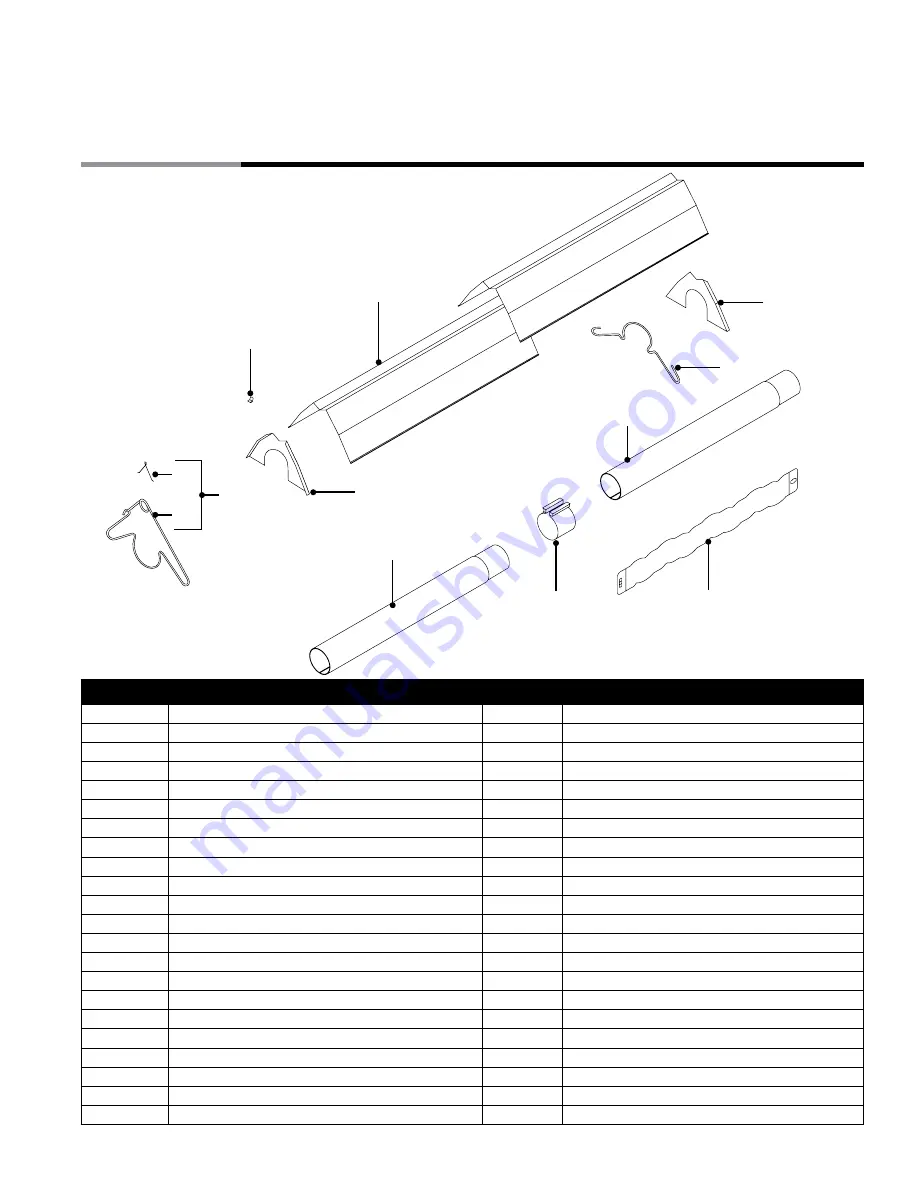
Basic Parts List
6.0
Parts
- GTD Series Installation, Operation, Maintenance and Parts Manual
39
Figure 6.2
•
Tube & Reflector Components
Part #
Description
Part #
Description
TP-615
220-240V 50/60Hz Fan
TP-3010
Service Panel Hinge
TP-628A
Red Indicator Light
TP-3011
Electrode Set Igniter Box
TP-628B
Green Indicator Light
TP-3012
Electrode Set Box Cover
TP-628C
Amber Indicator Light
TP-3014
Plastic Air Orifice Collar - Consult Factory
TP-633
Ball Valve Shut-off
TP-3033C
GTD Power Entry Plate
TP-635
4-Core Cable Wire
TP-3044
Gas Manifold
TP-638
Valve Main Coil Cord
TP-3060
Pressure Switch Mounting Bracket
TP-640B
230V Gas Valve Assembly
TP-3070
Low kW Burner (15-30 kW)
TP-651A
Circuit Control Board 0342G15B
TP-3072
High kW Burner (35-60 kW)
TP-652
JST Wiring Harness
TP-3093
#8-32 Cage Nut (Qty. 4)
TP-656
Ignition Filter
TP-3094
#8-32 x ½” Black Nylon Shoulder Screw (Qty. 4)
TP-664D
N.O. Atmospheric Pressure Switch - .10 (25Pa)
TP-3096A
Valve Compartment Bottom Panel
TP-664E
N.O. Atmospheric Pressure Switch - .14 (35Pa)
TP-3097A
Valve Compartment Top Panel
TP-664F
N.O. Atmospheric Pressure Switch - .20 (50Pa)
TP-3098
Valve Compartment Side Panel
TP-683
Stainless Steel Flexible Gas Connector
TP-3099
Controls Mounting Panel
TP-1018
Differential Switch Vinyl Sensing Tube (Exhaust)
TP-3580
Spark Burner Tube with Flange
TP-3001
Divider Panel
TP-3625
Picker Relay (Qty. 2)
TP-3002A
Left End Moulded Plastic Panel
TP-3646
AC Rectifier Voltage Cord
TP-3003A
Right End Moulded Plastic Panel
TP-3650
High Voltage Spark Wire
TP-3004
Main Control Box Panel
TP-3651
230 VAC Pactrol Circuit Board
TP-3005A
Control Box Chamber Moulded Plastic Lid
TP-3652
Wiring Harness
TP-3008
Gas Valve Mounting Bracket
* Optional upgrade or add-on item.
106
26A/B/C/E*
21B, 220
20C/D*
82
26A/D*
65I
105
105
19B
113
579