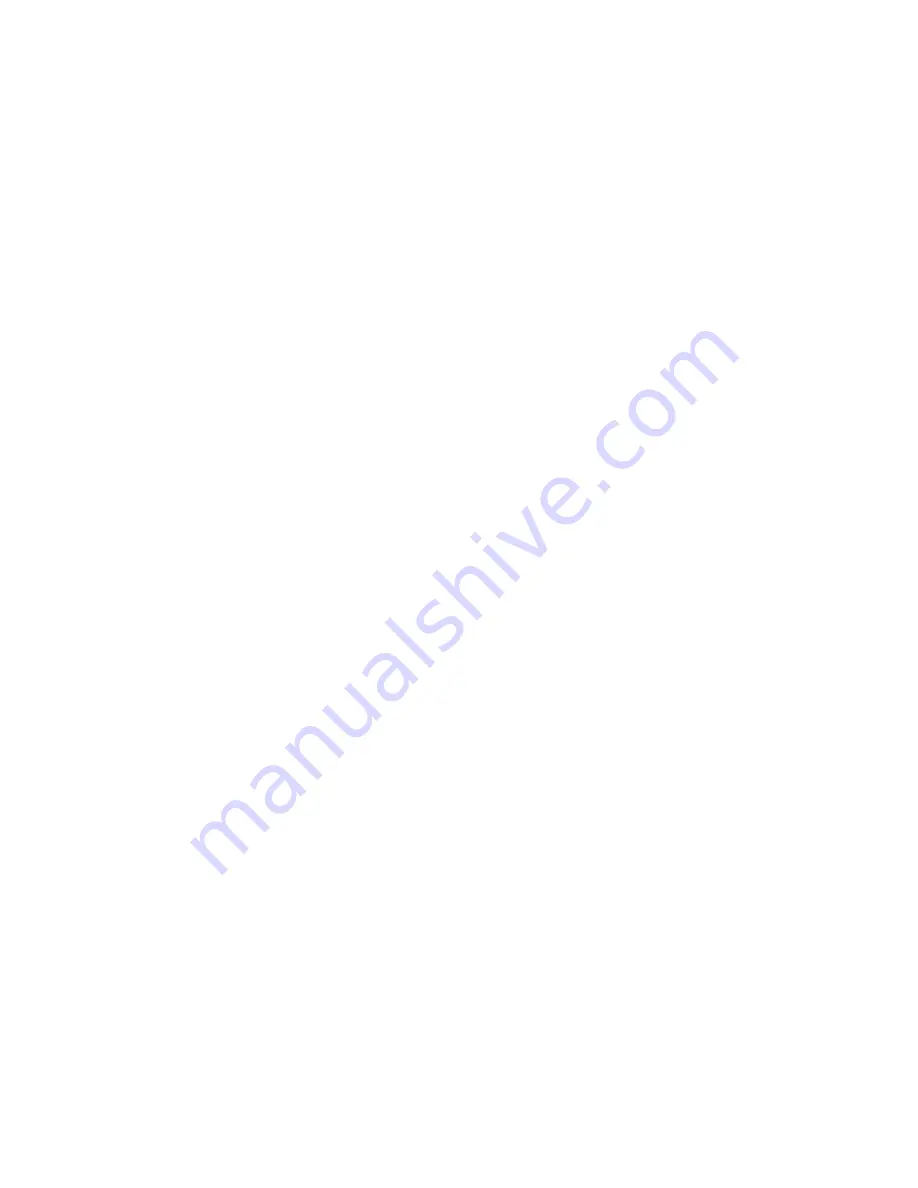
DSP-50 User Manual
Page 21 of 27
DSP50_MAN_A
Loop Configuration:
The size and shape of the loop will determine what type of vehicles it can reliably detect.
There are many variables that come into play including loop dimensions, percent of coverage, length of lead-in
wire, number of turns in the loop area, and detection height to name just a few of them. One common rule is
that the useable field height of a loop is 2/3 of the shortest leg of the loop. So if you plan on using a 2.5’ x 6’
loop, the expected useable detection height would be 20” (The shortest leg is 2.5’ or 30”, 30” x 2 = 60”, 60” / 3 =
20”). If the installation requires the detection of motorcycles as well as vehicles, the loop should go to within
one foot of the curb or roadway edge, whichever is present. If only motor vehicle detection is required, within
three feet of the curb or roadway edge is all that is required.
The number of turns to use in a loop is dependent on the size of the loop, the amount of metal (rebar, cables,
etc.), and distance from the loop to the detector. Rather than dive into all of the calculations to arrive at a
value, we will just use safe values. You can almost never have too many turns in a loop, only too few. For a loop
size of 2’ x 6’, four turns will be sufficient unless there is metal in the loop area. In that case add at least one
turn, and two if possible. As the loop size reaches 6’ x 6’, four turns will work for most all installations. If you
are unsure about your particular installation, call tech support for guidance.
Installation Practices:
Permanent loops should be installed into the road surface by cutting slots into the road
surface using a saw with an appropriate cutting disk for the road surface.
The slot cut should be wide enough that the wire being used will easily fit into the slot. This is needed so that
the loop sealant used can fully encapsulate the wire. When the wire fits tightly in the slot, the sealant may not
be able to get below the wire, leaving air pockets in the saw slot. If water finds its way in to these air pockets,
over time, freeze thaw cycles can slowly jack the loop out of the saw slot causing loop failure.
The saw slot should be deep enough that the loop wire will have a minimum of ½” of sealant over the top wire
in the slot. More is better. Going too deep with the saw cut is also a concern. Deep cuts in a road surface may
impact the structural strength of the roadway, especially if any reinforcement material is cut. Using a smaller
gauge of wire will allow for shallower saw cuts.
The corners of the loop should be crosscut at a 45
°
to help prevent damage to the wire insulation during
installation and temperature cycling. The angled cuts should be at least 9” back from where the corner would
be. The saw cuts should not go any further than necessary to insure that the saw slots are at full depth where
they meet.
Special consideration should be given to where the home run saw cut meets the loop saw cuts. Here either an
additional saw cut should be made as shown in Detail A or the inside of the sharp corner should be removed
with a chisel as shown in Detail B.
Once the saw slot has been cut, the slot should be cleaned of all loose material. High-pressure air should be
directed in to the saw slot to remove all debris. This will also help remove dust from the saw cutting operation
from the sides of the saw slot. This will allow better adhesion of the loop sealant to the saw slot.